New Nitrogen Purging Technology in Semiconductor Fabrication Can Accrue Millions in Energy Savings
December 3, 2024
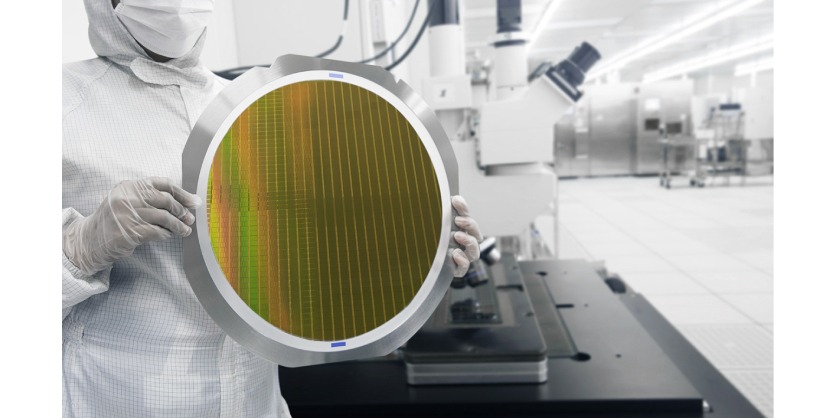
CO2 emissions associated with electricity generation will also decrease and reduce the Fab’s carbon footprint.
Research conducted by Festo finds a new generation of its low-energy flow-control valves utilized by Front Opening Unified Pods (FOUPs) purge systems can reduce Nitrogen gas (N2) consumption by as much as 75%. A new Festo white paper details how these piezo-based flow-control systems help semiconductor fabrication plants (Fabs) reduce their carbon footprint and lower energy costs.
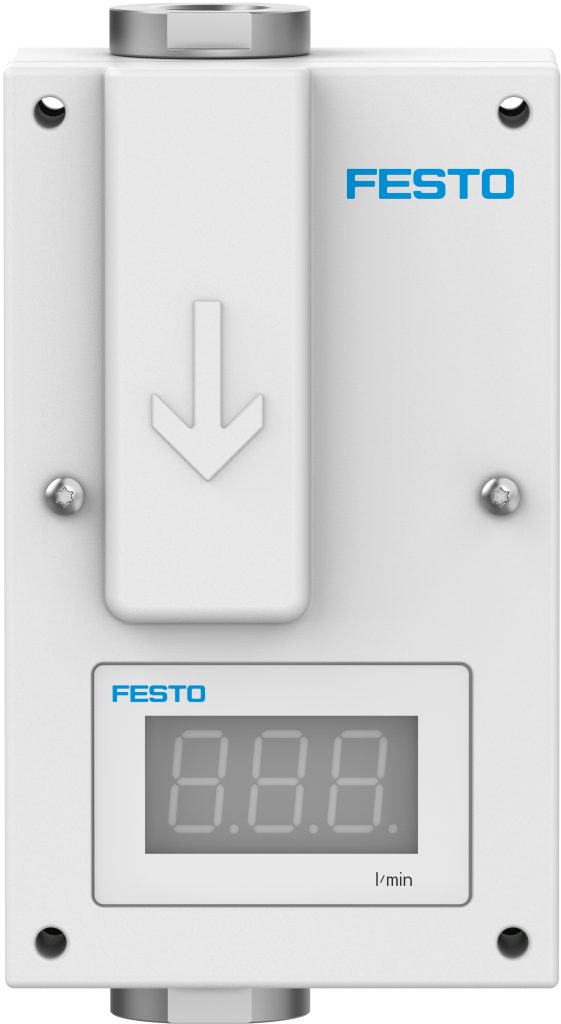
This Festo VEAD proportional flow-control valve maintains a consistent, low-particle N2 supply.
FOUPs are used to securely transport semiconductor wafers in an oxygen and particle free environment from one manufacturing step to the next. Festo estimates that for every 1,000 FOUPs utilizing precision N2 flow-control systems, Fabs can save $163,000 (U.S. dollars) per year in air-separation unit (ASU) electricity costs through reduced N2 demand. This figure is based on a $0.06 kWh utility rate. Considering that the largest Fabs manufacturing 300 mm wafers can have upwards of 20,000 FOUPs active in daily production and that Fab electricity rates can go higher than $0.06 per kWh, the $163,000 can quickly multiply into millions of savings.
For every 1,000 FOUPs equipped with new generation purge systems, Festo calculates a reduction in the environment of 1,045 metric tons of carbon dioxide (CO2) emissions directly from electricity generation. Putting this reduction into perspective, 1,045 tons of CO2 emitted into the atmosphere is the equivalent of burning 1.2 million pounds of coal according to the U.S. Environmental Protection Agency’s greenhouse gas equivalencies calculator.
The Festo piezo-based controlled-flow system reduces N2 flow from 20 nl/min to 5 nl/min per FOUP. The Festo N2 purge system significantly lowers the risk of oxidation and particle contamination. Festo N2 purge systems have a peak particle size per switching cycle of 0.1 μm, which is about five times smaller than current FOUP N2 purge systems. Closed-loop control ensures an accurate, reliable, stable, and linear flow rate – without hysteresis. The system’s repetition accuracy is rated at +/-0.25% of setpoint.
Low-friction piezo technology prolongs controller service life and minimizes maintenance. This solution requires less than one watt and reduces energy consumption by about 80% compared to competitive PWM proportional flow regulators. Festo N2 purge flow controllers consist of a two-way proportional valve, integrated flow sensor, and integrated electronics that include:
- A power supply
- High voltage technology for the piezo bender
- Piezo proportional control valve
- Stable, precise control loop for the sensor.
More Information
For more information about mass flow solutions, visit the automation in the semiconductor industry page, where the reduced carbon footprint white paper can be downloaded. To learn more about the Festo ecosystem ‒ the ecosystem that leads to less engineering overhead, fast time to market, and seamless connectivity ‒ visit www.festo.com/.