International Research Project Federated Learning for Robot Picking (FLAIROP) Successfully Completed
New AI methods improve picking by robots
August 3, 2023
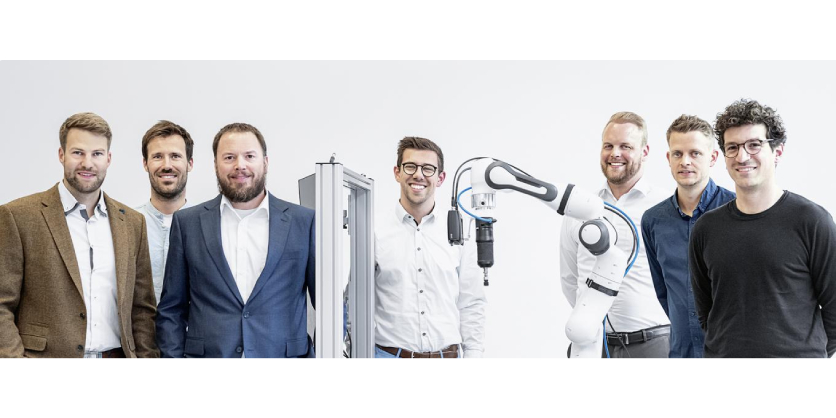
The FLAIROP (Federated Learning for Robot Picking) research project, which was sponsored by the German Federal Ministry for Economic Affairs and Climate Action, was concluded at Festo in Esslingen-Berkheim. At the event, all project participants – as well as interested public – were on site or presented their results live from Canada.
Over the past two years, Festo has been conducting joint research with the “Karlsruher Institut für Technologie” (KIT) and partners from Canada (University of Waterloo, Darwin AI) to make picking robots more intelligent using distributed AI methods. To do this, the partners investigated how robots can learn from each other without sharing their training data. This approach – called Federated Learning – allows to develop more robust and efficient AI than it would be possible with data from just one robot – without handing out sensitive company data.
“We are proud that we have succeeded in showing that robots can learn from each other without sharing sensitive data and company secrets. This protects our customers’ data and we also gain speed because the robots can take over many tasks faster this way. For example, the collaborative robots can help production workers with repetitive, heavy and tiring tasks,” says Jan Seyler, Head of Advanced Development Analytics and Control.
Jan Seyler, Head of Advanced Development Analytics and Control.
“We have developed a universal, simulation-based data set that we can use to train autonomous gripping robots in such a way that they are able to reliably grasp items that they have not seen before,” explains Maximilian Gilles from KIT. In the future, the Federated-Learning System will be further developed so that the platform enables different companies to train robot systems together without having to share data among themselves. This can increase the acceptance of such systems in practice.
Maximilian Gilles from KIT
Federated Learning revolutionizes picking through robotics
Federated Learning is a machine learning technique to create privacy-preserving AI applications. Instead of sending the training data of the robotic arms in the picking cells to a central server to train the model there, with Federated Learning, the training takes place at many different locations. The locally trained models are then sent to the central machine learning server so that the sensitive training data does not leave the data provider. Nevertheless, Federated Learning enables learning across data silos by aggregating the distributed models and ultimately enabling highly accurate and data-driven prediction of object recognition and grasping point detection.
The robot arms in the picking cells are equipped with cameras to visually detect the items in front of them. Based on the camera image, the robot arms automatically recognize the different items and select a suitable gripping method. Due to the variety of items in a warehouse, this is a complicated task and large amounts of data are needed to achieve reasonable results. Creating such large amounts of data is time consuming. With data collected from picking cells in different organizations, it was possible to improve the grasping point detection of the cells.
During the project, a total of five autonomous picking stations were set up for training the robots: Two at the KIT Institute for Materials Handling and Logistics Systems (IFL) and three at Festo SE & Co. KG based in Esslingen am Neckar.
Project completion: Now it’s time for practice
At the final event, Festo focused on the usability of the results. Jan Seyler: “We are showing which Festo products it can be incorporated into.” The research results will now be published and can be freely used by all interested parties in initial pilot projects.”
More Information
Related Product
Blind Bin Picking with GripperAI
The software GripperAI from Festo enables “blind bin picking” and thus autonomous handling solutions with almost any robot, cobot or Cartesian gantry. The company ibk Ingenieur Consult GmbH is offering an online configurable robot cell as an entry-level model. This could become the patent solution for many gripping tasks, including customised designs and integration services.
Which user of robot, cobot or Cartesian gantries doesn’t dream of being able to recognise and grip unfamiliar objects or objects that have not been taught in, including automatic gripper changes. The GripperAI from Festo might just make this dream come true in the not too distant future. With conventional solutions, you either have to teach in using CAD or manually teach in the robot’s movements.uding customised designs and integration services.