SEW-Eurodrive’s MOVIPRO® Technology Decentralized Inverter
January 24, 2025
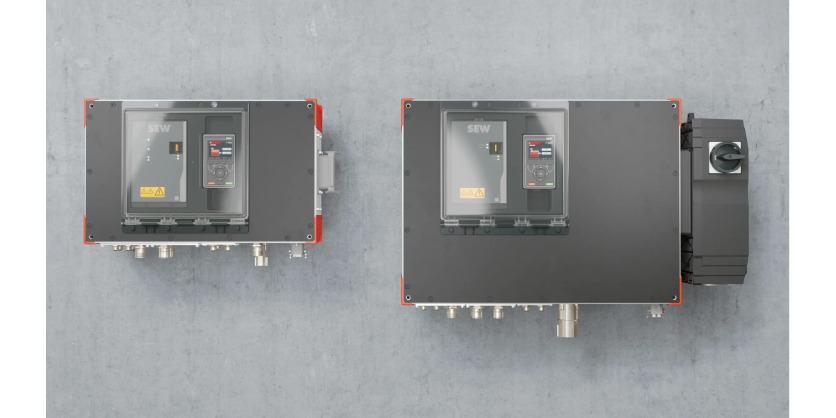
High-performance, flexible and scalable – the MOVIPRO® technology inverter combines the performance capability and range of options of the MOVIDRIVE® control cabinet platform with the installation benefits and robustness of decentralized technology. The decentralized inverter is the control-cabinet-free solution for modular automation.
Powerful universal genius
There’s a new addition to the decentralized technology portfolio in our MOVI-C® modular automation system – the new MOVIPRO® technology decentralized inverter is a real genius all-rounder and the perfect choice for your challenging tasks and applications.
The benefits for you
- End-to-end Thanks to the standardized MOVI-C® portfolio, which makes it very easy to decide between control cabinet and decentralized installation.
- Flexibility Since you can use the MOVIPRO® technology decentralized inverter to control any kind of motor in combination to any market-standard encoder system.
- Time saving Thanks to digital motor integration and plug-in connection technology.
- Power Since applications of up to 30 kW nominal motor power can be implemented.
- Scalable functional safety Since the perfect solution can be found for any requirement.
- Openness Thanks to standardized interface and predefined MOVIKIT® modules.
The MOVI-C® modular automation system at a glance
MOVIPRO® technology – high-performance, flexible, and scalable
MOVIPRO® technology is a decentralized inverter that can meet challenging requirements for applications. Alongside high-performance, scalable safety technology, it also boasts a positioning function with all standard motor encoders or external encoders. Thanks to its large power range of up to 30 kW, the decentralized inverter can also be used in lifting applications for heavy materials. The plug-in interfaces minimize installation outlay.
Facts about MOVIPRO® technology
Features
- Motor types: Can be combined with synchronous/asynchronous drives (with/without encoder) from SEW-EURODRIVE and third-party motors.
- MOVILINK® DDI: The digital motor interface with an electronic nameplate that includes all drive unit data. By eliminating the need for manual motor startup, this saves you valuable time and prevents any potential startup errors.
- Encoder evaluation: Evaluation of standard motor encoders (MOVILINK® DDI, sin/cos, TTL/HTL, RS422, HIPERFACE®).
- External encoder evaluation: Evaluation of standard external encoders such as distance encoders (EnDat, SSI, sin/cos, TTL/HTL, RS422, HIPERFACE®).
- Wide voltage input for global use.
