Promise Robotics Transforms Automation in Homebuilding with Next-Gen Control Platform
December 11, 2024
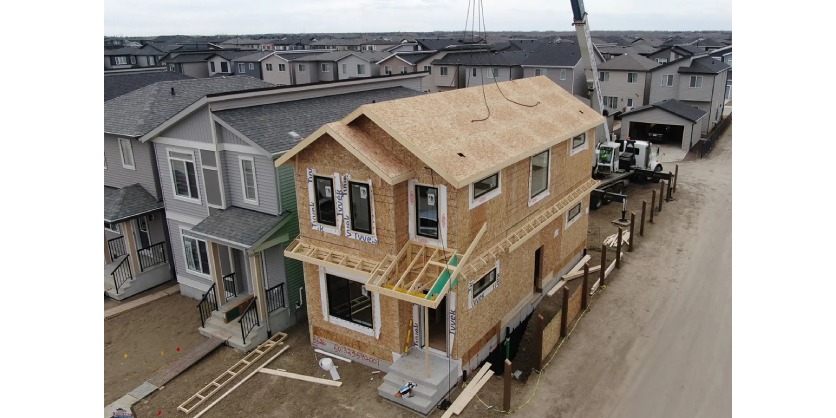
The AI-powered robotic system enables homebuilders to build more homes faster with less resources using flexible automation and distributed drive technology from Beckhoff
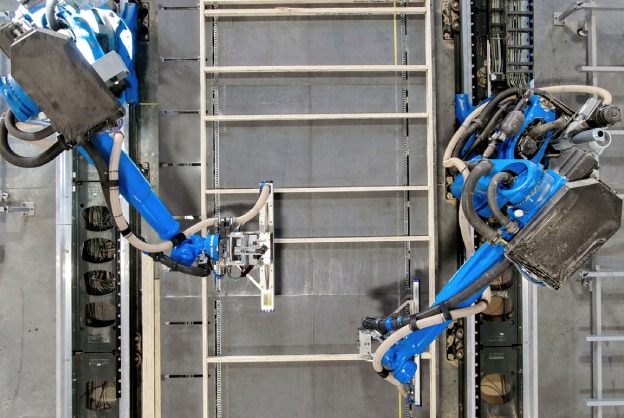
Imagine a world where affordable, sustainable housing isn’t a dream, but a reality. This vision faces two significant hurdles: skyrocketing construction costs and a shortage of skilled labour. These issues are making it harder than ever to build enough homes at a fast pace and reasonable price.
Enter Promise Robotics, a Canadian startup reinventing prefabrication by enabling builders to harness the power of AI and automation. The company is bringing the most intelligent, flexible, and compact industrial robotic systems for construction, powered by a proprietary cloud-based software platform that manages the entire production lifecycle from planning to factory floor operations, scheduling, and logistics. The platform introduces the concept of a Homebuilding Factory-as-a-ServiceTM, enabling customers to access expertise and advanced technology to streamline the building process.
By using the innovative Homebuilding Factory-as-a-ServiceTM concept, homebuilders can expect to dramatically reduce on-site assembly of homes by up to 70% compared to traditional methods. For example, a single-family home could be assembled in about five hours and a 64-unit, three-story apartment building in two weeks.
“Automation is not very common in the construction industry, which remains heavily labour-intensive,” said Ramtin Attar, CEO and co-founder of Promise Robotics. “Our goal at Promise Robotics is to build foundational technology – an automation system with a tangible return on investment and without limits for wide adoption.”
Nailing tough challenges in robotic homebuilding
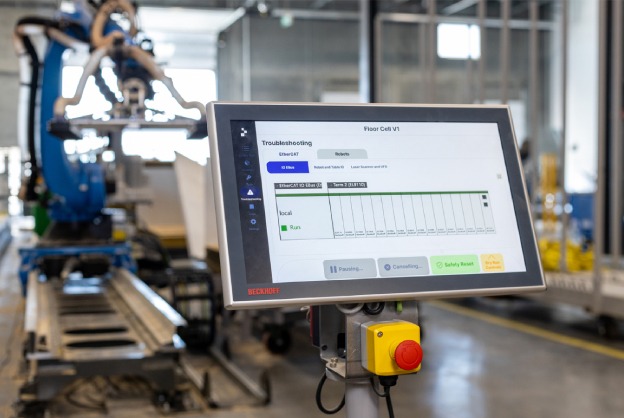
Developing Promise Robotics’ innovative construction systems presented unique challenges. These systems require a delicate balance—achieving precision and speed while still being able to adapt to the complexities of real-world construction methods and building codes.
