Click and Customize Robotic Welding is Finally Here. Get Started Fast with Six Customizable Models!
January 16, 2025
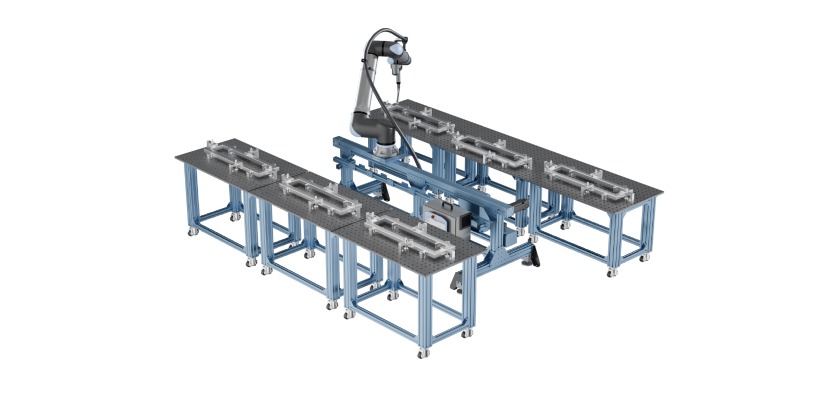
Easy-to-Customize Solutions for Quick ROI
Build, simulate, and deploy robotic welding solutions in days. No programming knowledge needed.
Why Robotic Welding?
Vention’s modular approach to robotic welding solves labor and throughput challenges and ensures flexibility for the future. Build your welding cell based on your needs and space constraints, with the flexibility to choose components, robots, and software that you need to boost productivity. You can even use your own welding gun. From design and procurement, to deployment, everything can be done on a single platform with complementary engineering support!
Welding Solutions Optimized for the Real World
Three Reasons to Adopt Robotic Welding
1. Alleviate Welder Shortage
Boost productivity by moving skilled tasks to your welders and time-consuming jobs to a welding robot.
2. Ensure Consistent Quality
Improve weld quality with uniform torch position and precise weld path for each job.
3. Reduce Welding Costs
Reduce waste and downtime to achieve significantly lower costs per weld.
Start Your Automation Journey
Build Your Own Welding Solution
Start building a custom welding solution with Vention. Add plug-and-play components, software, and other essential features to get started.
1. Welding cart
Build a custom cart using the Vention ecosystem of aluminum extrusions and hardware. Already have your own cart? Build a pedestal to position the robot.
2. Table top & fixtures
Nitrided and black oxide-coated table plate. Heat-treated for durability, with a flat-ground surface for accurate setups. Resistant to weld spatter, rust, and scratches. Combine multiple table tops to create the welding surface you need.
3. Welding Robot
Select between a UR10e and UR20, based on the reach your application requires.
UR10e: Reach up to 51.2in
UR20: Reach up to 68.9in
4. Protection panels
Build protection panels using the Vention aluminum extrusions and tinted, transparent, impact resistant polycarbonate Tuffak® weld curtain panels.
5. Programming
Program your welding application using the easy and intuitive SmoothTool that includes a programming flange and URCap. Compatible with all welding power sources.
6. Other essentials
Use Pushbutton to start/stop your program, turn the arc on/off and e-stop your operation. Retrofit kits to integrate power sources to the Universal Robots controller. All provided by SmoothRobotics.
The Vention Difference
Smarter Robotic Welding, Powered by Vention
Customizable System
Build your welding cell based on your needs and space constraints, with the flexibility to choose components, robots, and software that you need to boost productivity.
Rapid Deployment
No more waiting for months to automate your welding operations. Design in minutes with real-time pricing, and get your robotic welding solution delivered in record time.
All-in-One Platform
Simplify your workflow with the support and convenience of integrated design, ordering, deployment, and operations tools. Eliminate risk with an ecosystem of 4,000+ plug-and-play parts.
Ready for Any Type of Welding
Explore Multiple Welding Cell Configurations
Visit Vention to explore their ready-to-use templates below, and start customizing today!
Related Story
Vention Introduces AI, Making Adoption of Automation Easier
Vention has been on a mission to democratize automation since 2016. Etienne Lacroix, Founder and CEO of Vention, realized he could leverage software and technology to productize automation, making it more accessible to everyone.