Grippers Of the Future
Intelligent Handling Solution Supports Kaco in Production
July 19, 2023
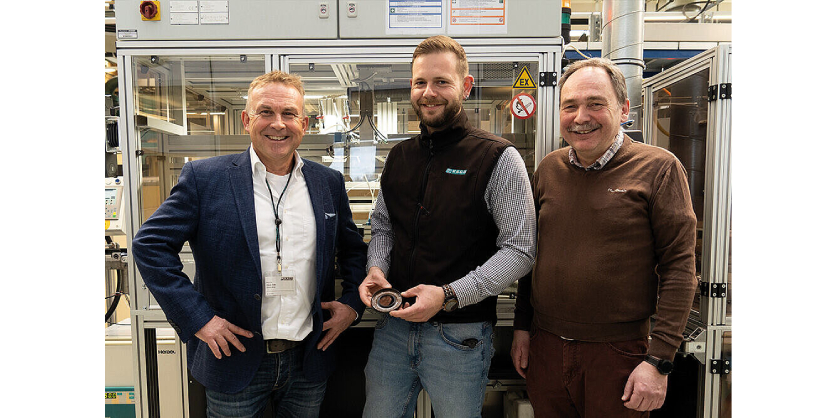
When it comes to the production of radial shaft seal rings, an intelligent gripper solution is essential. KACO GmbH + Co KG relies on a gripper of the future from the Zimmer Group, which makes production more efficient and faster.
Handling of radial shaft sealing rings
KACO is the world’s leading developer and manufacturer of high-precision, application-oriented sealing solutions for the automotive and supplier industry. As a close partner to the automotive and supplier industry, the company is in tune with the times and also relies on forward-looking technologies in its own production.
For the innovation of their production plant, a gripper solution was needed to ensure the placement of radial shaft seal rings in the sliding wax plant. The sliding wax line is the last step before the seal rings are visually inspected before they are shipped packaged to the customer. The lubricant ensures the smooth installation of the products at KACO’s customer’s site.
To choose the right gripper, the company turned to automation specialist Zimmer Group, as it already had a long and successful working relationship. The requirements for the gripper were clearly defined: It must be able to handle radial shaft seals with different dimensions and enable parameterisable stroke settings. Pneumatic grippers that always open completely were not practical. In addition, only an internal gripper was possible, as the rubber coating of the workpieces must not be damaged.
KACO relies on IO-Link technology
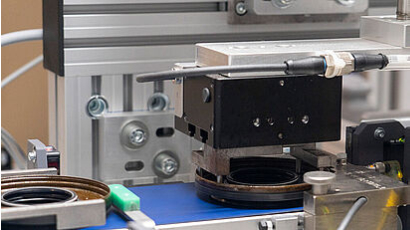
The GEH6040IL-03-B electric gripper turned out to be the ideal solution for these requirements. Its IO-Link technology enables precise force adjustment and individual control of position and speed thanks to the servo drive. In addition, the gripper convinces with its easy commissioning and control as well as the adaptation to different workpieces.
Up to 32 settings can be stored in the gripper, which facilitates adaptation to new workpiece sizes and thus saves valuable time during production changeover.
“The mechanical self-locking when the position is reached is also a big plus. It ensures that the workpiece is held securely in the event of an emergency stop or power failure,” knows Klaus Tritt, technical consultant at the Zimmer Group, who supported KACO in this project.
In KACO’s glide wax system, two 6000 series grippers were connected in series to ensure the transport of workpieces from the conveyor to the glide wax system as well as from the system to the conveyor for transfer to the visual inspection.
The use of intelligent grippers in production
The integration of the gripper into KACO’s production line went smoothly. The close cooperation between the Zimmer Group and KACO made it possible to develop a customised solution that was perfectly tailored to the needs of the automotive supplier.
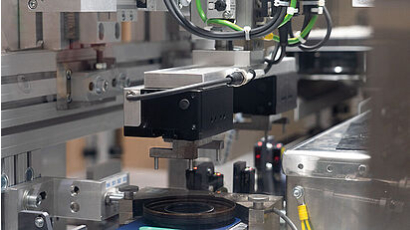
“The service and above all the technical advice from Klaus Tritt were always excellent. No matter what challenge arose during the integration of the grippers, Mr Tritt was immediately at our side and was able to find a solution with us,” says Hubert Eckert, CAD designer and production optimiser at KACO.
Overall, the use of the intelligent gripper has proven to be extremely successful. The application of sliding wax to the radial shaft seal rings now runs faster and more efficiently, which is also reflected in the production costs: these have been reduced by half, mainly due to the saving of valuable time during set-up on new workpieces.
Long partnership characterises cooperation
KACO is proud of the successful in-house developments and the value-added chain from a single source, which make it possible to respond to customers’ individual wishes – a philosophy that is also shared by the Zimmer Group. Together, they look positively at the developments in the automotive industry. With their technical know-how and solutions expertise, they agree that both KACO and the Zimmer Group will play a decisive role in shaping the transition from combustion engines to e-mobility.
For years, the Zimmer Group has been a leading development and system partner for renowned automobile manufacturers as well as their suppliers and system integrators. The company’s portfolio covers the handling of all powertrain parts, including camshafts, crankshafts, cylinder blocks and heads, transmissions and chassis parts as well as tyres, wheels and rims. Due to the demands that electric vehicles place on production technology, the economical production of battery cells and packs is crucial for the growth of this market. A high degree of automation, for example in battery production, module assembly and electric motor production, is indispensable for this.
More Information
Related Product
MATCH. End-of-Arm-Ecosystem
The MATCH series offers a unique potential for standardization: The MATCH robot module can be mounted on the most common types of robots and acts as a connection for the entire range of end effectors compatible with MATCH. The standardized robot connection flanges offer a high degree of flexibility in the choice of applications. The attached end effectors, regardless of whether they are grippers or suction cups, can be easily exchanged manually or automatically using the click system. Standardized and ready-to-connect solutions guarantee maximum system availability.