A primary hurdle was the need for a robust, high-performance control system. Specifically, real-time processing was crucial for precise robot movement and feedback control. Traditional construction relies heavily on human judgment and expertise, even today, when the most experienced workers are retiring at a rapid rate. Robotic systems, however, are not an off-the-shelf replacement; they require constant feedback and precise control to ensure accurate execution.
“One of the key lessons we’ve learned is how to use perception to handle material variations that can occur during production,” explains Farid Mobasser, Director of Software at Promise Robotics. “We have to provide feedback to the robots and adapt to unique scenarios that might disrupt the process. It’s a continuous learning curve – we test and build different structures, shapes, and handle edge cases to improve our systems.”
Another key challenge was ensuring a compact, integrated design. Minimizing wiring and complexity was essential for facilitating quick deployment in a dynamic construction environments with limited space.
Laying a solid automation foundation using EtherCAT and Beckhoff
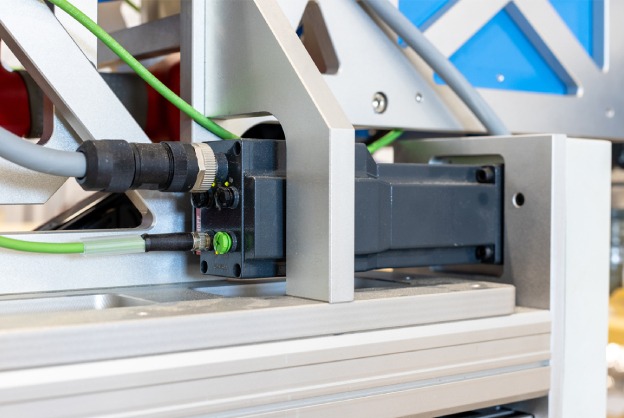
To address these challenges, Promise Robotics leveraged several Beckhoff products, including TwinCAT 3 automation software, and the high-speed EtherCAT industrial Ethernet system for data transmission between controllers, drives and I/O.
TwinCAT offers an end-to-end engineering and runtime platform for all automation functionality, from machine control logic and motion control to safety and HMI. The TwinCAT development environment allows Promise’s engineers to leverage a wide range of programming languages, including structured text, ladder logic, and C++ to rapidly build robust applications.
EtherCAT can handle real-time communication with minimal latency – a critical requirement for precise robotic control. Its high-speed performance seamlessly integrates motion control, safety functions, and other machine components, enabling Promise Robotics’ complex construction systems to operate smoothly in dynamic environments.
“The flexibility and scalability of EtherCAT was a big factor. It’s the fastest industrial Ethernet communication protocol, and Beckhoff also offers a wide complement of hardware. This includes everything from the CX2043 embedded PC to I/O fieldbus components and all drive technology, including motors, drives, cables,” said Darren Brix, Director of Hardware at Promise Robotics. “It’s a turnkey package that streamlines process and system design. EtherCAT really makes it simple and efficient to complete a harmonized, consistent industrial solution at a high standard.”
The CX2043 embedded PC (IPC), featuring an AMD Ryzen™ V1807B CPU with four cores and a clock speed of 3.35 GHz, is the backbone of Promise Robotics’ control system, managing the entire automated construction process and allowing seamless integration with all Beckhoff I/O components. Paired with TwinCAT automation software, the CX2043 becomes a high-performance PLC and motion control system, supporting both 32-bit and 64-bit modes, and providing precise, deterministic processing with the short cycle times needed for Promise Robotics’ automated systems.
A CP3924 multi-touch control panel, leveraging CP-Link 4, serves as the main interface for operators to control the robotic systems. This state-of-the-art touch screen interface provides intuitive control and monitoring capabilities, allowing operators to easily interact with and manage the automation system.
