Stay Flexible Safely with Leuze
April 27, 2023
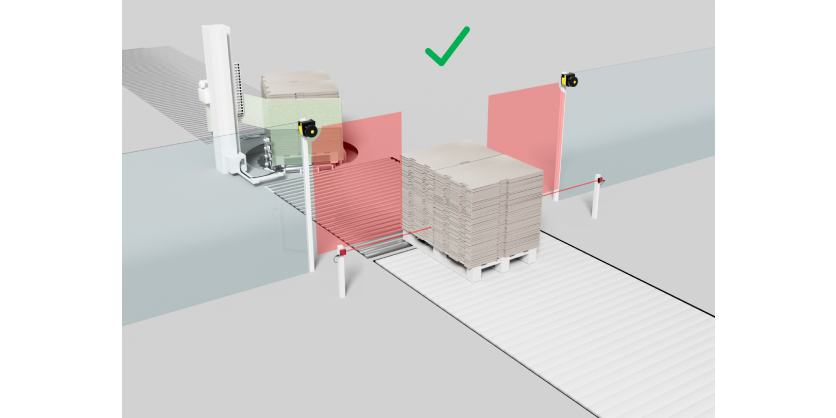
Different material widths, varying material positions or partially loaded pallets pose special challenges for transfer station access guarding. For this, Leuze relies on the concept of dynamic format adaptation. In this way, productivity and safety can be optimally harmonized.
Variation becomes a safety risk
Access monitoring on conveyor lines can be implemented with classic tried and tested safety concepts if the dimensions of the goods remain constant. These are mostly based on muting functions for automatic temporary bridging of the safety function. However, the area of application of the access guarding with muting function is limited.
If the width or position of the goods on the pallet or the position of the pallet on the conveyor varies, unmonitored safety gaps directly next to the goods can emerge. A person would then be able to access the danger zone. However, these gaps can be reliably closed with a safety solution tailored to them. The Leuze safety solution with dynamic format adaptation provides the right concept for this purpose.
Just triggering is not enough
A look at three examples of real-world situations illustrates the challenges of access guarding. The initial situation in all three cases: Pallets are automatically conveyed into or out of a danger zone using a conveyor line.
Example 1: The space next to the goods on the conveyor is larger than 200 mm.
Example 2: The goods have different widths and/or the pallets are occasionally only partially loaded, resulting in open spaces greater than 200 mm next to the goods.
Example 3: The position of the goods on the conveyor itself varies, which also results in large gaps next to the goods. The reason could be due to offset pallet positions on the conveyor or a missing pallet centering device depending on the application.
When muting is used, the goods would activate the associated muting sensors in all these cases. The protective function is then bypassed by the muting function. However, it is not always possible to comply with the specified normative framework conditions for lateral safety distances (< 200mm).
Measurement sensors and laser scanners cleverly combined
The Sensor People from Leuze offer a safety solution that closes these safety gaps: access guarding with dynamic format adaptation. For this, Leuze relies on a combination of safety sensors, measuring distance sensors and the associated safety program. The operating principle can be easily illustrated using the application described above. Two RSL 400 safety laser scanners are installed in the safety solution in front of the danger zone to safeguard the entry/exit point. Together they create a vertical protective field.
The safety laser scanners are extremely compact and powerful at the same time. Their high operating range of 8.25 meters makes it possible to monitor even extensive entry/exit points. Other important components of the safety solution from Leuze are two optical distance sensors. These are located in front of the protective field of the safety laser scanners on both sides next to the conveyor line. The distance sensors determine the width of the goods and thus also indirectly their position on the conveyor line.
Based on the information from the distance sensors, the safety system releases a “clearance window” in the protective field corresponding to the width of the goods. After the goods have completely passed through the opened window, the protective field is reset by the system to its original closed state. If goods are not only to be fed in but also discharged at one location, the system can be easily expanded.
For this purpose, only two additional distance sensors are required, which are installed behind the protective field – i.e. within the danger zone. Thus, the safety system works identically in both conveying directions. The entire process sequence, from distance measurement, protective field opening to resetting, is monitored in terms of safety by the solution’s safety program. All necessary configurations and parameters are individually adapted by Leuze to the needs of its customers.
