Linear Transport System Eliminates Slow Pick-and-Place Process
Battery cell production with XTS and PC-based control
May 25, 2023
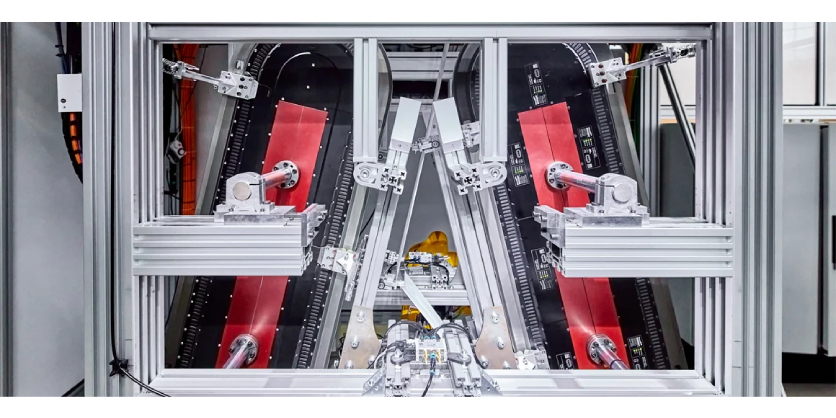
Low-cost lithium-ion battery cells (LIB) are the key to mass electromobility, although the manufacturing process has always been a cost driver – until now. Researchers at TU Berlin are using continuous Z-folding to replace the traditional pick-and-place movements that have been used so far, thus accelerating battery cell production. The XTS linear transport system from Beckhoff has played a crucial role here.
The biggest challenge in the production of lithium-ion battery (LIB) cells is that the assembly of the electrode-separator composite, which consists of many layers, is very slow. Many pick-and-place operations performed by robots or special kinematics are required for the Z-folded structures destined for electric vehicles. The process is time-consuming, as each electrode requires a pick-and-place operation, and a single 50 Ah LIB has up to 53 individual electrodes in 300 x 125 mm format.
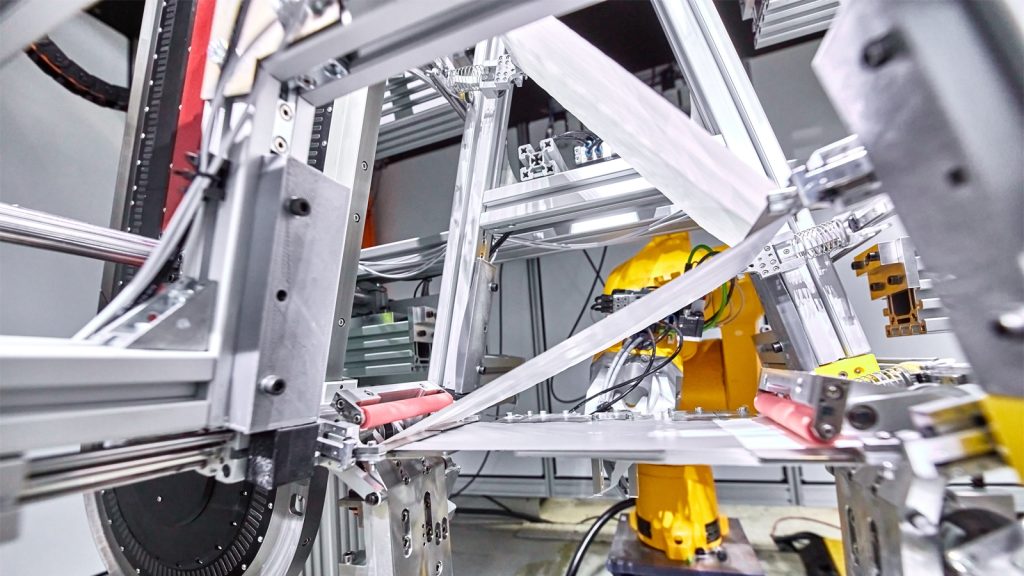
“The problem and the productivity bottleneck are evidently caused by these many pick-and-place movements,” explains Dr.-Ing. Arne Glodde, senior researcher at the Institute of Machine Tools and Factory Management (IWF), Department of Handling and Assembly Technology at the Technische Universität Berlin.
He says that handling and joining times cannot simply be reduced by faster braking and acceleration in the industrial robots. “That would impair positioning accuracy when placing the electrodes,” states Dr. Arne Glodde. This would result in a lower degree of coverage in the cell array, at the expense of cell capacity, service life, and even short circuits. “The previous process flow has reached its productivity limit in practical terms,” points out Dr. Arne Glodde, in reference to what was ultimately the impulse that led to the development of the new LIB production process.