Building beyond the cabinet with distributed drive systems
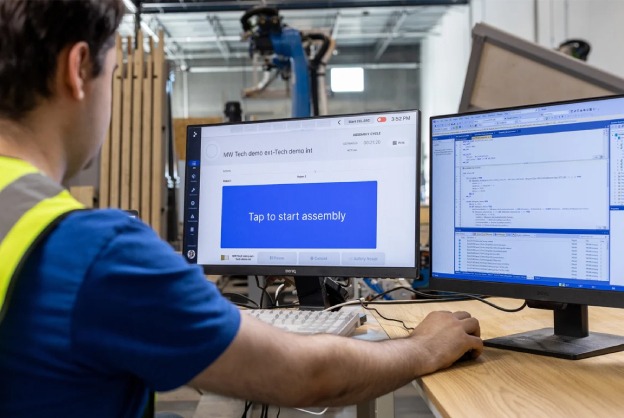
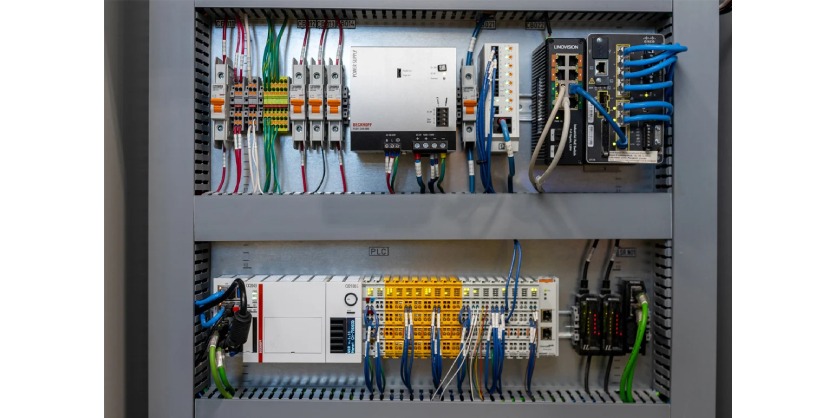
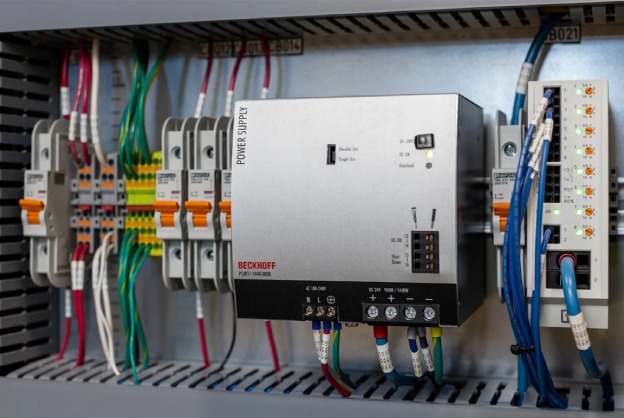
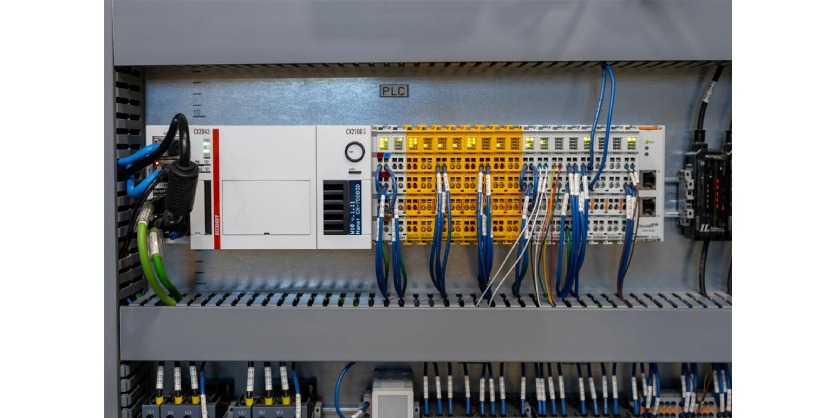
Precise control of the robotic arms and actuators is achieved using Beckhoff’s AMI8122 servo drives, which combine the servomotor, output stage, and fieldbus connection in a space-saving design. Promise Robotics leveraged the compact AMI8122 servo drive to build a custom end effector paired with a KUKA robot to achieve the precision alignment required to build different structures, shapes and sizes.
