KMP 600-S diffDrive: New Avenues for Intralogistics
February 7, 2023
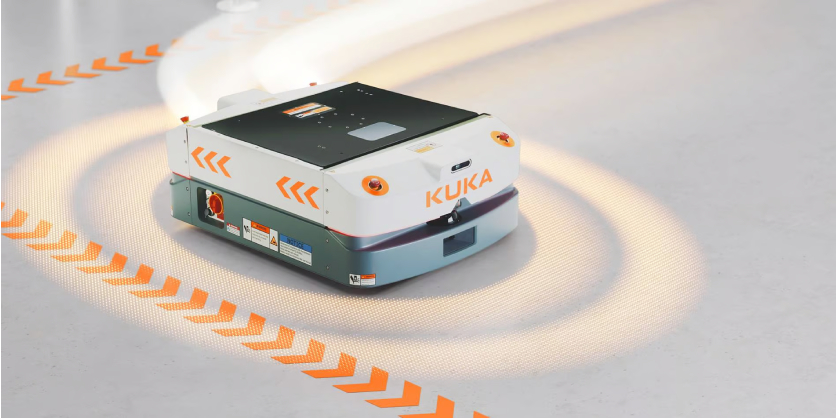
A compact powerhouse meets the highest safety requirements: The new generation of the KMP 600-S diffDrive expands KUKA’s portfolio of mobile platforms. The KMP 600-S diffDrive is fast – up to two meters per second – and equally safe, thanks to laser scanners and 3D object detection.
This collision-free coworker takes intralogistics to a new level – especially in the consumer goods industry
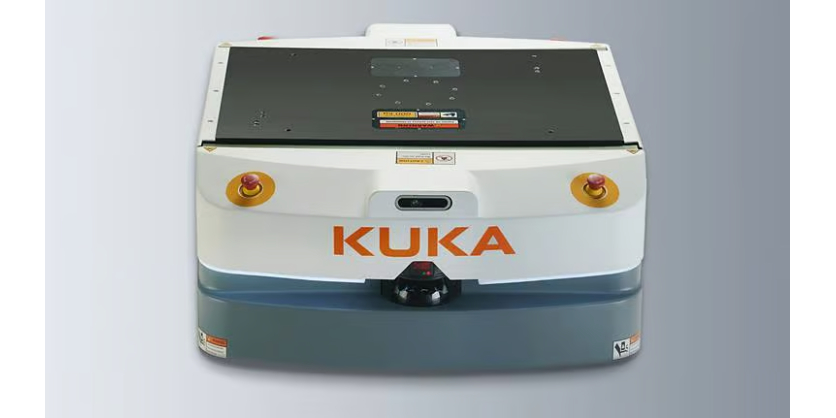
Mobile solutions must meet extremely high standards for industrial use. The KUKA KMP 600-S diffDrive mobile platform provides a new automated guided vehicle system with high-speed support for production intralogistics and a payload of up to 600 kg. At the same time, the KMP 600-S diffDrive is ideally equipped for the tough everyday environment of industrial production. Its IP 54 design always enables it to work reliably even under adverse conditions – including water spray and dust.
A compact powerhouse that meets the highest safety requirements: the new generation of the KMP 600-S diffDrive expands KUKA’s portfolio of mobile platforms. At up to two meters per second, the KMP 600-S diffDrive is not only fast, but also safe thanks to laser scanners and 3D object detection. The collision-free coworker thus takes intralogistics to a new level – especially in the consumer goods industry.
Maximum safety, maximum flexibility
All KUKA mobile platforms guarantee employees maximum freedom of movement without the need for safety fencing. The KMP 600-S diffDrive is no exception. Laser scanners mounted at the front and rear of the machine provide maximum safety and allow for high speeds in all directions of travel when cycle times require it. “Safety is a central concern for us,” said Jakob Brandl, portfolio manager at KUKA. “That’s why the KMP 600-S diffDrive uses eight safety zones at both the front and rear – customizable for vehicle speeds and specific applications.”
Interfaces for any requirement
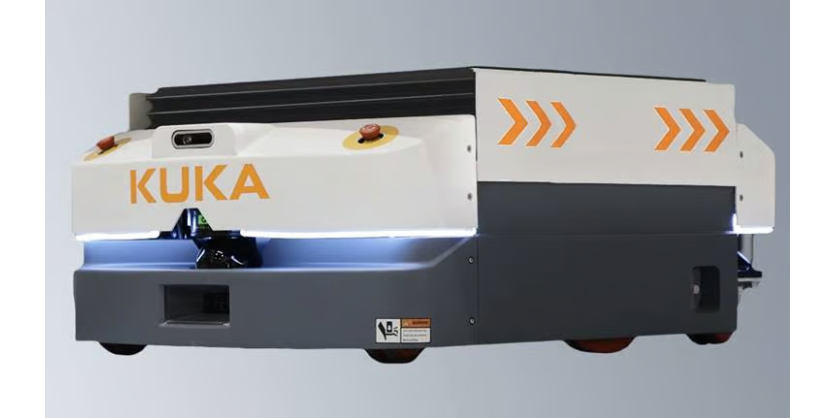
Add 3D object detection to expand the KMP 600-S diffDrive so it can detect obstacles from 50 mm to 2.10 m above the ground. Link the KMP 600-S diffDrive to a wide variety of workstations for precisely the right load-handling options. For example, it acts as a top-load AGV (automated guided vehicle) and can lift pallets or cartons up to 60 mm via its integrated lifting device.
KUKA.NavigationSolution for navigation and fleet management
Start up the KMP 600-S diffDrive via a manual controller and program applications in Java. With an operating time of around eight hours, the KMP 600-S diffDrive can recharge in two hours. KUKA.NavigationSolution monitors an entire fleet: it detects battery charge levels and identifies which vehicles are connected to the WLAN. After initial environment teaching through the SLAM algorithm, the software solution takes over localization in space (on the vehicle itself) as well as vehicle coordination (on a central computer). The fleet manager uses parameters such as distance and speed to determine the best route on the network of paths – avoiding all collisions.
More Information
Related Story
KUKA Showcases Automation for Human/Machine Collaboration at ATX West
During the ATX West show, KUKA Robotics showcased several new technologies geared specifically for safely automating those manufacturing processes where humans interact with robots on a regular basis. Among those technologies were the new LBR iisy cobot, the new KUKA KMP 600-S diffDrive automated mobile platform and the company’s LBR iiwa robot incorporated into an automated mobile robotic material-handling system.