Festo’s EHMH Heavy Duty Axis Is Built for Safe Movement of Big Payloads
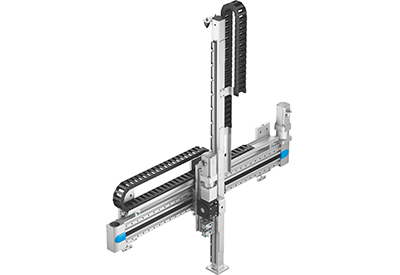
March 22, 2021
Developed with stacking or palletizing of heavy loads in mind, Festo’s new EHMH is a muscular cantilever axis with rack and pinion technology that handles payloads up to 200 kg with great repeatability. As a Z axis, EHMH can form the backbone of a complete, application-optimized handling solution with an all-Festo lineup of complementary components such as the EGC-HD heavy duty toothed belt or ball screw model as the X axis, CPX-E control system, CMMT-AS AC servo drive, EMMT-AS servo motors plus other accessories. Such a gantry-style solution is usually more cost-effective than a six-axis articulated robot performing such heavy loading/unloading functions typically required in the packaging and automotive sectors or in handling machine tools. EHMH also requires a smaller working envelope than an articulated robot, for optimal usage of available floor space.
EHMH comes in two sizes. It combines a solid steel profile and high-quality recirculating bearing guide for high rigidity and repeatability across all available stroke lengths – from 250 to 2,500 mm – with high feed force and speeds up to 1.5 m/s. EHMH also can be configured for enhanced safety protection up to Performance Level d (PL-d). A number of optional safety add-ons are available: a pneumatic locking unit for a positive, hard mechanical lock during maintenance or commissioning; a frictionally engaged clamping unit that acts as an emergency brake; and an external displacement encoder for additional position detection that can also be used as a second channel in safety applications. Among the protection options for the axis itself, users can add scrapers on both sides to guard it from external influences such as dust, dirt, particles or liquids. And the unit’s available easy lubrication features can extend the service life of the unit and reduce wear and tear.
In many cases, Festo gantries based on a cantilever axis like EHMH offer a superior cost and overall value proposition with simple commissioning for additional labor savings and a shorter project timeline than alternatives. The interpolation performed by multiple EHMH-based gantries (and their connected servo drives running in parallel) can be controlled from a single CPX-E motion controller. The CPX-E is an extremely compact alternative to the larger controllers required to manage multiple articulated robots.
For more information, visit www.festo.com.