Gripper for Small Components EGI with Active Gripping Force Maintenance
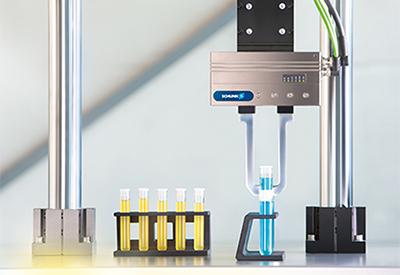
August 19, 2021
Gripper for small components EGI
The EGI was specifically designed for challenging and diverse handling tasks in electronics, pharmaceutical and laboratory applications. Individually programmable stroke of up to 57.5 mm per jaw. Flexibly adjustable gripping force of up to 100 N. Components that are sensitive to deformation or fracture can be handled reliably and gently. Due to the integrated web server, convenient commissioning assistants, active gripping force maintenance, and the certified category C PROFINET interface, the 24 V gripper for small components is one of the most convenient mechatronic grippers on the market.
Laboratory automation
Sensitivity and flexibility are important in laboratory applications when handling test tubes, petri dishes, syringes, and other fragile laboratory equipment. With its flexibly adjustable gripping force, the EGI can safely grip them without damaging them. Due to the individually programmable stroke, parts with different diameters can be flexibly handled during a change. The closed jaw guidance is a significant advantage when it comes to avoiding impurities.
Benefits of the EGI in laboratory automation:
- Gripping of different sample containers and holders with the flexible stroke of 57.5 mm per jaw.
- Safe and sensitive equipping of centrifuges with glass or plastic containers
- Safe holding of sample containers due to the gripping force maintenance
- Smart, simple commisioning due to the integrated and intuitively used web server
Medical and pharmaceutical automation
The EGI provides maximum flexibility and safety
Automated processes in the medical and pharmaceutical industries have high demands on gripper components. Syringes, cannulas, and other small plastic and glass parts must be gripped without deformation. With its flexibly adjustable gripping force, the EGI sets benchmarks in terms of sensitivity and safety. Due to its individually programmable stroke up to 57.5 mm per jaw, it covers a wide range of parts diameters.
Advantages of the EGI in medical and pharmaceutical automation:
- Maximum flexibility e.g. when packing different medical plastic and glass parts
- Short cycle times with pre-positionable gripper fingers
- Smart, simple commisioning due to the integrated and intuitvely used web server
- Sensitive gripping of cannulas, syringes and ampules without deformation
- Highly flexible gripping of work pieces with different diameters
Electronics industry
The EGI with sensitivity and a long stroke
In the electronics industry, the EGI scores with its long stroke of up to 57.5 mm per jaw and a sensitive adjustment of the gripping force. These strengths fully come in the SCHUNK depaneling systems into play, where a wide variety of panels are to be separated. Printed circuit boards with different formats or entire panels can be flexibly and sensitively gripped so that they cannot be damaged or destroyed.
Advantages of the EGI in the electronics industry:
- Sensitive gripping of even very small, thin parts with a stroke of up to 57.5 mm per jaw
- Smart, integrated web server for convienient commisioning
- Flexible, quick prepositioning of the gripper fingers for variable, highly dynamic panel handling
- Efficiency enhancement in the process sequence
Production automation
The EGI – the all-rounder for many applications
The robust design of the EGI is perfectly suitable for industrial applications. Its variable stroke and gripping force offers the possibility for handling different sized workpieces that also vary in shape and position. Irregularly oriented workpieces can be gripped at different gripping points. The EGI is an all-rounder and is suitable for applications with a high workpiece variance e.g. for bin picking.
Benefits of the EGI for production automation:
- Robust design, electric connection with plug connectors in accordance with industry standard
- Maximum flexibility at a high workpiece variance
- Versatile gripping with a stroke of up to 57.5 mm per jaw
- Integrated web server for convient commissioning
- Category C PROFINET interface for continuous data exchange
- Intermediate positions and special referencing of the gripper are possible
- Integrated intelligence and Ethernet interface
Smart factory
The EGI – intelligent and real-time capable
Ready-for-Industry-4.0! The EGI can be used in smart applications without restrictions. With its certified, category C PROFINET interface, the SCHUNK EGI meets all the prerequisites for high-performance applications. The position of the gripper fingers, the gripping forces, or the closing speed can be detected and controlled. Intermediate positions and special referencing for the gripper are also possible. The data e.g. of workpieces can be gathered, stored and evaluated.
Advantages of the EGI in the Smart Factory
- Smart, convenient commissioning via integrated web server
- Work and process data on the workpiece and process can simply be transferred to a cloud and processed
- Category C PROFINET interface for high-performance applications due to fast data transmission up to 100 Mbps
- Versatile gripping with a stroke of up to 57.5 mm per jaw
- Intermediate positions and special referencing of the gripper are possible
- The gripper is suitable for PROFINET IRT (isochronous real time) structures and can therefore be deployed in high-performance applications
For more information click here.