Festo Takes Pneumatics to a New Level of Performance Through Digital Closed-Loop Control
December 3, 2024
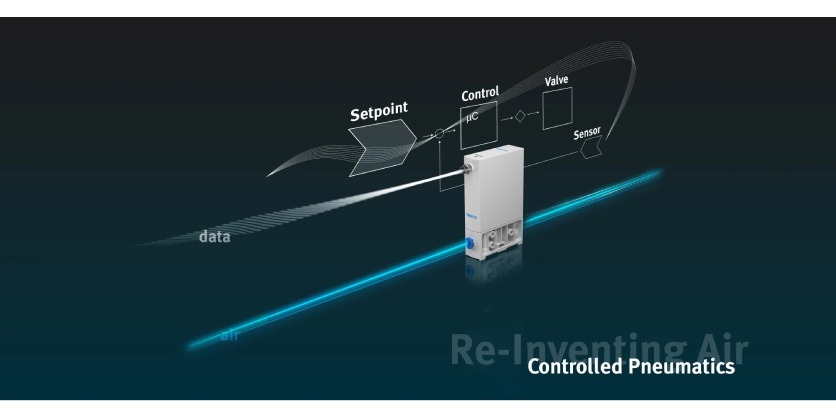
Controlled Pneumatics combines proportional technology, sensors, and control algorithms into a closed-loop control system.
Festo introduces Controlled Pneumatics, a digital closed-loop control strategy for delivering energy efficiency, high dynamic response, and precision movement. Controlled Pneumatics is an ideal solution for web tensioning; welding; surface processing; flexible gripping, including vacuum gripping; dispensing and pumping; PET bottle blowing; and diaphragm pump control.
Controlled Pneumatics lowers compressed air usage by up to 50%. The reduction in energy improves the sustainability of the operation by lowering carbon dioxide (CO2) emissions from electricity generation. Precise proportional pressure control also conserves gases used in food and beverage, chemical, and semiconductor processing applications.
Controlled Pneumatic systems are composed of digitally controlled proportional pressure regulators, sensors, high-speed communications, and control algorithms. Controlled Pneumatics proportional pressure regulators feature piezoelectric valves, a technology Festo has been applying for decades and now mass produces.
Piezoelectric valves consume 95% less energy than solenoid valves. Piezoelectric valves open proportionally for precision control of pressure and flow and are fast acting for highly dynamic applications. Closed-loop control of these valves ensures an accurate, stable, and linear flow rate – without hysteresis. Repetition accuracy is rated at +/-0.25% of setpoint. Piezoelectric valves do not generate heat and can be densely packed. Low friction prolongs service life. These valves have a peak particle size per switching cycle of 0.1 μm, which is about five times smaller than proportional pressure regulators that do not use piezoelectric valves. These valves operate silently.
The Festo Controlled Pneumatics product range includes the VPPI proportional pressure regulator for high flow rate applications. The VTEM motion terminal is used for multi-channel control of large and small workpieces. The VEAB low flow rate proportional pressure regulator is designed for highly precise applications. The VTEP is a compact valve terminal for multi-channel low flow rate pressure control. It features high precision and dynamic response. These proportional pressure regulators can be used in addition with solenoid valves for hybrid functionality. The VEAB is a proportional pressure control valve for pressure ranges up to 6 bar. The VEFC is a compact mass flow controller for inert gasses.
Festo offers control algorithms to operate the VTEM Motion terminal, including:
- Flow control
- Selectable pressure level
- Positioning over the entire stroke of the cylinder
- Preset travel time
- Operating actuators with minimum pressure
- Leakage diagnostics
- Soft stop
- Model-based proportional pressure regulation (no need for external sensors)
- Proportional pressure regulation – two pressure regulators per valve slice at the two valve outlets that can be used to regulate pressures independently of each other, including vacuum.
These algorithms can be downloaded as apps on demand for the VTEM motion terminal.
Controlled Pneumatics simplifies commissioning through immediate adjustment to specified setpoints during operation. Presets enable fast format changeovers.
“Controlled Pneumatics digitizes pneumatics,” said Stefan Stolz, Head of the Controlled Pneumatics Product Line. “The latest sensors, fast communication technologies, proportional valves, and intelligent control technology form a system. Our knowledge of the application parameters increases efficiency and performance and paves the way for adding pneumatics into our customers’ core processes.”
A silicon wafer manufacturing plant applied Controlled Pneumatics to its Nitrogen gas (N2) purge application. Controlled Pneumatics cut N2 flow rate for oxygen flushing by 75%. For every 1,000 nitrogen purge systems, the plant saved $163,000 (U.S. dollars) in lower energy costs. The reduced energy lowered CO2 emissions from energy generation by 1,045 metric tons. In other words, Controlled Pneumatics removed CO2 emissions equivalent to burning 1.2 million pounds of coal.