- Control modes:
- V/f: highly robust for asynchronous motors without encoders
- VFCPLUS: highly diverse for asynchronous motors with and without encoders
- CFC: highly dynamic for asynchronous and synchronous motors with encoders
- ELSM®: highly efficient for synchronous motors without encoders
Technical data
Series/design | ||||
MPX22.. | MPX23.. | |||
Size | 2 | 2E | 3 | 3E |
Weight kg | approx. 16 | approx. 18 | approx. 26 | approx. 28 |
Nominal output current A | 5 – 9.5 | 12.5 / 16 | 24 / 32 | 46 / 62 |
Nominal power kW* | 2.2 – 4 | 5.5 / 7.5 | 11 / 15 | 22 / 30 |
Connection voltage V | 3 x AC 380 V – 500 V (also available as IT network design) | |||
Digital and analog inputs/outputs | Up to 12 digital inputsUp to 8 digital outputs1 relay contactUp to 2 analog inputsUp to 2 analog outputs | |||
Brake control | Integrated brake control for DC 24 V (BMV5)Integrated brake control for AC 230 V, AC 400 V, and AC 460 V (BD1B)Integrated safe brake control for AC 230 V, AC 400 V, and AC 460 V (SBM)Optional: two integrated brake control systems for dual-motor operation (only with BD1B or SBM) | |||
Degree of protection | depending on the design: IP54/IP65 to EN 60529 | |||
Ambient temperature | -25 °C to +60 °C (reduction in performance from 40 °C) |
* In conjunction with asynchronous motors
You can find all the technical data and documents about MOVIPRO® technology here.
Areas of application
MOVIPRO® technology decentralized inverters are particularly well suited for applications with challenging requirements:
- Lifting/lowering conveyors in the automotive industry or intralogistics
- Scissor lift tables in the automotive industry
- Electrified monorail systems in the automotive industry
Communication/installation variants:
- DFC – Direct Fieldbus Communication (PROFINET, EtherNet/IPTM, Modbus TCP)
- DSI – Direct Systembus Installation (EtherCAT®/SBusPLUS,EtherCAT®/CIA402)
Topologies
From control technology to inverters and drives, whether centralized or decentralized, there are no language barriers with any of the components from the MOVI-C® modular automation system. Plan the design of your machines or systems with a single control, communication, or installation topology. Our hardware and software will slot seamlessly into place and simply get things moving.
Customized motion control applications are increasingly making use of the EtherCAT® CiA402 profile, including directly in the field, to control a number of drives using a field distributor. Whether you are utilizing this bus communication interface or a different one, you have unlimited combination options with MOVIPRO® technology. Find out more: From control and communication topologies to installation topologies
Digital motor and data integration
Single-cable technology for power supply and data transfer with digital encoder for synchronous and asynchronous motors
In fact, only one hybrid cable is required here for the data connection between inverter and motor. The digital MOVILINK® DDI data interface transmits performance, brake, encoder, and diagnostic data to the motor.
MOVIKIT® software modules
The “Drive” category includes MOVIKIT® software modules that are operated directly on the MOVIMOT® flexible decentralized inverter.
- MOVIKIT® Positioning Drive: MOVIKIT® Positioning Drive enables positioning applications with a standardized fieldbus interface.
- MOVIKIT® RapidCreepPositioning Drive: MOVIKIT® RapidCreepPositioning Drive is a software module for implementing classic “rapid/creep speed positioning” without a motor encoder.
- MOVIKIT® Velocity Drive: MOVIKIT® Velocity Drive allows you to use applications with velocity control and a standardized fieldbus interface.
Functional safety overview for the basic version:
- Integrated STO (Safe Torque Off) safety function to IEC 61800-5-2
- Safety Integrity Level 3 to EN 61800-5-2: 2017, EN 61508: 2010
- PL e to EN ISO 13849-1: 2015
- STO (Safe Torque Off) activated via binary control or safe communication
- Optional: Up to 2 integrated safe brake control (SBC) systems
Accessories
- Interface box Interface box with integrated maintenance switch enables rapid installation and quick unit replacement in the event of a fault
- Braking resistor Plug-in, external braking resistors for all sizes
- Sensor/actuator box
- Keypads The CBG11A and CBG21A keypads can be used for startup and diagnostics.
Find out more - FEA31A decentralized combibox Decentralized combi box for processing two SSI encoders for safe positioning functions
Certifications/conformity
- CE (Europe)
- UKCA (United Kingdom)
- EAC (Russia, Belarus, and Kazakhstan)
- UA.TR (Ukraine)
- UL
- CMIM (Morocco)
- RCM (Australia)
Related Story
Why Choose SEW-EURODRIVE VFD’S? Discover More
SEW-EURODRIVE’s decentralized drive technology has everything you need – compact drive units, decentralized inverters and motion controllers for field use – and everything can be easily combined and recombined as required. This is all possible because the standardized control and communication architecture forms the perfect pairing!