Another issue for these applications is how the safety system behaves in the event of a deliberate bypass attempt by travelling on the goods. A function extension is also available for this scenario. However, further risk minimization using this additional protective measure is often not necessary, or the risk is already sufficiently minimized by existing protective measures. Here it is worthwhile to conduct an evaluation by means of an application-specific risk assessment. This could be conducted by the safety experts from Leuze, for example.
Overcoming the limitations of muting
The Leuze safety solution for dynamic format adaptation overcomes the limitations of conventional muting concepts. Material width and material position on the conveyor can vary without compromising on safety. The safety solution reliably detects people walking sideways next to the goods, as well as people walking ahead or behind. In this way, operators and manufacturers prevent dangerous situations while having the highest level of flexibility.
Productivity is also increased – as no further protective measures are required, the process in the danger zone can continue to run uninterrupted during the material transfer. Last but not least, this safety solution is easy to retrofit and provides optimum protection against deliberate or unintentional bypassing.
The way to a solution
As a reliable partner, Leuze is at your side in all project phases – from the coordination of requirements at the start of the project, through implementation, documentation and commissioning support, to final application validation and including legal security through CE conformity. This makes safety-related challenges particularly easy to implement for operating companies and manufacturers.
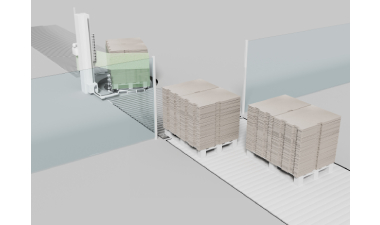

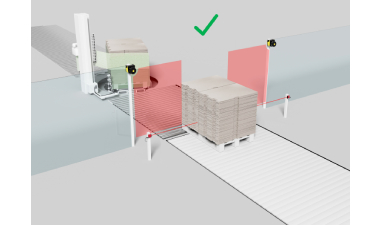
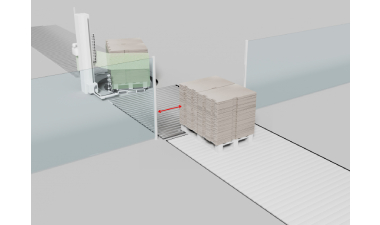
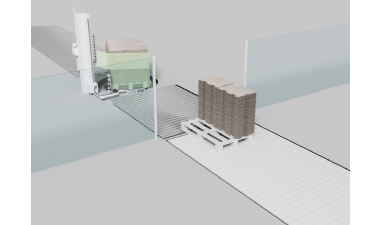
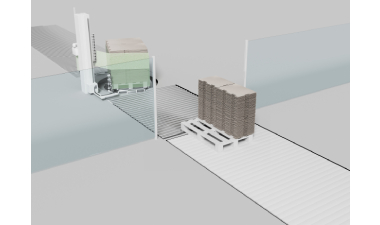
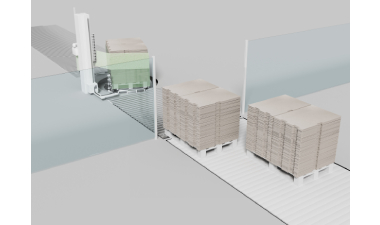
More Information
Related Product
Leuze Sets New Standard for Compact Positioning System
The AMS 100i from Leuze is one of the smallest laser positioning systems available on the market. This makes it the perfect solution for tight installations spaces.
Whether on the stacker crane, automated guided vehicle, or lifting system: In automated intralogistics, the sensors used for positioning applications must be able to operate on a small footprint in many cases. The new AMS 100i from Leuze is up to the task without sacrificing performance. With its small dimensions of 105 x 68 X 75 mm, it is one of the most compact laser positioning systems on the market. This makes it the perfect solution for use in tight spaces. The sensor works with very high accuracy: With the AMS 100i, users are able to position with millimeter accuracy for up to 120 meters.