The AMI8122 is part of Beckhoff’s distributed drive solutions, which bring drive technology out of the control cabinet and place it directly on the machine. This design significantly reduces the control cabinet size, overall machine footprint, and cable length, making it ideal for dynamic construction environments.
The servo drive high-speed EtherCAT communication protocol and TwinCAT 3 Drive Manager 2 also simplify implementation and commissioning, enabling Promise Robotics to maintain reliable, precise control over their automated systems in real-world construction scenarios.
Because safety is paramount, Beckhoff’s EL6900 TwinSAFE safety controller ensures the safe operation of all machines. This system-integrated I/O component handles safety-oriented applications based on Boolean values, with function blocks for processing safe input signals and generating safe output signals. Additionally, it supports up to 128 safe connections and includes a backup and restore function for easy controller exchange, contributing to the reliability and safety of Promise Robotics’ automated systems.
Creating a blueprint for the future
By standardizing their control system on automation solutions from Beckhoff products and relying on a flexible and open fieldbus, Promise Robotics has significantly accelerated research and development cycles and reduced commissioning times.
“Standardizing on a single fieldbus means our development teams can learn one system and become very proficient with it. It’s allowed us to keep all of our control systems harmonized and universal, decreasing our deployment times and time-to-market,” said Brix.
By adhering to open standards like EtherCAT and using a scalable control platform, Promise Robotics is building a flexible system that ensures compatibility with emerging technologies. This standardized approach simplifies maintenance, ensures consistent operation across all machines, and allows seamless integration of new innovations – reducing downtime.
Moreover, this future-proof architecture enables Promise Robotics to adapt over time, laying the foundation for expansion.
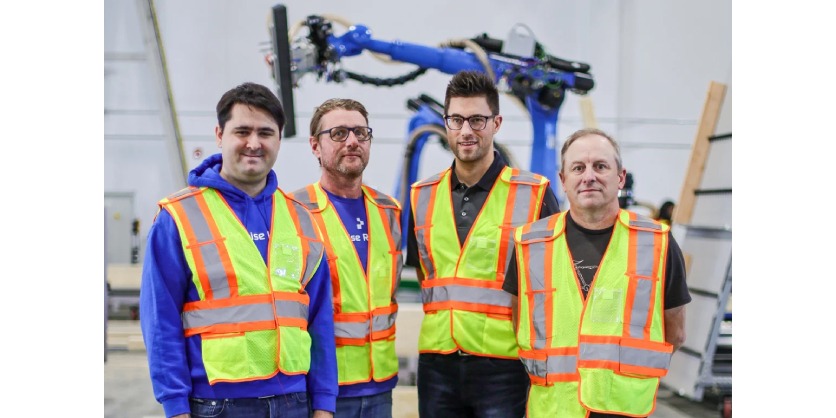
“Right now, we’re focused on wood frame construction, which is about 80% of residential construction in the U.S. and Canada. But essentially, we are building the largest AI library for construction tasks for robotic assembly that could extended to all kinds of building assemblies,” Attar said, explaining the challenges involved in attempting to transform an entire industry.
“There’s a reason why automation has not scaled in this massive, multi-trillion-dollar industry. While there have been some successful custom implementation, scalability and rapid deployment have been rather limited. Our goal is to deploy these systems very rapidly in non-custom factories, where you can take over a warehouse, turn on the lights, and start returning profit on your capital.”
While challenges remain, the company’s commitment and optimism for the future of construction has only been buoyed by initial results.
“Other industries have been successfully deploying automation and robotics in manufacturing processes over the past 50 years,” Brix said. “We’re doing the same very quickly now, in a compressed timeline. We’ve made great progress, but there’s still lots to do – and that’s the fun part.”
More Information
Related Story
Beckhoff Future-Proofs Hybrid Connectors in Industrial Cable Offering
Beckhoff’s proven hybrid connectors, part of the company’s One Cable Automation (OCA) solution, are receiving a major update to better support distributed automation well into the future. Beyond the design advantages of consistent modularization with a uniform data core, these connectors now comply with the upcoming IEC 61076-2-118 standard, enabling a seamless transition in advance of the rollout.