Dr.-Ing. Arne Glodde, senior researcher at the Institute of Machine Tools and Factory Management (IWF)
Battery stacking accelerated by 150%
The researchers at TU Berlin have replaced the pick-and-place process with continuous material transport of the electrodes and separator. “This has enabled us to increase production by more than 150% compared to the current state-of-the-art process,” says Dr. Arne Glodde, outlining the most significant improvement. This increase in throughput means that, in the future, 250 cells will be able to be produced in the time that it currently takes to produce 100. The key innovation in this process is the patented Z-folding technique based on the XTS linear transport system and its rotating grippers. Two of these systems with a total of ten movers ensure continuous folding with precise positioning of the electrodes in the stack.
The electrodes are available as stacks of individual sheets, and the separator is available as belt material. Using a vacuum-based process, the flexible electrodes are each picked up by an individual roller and accelerated to the speed of the separator belt. During transportation, positions are detected and the electrode sheets are precisely aligned with the separator. The electrodes are then fixed alternately on the separator material as it is continuously conveyed.
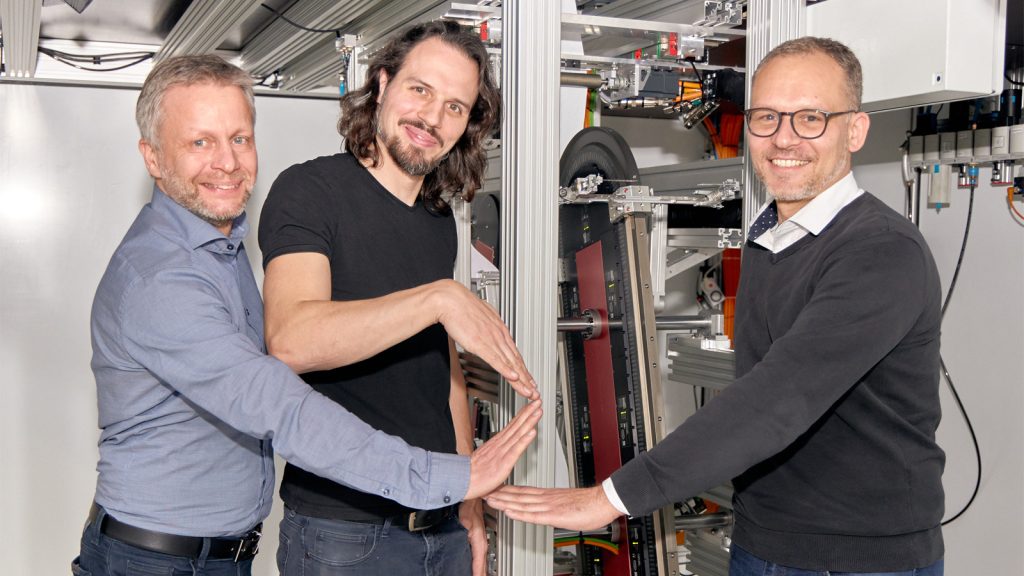
This is followed by Z-folding, whereby the separator belt with the electrodes fixed to it is fed into the folding process from above via two guide rollers. Two commuter rollers deflect the belt material for this purpose and to facilitate alternating gripping from the rear with special grippers. These are mounted on the movers of the two interlocked XTS systems, and guide the folds until the belt material is deposited on the folding table. where a hold-down system secures the folds. The XTS systems are mounted in a vibration-free structure that can be integrated into the individual sequence of any battery production system.
XTS opens up potential for innovation
“Without the linear transport system from Beckhoff, we would not have been able to implement continuous Z-folding with this process control properly and achieve these significantly shorter processing times,” says Dr. Arne Glodde. The processing time has been cut from over one second per fold to 0.7 s for large-format z-folded electrode-separator composites, and the process is still far from reaching the limits of its potential. In the future, times of around 0.35 s per fold could be achieved.
To create a fold in 0.7 s, the movers travel at a speed of about 600 mm/s. For the targeted 0.35 s per fold, this speed would be around 1,000 mm/s. “Our XTS is designed to travel at up to 4 m/s as standard, so it has enough capacity to accelerate the process further,” states Guido Sieder, sales engineer at the Beckhoff Berlin branch.
“The mechanical properties of the separator material and the moments of inertia will probably always be the limiting factors in the long run,” confirms Dr. Arne Glodde.
