Schmalz: Gripper Update for Vacuum Tube Lifter JumboErgo
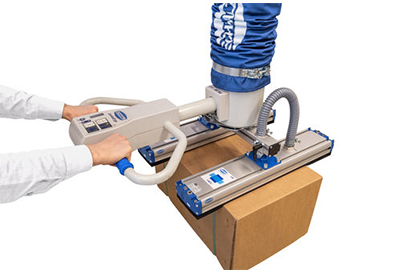
December 10, 2020
In mid-August of 2020, Schmalz introduced a new generation of area grippers for its vacuum tube lifters in the JumboErgo series. The FMP is hugely versatile and reliably grips heavy workpieces weighing up to 140 kilograms even when only part of the suction area is covered. It replaces the FM gripper. Thanks to its modular design, the FMP also provides a basis for extending the area gripper portfolio for the vacuum tube lifter Jumbo in the future.
The area gripper FM has been available for the JumboErgo for some time. It has now been fully replaced by the FMP generation. This area gripper may already be familiar to some: It has long since proven itself as an end-of-arm tool in vacuum automation. J. Schmalz GmbH is now bringing this successful concept to manual handling.
The new area gripper FMP is available in two lengths: 442 and 640 millimeters. It can be connected to the beam both lengthwise and crosswise. The beam connects the area grippers with the control handle and allows for the continuous adjustment of the grippers within this range. The FMP has a modular design. The base section is made from aluminum, and the easy-to-replace sealing foam with integrated filter protects the suction cup from dirt.
In comparison to the FM variant, the effective area is increased by up to 32 square centimeters thanks to its new dimensions and optimized hole pattern. In contrast, the application itself remains the same: Both its behavior and area of use correspond to the FM system. That means the FMP is ideal for safely handling sheets with cut-outs, pallets or other workpieces with inconsistent surfaces. The new area gripper also makes it easy to switch between full-surface and partly covered gripping, for instance, for loading machines ergonomically and then removing the cut-outs. The vacuum provides reliable gripping, even if the suction area is not fully covered.