At a tire manufacturing plant, small pneumatic cylinders were used to apply various tread patterns, depending on the layer of rubber being applied. These cylinders had to be precisely controlled in a pressure range of 0.05 to 8 bar. Previously, a proportional valve was used for each individual pressure zone in this application. The multi-channel VTEM motion terminal reduced valve slices by 50%. For the application’s control algorithm, the plant used model-based control for proportional pressure, which did not require external sensors.
Links to video VPPI: https://www.youtube.com/watch?v=rxbKy8Z7RDg
VEAB: https://www.youtube.com/watch?v=gaJ-5WiKSyU
VTEM: https://www.youtube.com/watch?v=bpohz4uZUGU
More Information
Visit the Controlled Pneumatics webpage for more information or look under the solutions tab on the Festo website. To learn more about the Festo ecosystem ‒ the ecosystem that leads to less engineering overhead, fast time to market, and seamless connectivity ‒ visit http://www.festo.com/.
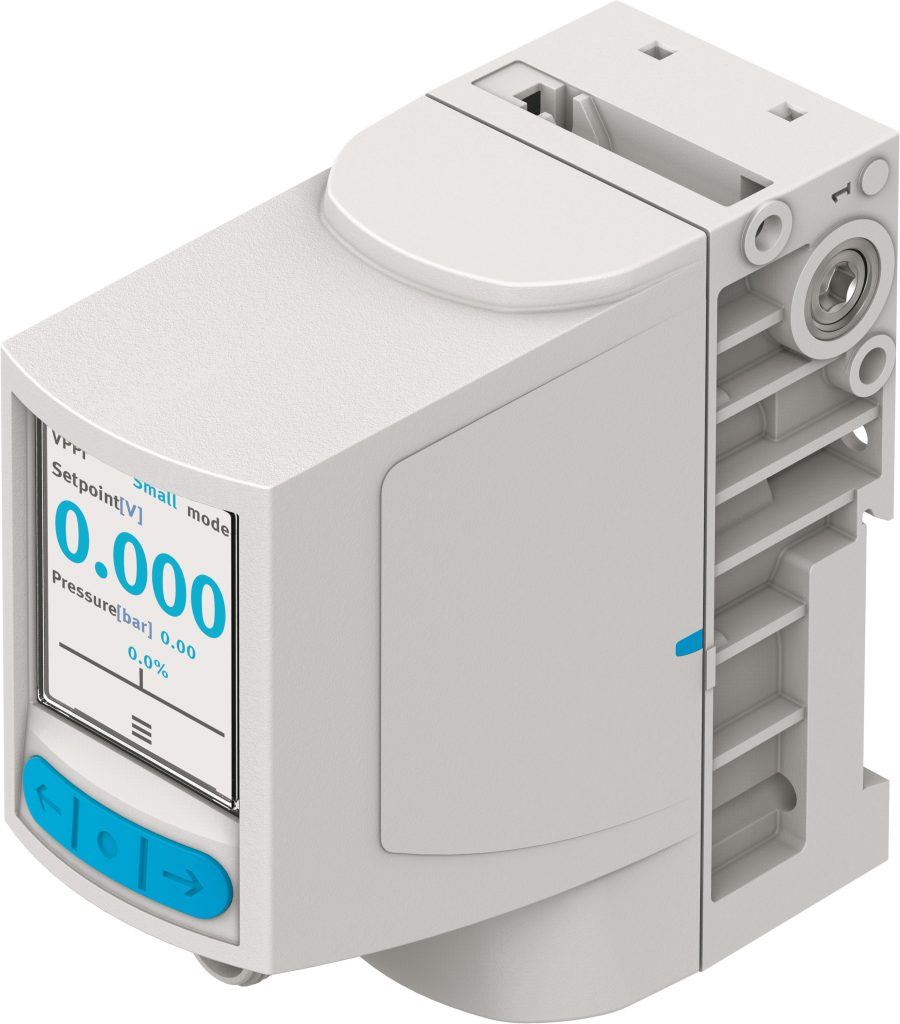
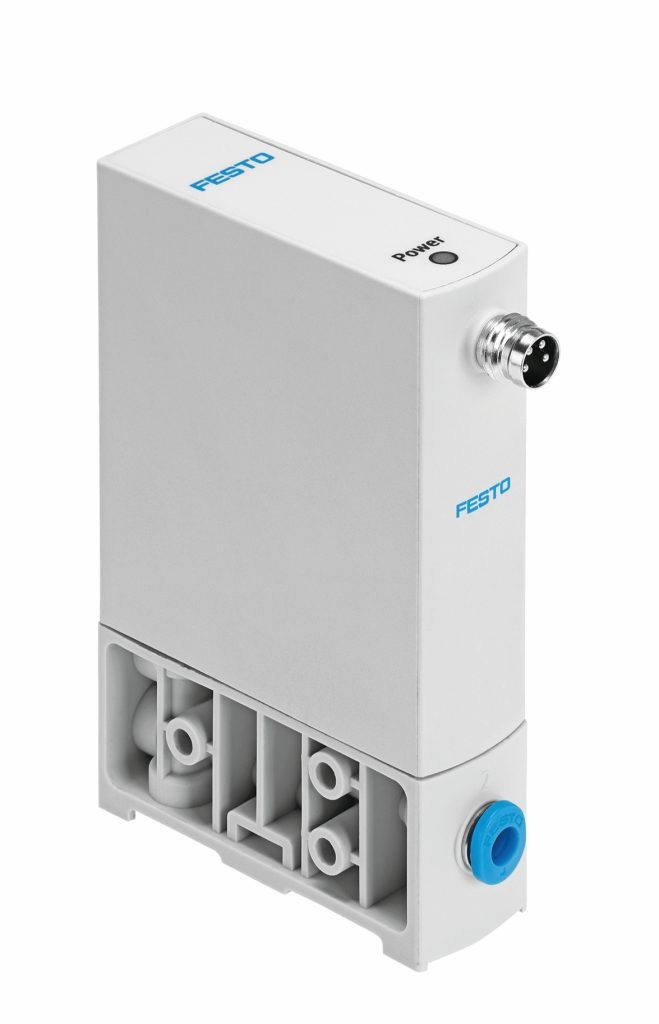
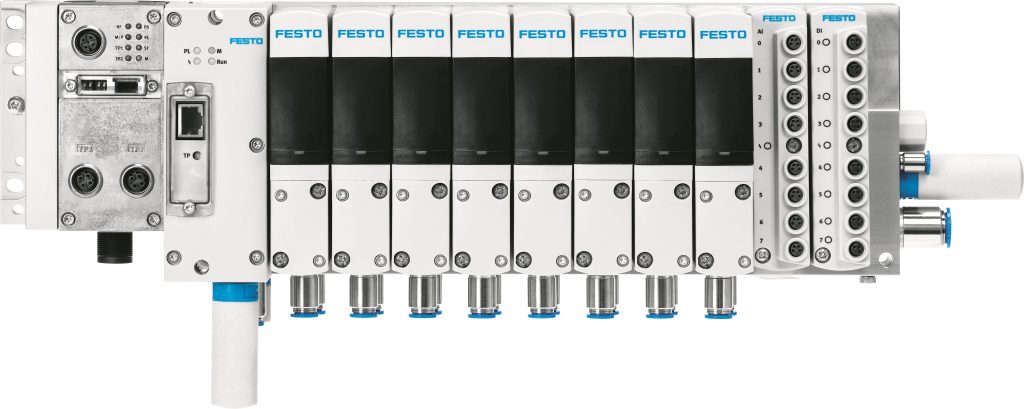
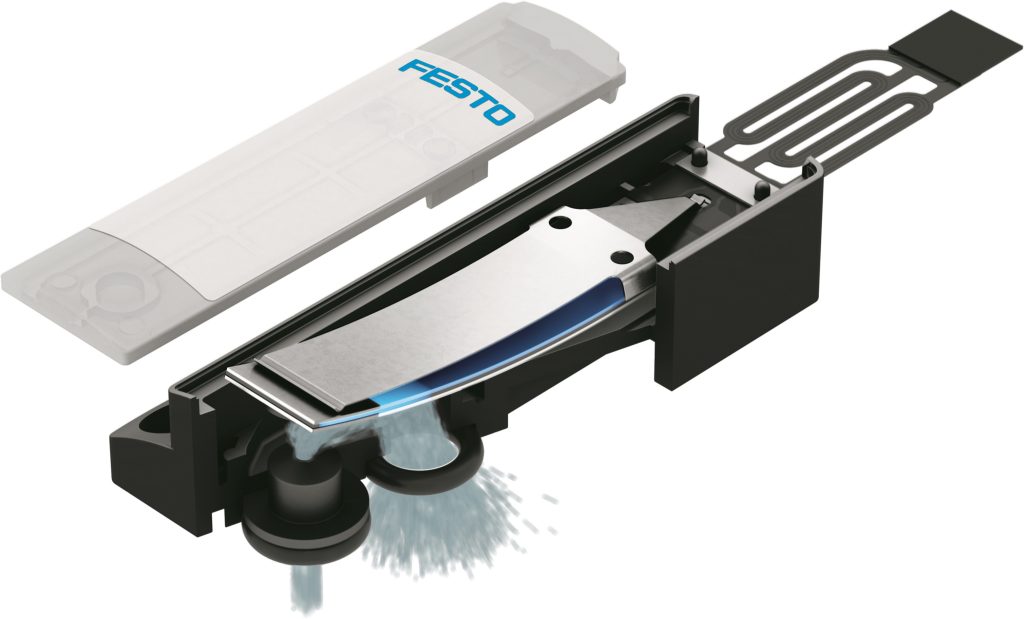
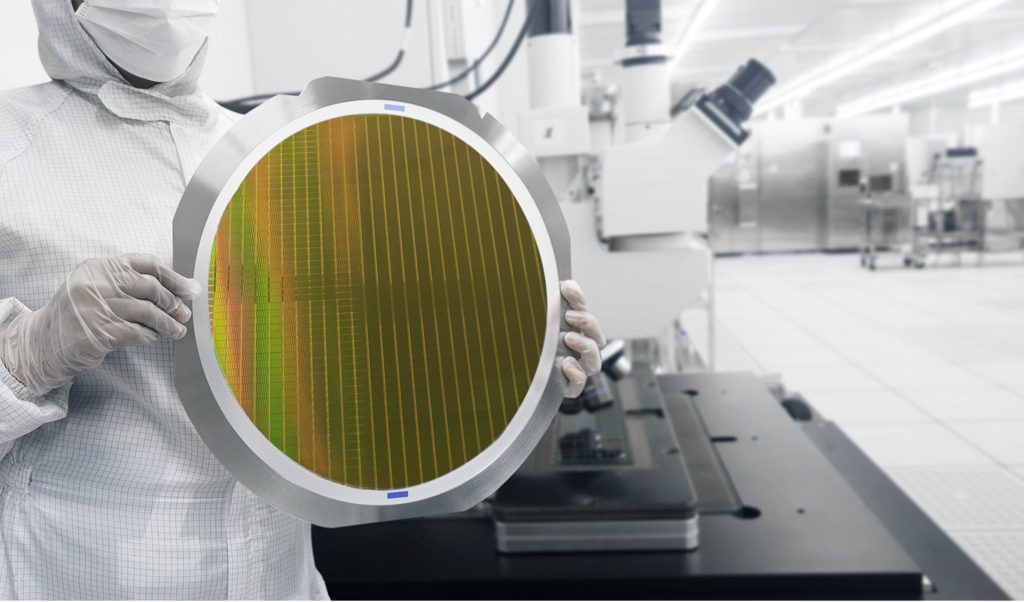
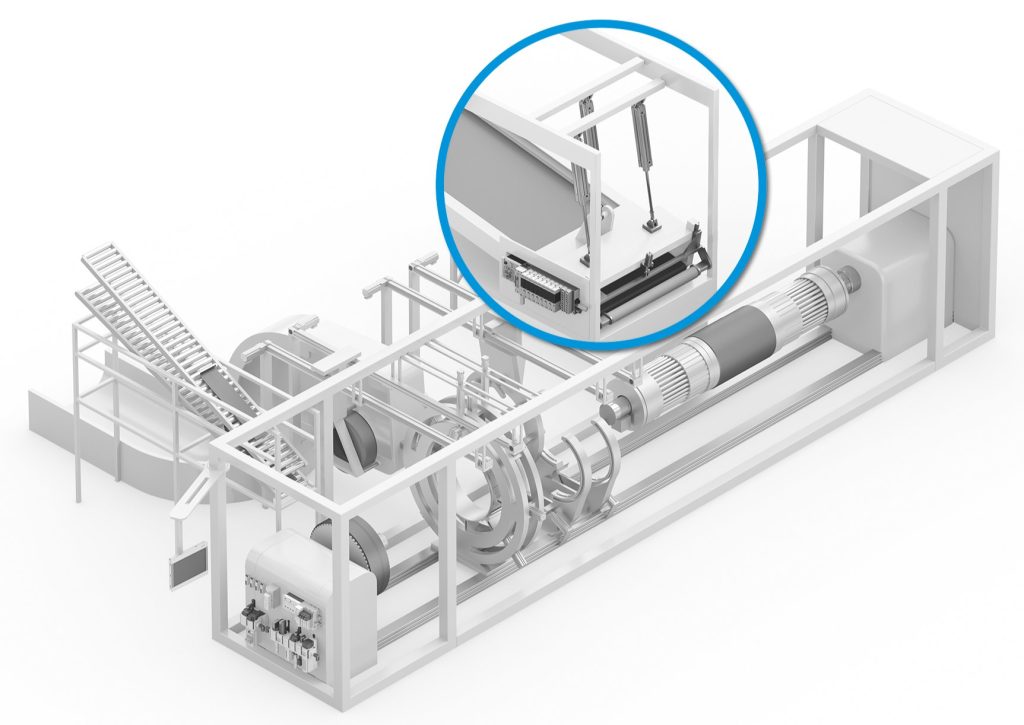