How to Select the Right Purge and Pressurization System
April 11, 2023
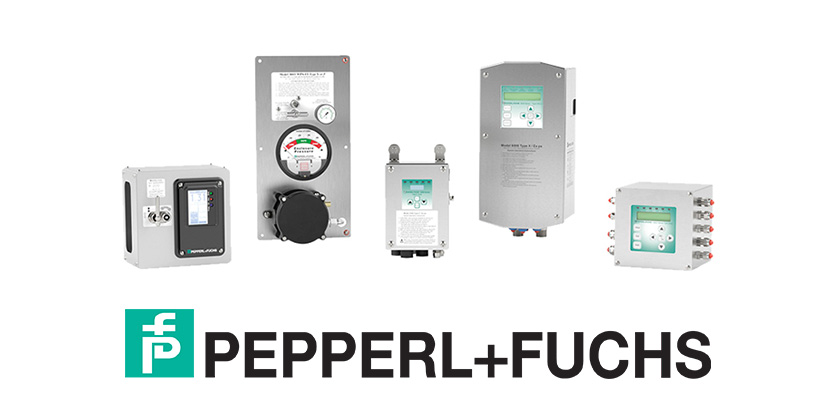
The explosion protection method purging and pressurization enables the use of non-explosion-proof electrical equipment and conventional automation components in hazardous areas. Special purge and pressurization systems flush the enclosure with an ignition protection gas and thus reduce the concentration of explosive gas or dust inside. Immediately thereafter, a positive minimum overpressure is maintained inside the enclosure, preventing the surrounding, potentially explosive atmosphere from entering.
Selecting the right system to protect your plant from ignition sources in potentially explosive gas or dust atmospheres can be a challenging task. First, one must consider the hazardous area classification, i.e. to what extent the planned area of application is at risk of explosion. The hazardous areas are divided into classes/divisions (North America) or zones (Europe). In addition, wiring and temperature are other factors that need to be taken into account.
Learn about the various types of Bebco EPS® purge and pressurization systems from Pepperl+Fuchs and how to select a system that best fits your application.
Selecting a Purge and Pressurization System Considering Class/Division or Zone
Purge and pressurization systems are designed according to NFPA 496, or ATEX and IECEx standards and regulations. The hazardous area classification determines which standards have to be followed and what system can be used. However, wiring, temperature, and material of the enclosure and the electrical equipment inside also need to be considered. For example, the wiring to and from the enclosure needs to be protected accordingly.
Class/Division Applications
For Class/Division applications, NFPA 496 provides the definition to the applicable types:
- Type X purge system allows for the use of electrical equipment suitable for unclassified locations within the pressurized enclosure for Division 1 applications. If a pressure loss occurs after purging and pressurizing the system, power to the enclosure must be disconnected. A timer is required for purging. The flow rate is based on a measurement at the outlet of the enclosure. A flow sensor is located on the vent at the outlet of the enclosure.
- Type Y purge system allows for the use of Division 2 rated electrical equipment within the pressurized enclosure for Division 1 applications. If pressure is lost after purging and pressurizing the system, an alarm shall be triggered unless power is removed. The operator can manually determine when to purge. The flow rate can be measured at the inlet of the enclosure.
- Type Z purge system allows for the use of electrical equipment suitable for unclassified locations within the pressurized enclosure for Division 2 applications. This type has the same pressure loss and timing requirements as Type Y. Another similarity to Type Y is that the flow rate can be measured at the inlet of the enclosure.
Zone Applications
For Zone 1/21 and Zone 2/22 applications, IEC 60079-2 provides the definition to the applicable types:
- Type Ex pxb purge system allows the use of ignition capable equipment inside the pressurized enclosure for applications in Zone 1 or 21. Its protection requirements are the same as those of Type X.
- Type Ex pyb purge system allows the use of Zone 2 or 22 electrical equipment within the pressurized enclosure for Zone 1 or 21 applications. Its protection requirements are the same as those of Type Y.
- Type Ex pzc purge system allows the use of ignition capable equipment within the pressurized enclosure in Zone 2 or 22 applications. The protection requirements are the same as for Type Z.
Pepperl+Fuchs System Offerings
The following chart gives you an overview of the different types of purge and pressurization systems available for your application and hazardous area classification.
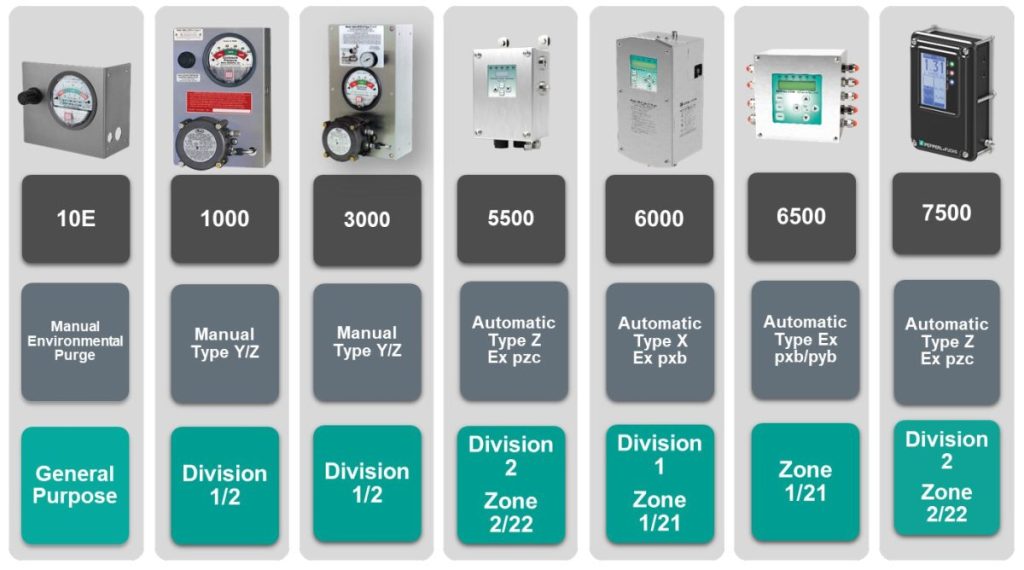
Pepperl+Fuchs offers manual and automatic purge and pressurization systems. The low-profile design of the systems allows for internal or external mounting. Outputs automatically perform temperature control and pressurization for leakage compensation. The systems also output various alarm signals as preventive error messages. The user interface is programmable to meet user requirements.
For detailed information on each purge and pressurization system, please visit the Pepperl+Fuchs website.
Configure your Purge and Pressurization System Online
To be certain, there is a variety of options for purge and pressurization systems. Therefore, we have created a quick configurator tool that will easily guide you to the right system that fits your application according to the area classification (Class/Division or Zone). You can then easily configure the purge control unit with the appropriate mounting variant, temperature control, power supply, wiring, and accessories such as manifold valve and pressure relief vent.
Configure your Pepperl+Fuchs Bebco EPS Purge and Pressurization System
Do you need support in configuring the right components or are you looking for a specific purge solution? Pepperl+Fuchs offers technical support worldwide and will be happy to assist you find the right solution.
Related Product
Register for Hazardous Area Training Programs with Pepperl+Fuchs
As an expert in hazardous area protection, Pepperl+Fuchs has applied their decades of experience and expertise in this field to build a portfolio of training modules. The diverse topics relate to the principles involved in applications in potentially explosive atmospheres. In addition, some of these modules can be customized specifically to the customer’s needs to provide a unique training experience.