Dr.-Ing. Arne Glodde, senior researcher at the Institute of Machine Tools and Factory Management (IWF)
The special features of XTS and PC-based control are responsible for the current leap in performance. Dr. Arne Glodde comments: “With its freely controllable movers, XTS brings our demanding motion sequence to life.” The grippers have to be moved in relation to each other in order to fold the material with adequate belt tension while coping with the stresses. While this may sound simple, it actually requires high-performance yet flexible automation technology:
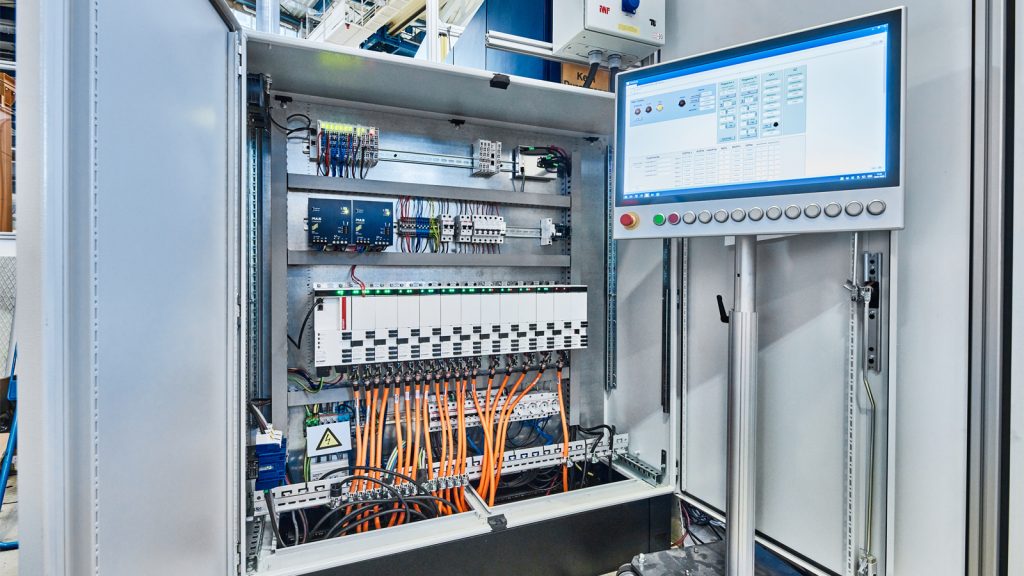
- TwinCAT has to calculate the position of a mover in relation to the position of the other movers precisely and in real time.
- Accurately synchronizing the rollers over the shortest distance requires high dynamics.
- The number of actively intervening movers must be able to be adjusted dynamically during the process.
- To ensure that the positions along the separator belt are approached at the right time, a high degree of repeatability is needed.
- Load fluctuations require high-quality control.
“To calculate and control all of the kinematics in real time, we had to ensure that the XTS servo axes can seamlessly switch from NC (point-to-point) operation to interpolation,” explains Mathias Arndt, application engineer at the Beckhoff branch office in Berlin. Dr. Arne Glodde, who is responsible for the project, says that the module-specific programming and synchronization of the controllers, thanks to TwinCAT’s multitasking capabilities, was also very helpful during implementation.
Path planning for all axes is performed directly in the controller based on the kinematic calculation that has been performed. The sequences in the other modules are coupled via virtual axes and corrected via superpositioning movements in relation to the other elements in the process. Another plus point for Dr. Arne Glodde is the simple integration and synchronization of the six-axis robot kinematics that eject the folded electrode packages.
Position detection of objects that is as fast and accurate as possible is crucial for precision and repeatability. The Berlin researchers relied on XFC technology to provide this. “We use eXtreme Fast Control Technology’s timestamping feature for calculating the positions,” specifies Dr. Arne Glodde, “and signal acquisition thus becomes independent of the PLC cycle.” The advantage is that control technology is no longer the limiting factor in position detection; instead, the current sensor technology with sampling rates of 62.5 kHz constitutes the limit here.
Further acceleration through actively controlled grippers
It goes without saying that Dr. Arne Glodde and his team are working on pushing the boundaries of Z-folding further still. “We do actually see lower accuracy at higher speeds due to vibration and inertial forces. This could be counteracted with even stiffer guide rails or active grippers.” Beckhoff has solutions for both: the XTS linear transport system with its V-shaped guide system and No Cable Technology (NCT) for wireless transmission of communication and power to the movers broadens the scope for further optimization, making the folding processes faster and more flexible.
“More specifically, we are working on the further development of our grippers and want to use NCT to replace the mechanical positive guidance with active control of the grippers,” says Dr. Arne Glodde. This increases the flexibility of the system with regard to electrode formats and enables errors in the feed to be compensated dynamically. “Furthermore, we also want to integrate a vision system into the system for quality assurance,” states Dr. Arne Glodde, outlining the upcoming expansion plans.
Dr.-Ing. Arne Glodde, senior researcher at the Institute of Machine Tools and Factory Management (IWF)
More Information
- XTS | Linear product transport
- Technische Universität Berlin
- Automation solutions for battery manufacturing
Related Product
Beckhoff’s TF3820 | TwinCAT 3 Machine Learning Server
Beckhoff offers a solution for machine learning (ML) and deep learning (DL) that is seamlessly integrated in TwinCAT 3. The TF3820 TwinCAT 3 Machine Learning Server is a high-performance execution module (inference engine) for trained ML and DL models.
The inference engine is programmed classically in the PLC. From here, models can be loaded, the running hardware can be configured, and the inference executed. The model runs in an independent process of the operating system. There are almost no restrictions when it comes to the ML and DL models. From clustering models to image classification and object detection, the possibilities in the choice of models are extremely diverse.