Festo Introduces VZXA, A Uniquely Engineered Angle Seat Valve
January 24, 2023
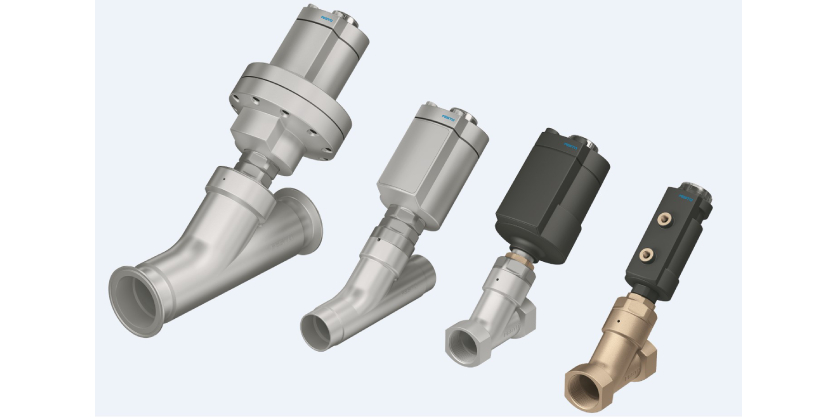
The new Festo VZXA family of pneumatically actuated angle seat valves delivers installation, maintenance, operational, and inventory benefits thanks to a unique modular design.
When a VZXA actuator is removed for maintenance or changeover, for example, the stem, seat, and seal stay inside the valve body, allowing the process system to remain pressurized. In applications containing hazardous materials, those materials reside safely within the system, saving cleaning time and lowering health and safety risks of contamination. No other angle seat valve offers these operational benefits.
Reinstalling the actuator is simply a matter of screwing it into the valve body. The actuator does not have to be pressurized, which eliminates strain on the stem, seat, and seal and lowers the potential of damaging the valve seat. The modular design is ideal for valve manifold applications where speedy assembly, ease of maintenance, and compact size are pluses.
Modularity lends itself to valve body repair as stem, seat, and seal are individual components with readily available replacement parts. The valve family’s standardized design ensures every VZXA actuator is compatible with every valve body in the family. The universal fit between actuators and valve bodies simplifies ordering and inventory management.
An online valve configurator enables the correct valve for the application – standard or custom – to be specified and ordered in a matter of minutes. Normally open, normally closed, and double acting actuators are available.
Line connections include threaded, sanitary clamp, and welded end. Sanitary clamps work best in washdown and clean-in-place applications where quick connect/disconnect are beneficial. Valve body materials include stainless steel and brass. Actuator bodies are stainless steel or polymer. Each VZXA actuator has an optical indicator showing valve position.
Accessories include sensors for digital feedback, a piloting banjo valve, and stroke limiter for the open stroke. Valve body sizes up to two inches are assembled at the Festo Mason, Ohio, Global Production Center. Delivery can be expected within a week for both standard and custom configurations.
Angle seat valves are used for high volume flow control of water, steam, and corrosive materials. They are in high demand because of their nearly universal applicability in terms of wide temperature and pressure ranges, compact footprint, long service life, low cost, material options, high performance, and ready availability.
A short informational video provides a helpful summary of the features and benefits of the VZXA family as well as showing the modular design.
The VZXA easily adapts to the task in hand thanks to its range of variants, thus maximising flexibility and minimising the effort involved in designing your application. The carefully thought-out product architecture means valve bodies and actuators can be freely combined. The modular product concept makes it easier to modify and maintain systems without having to remove the entire valve.
More Information about the VZXA
Advantages of working within the Festo ecosystem of less engineering overhead, fast time to market, and seamless connectivity.
Related Story
How Festo Is Filling the Training Gap with Workforce Development
Labour and skills shortages are among the most pressing challenges that manufacturers face today. Access to a large, high-quality workforce is critical for manufacturing to be successful. This workforce is the driving force for innovation and is essential to making the most of new technologies and production methods.
Canadian Manufacturers & Exporters recently conducted a survey of over 225 manufactures from across Canada and found that more than 85% of manufactures are struggling to fill vacancies, youth are increasingly unprepared and uninterested in working in manufacturing, and employers lack the capacity to invest in skills and training.
In short, labour and skills shortages are dampening manufacturing in Canada, and it is necessary to provide solutions to improve this situation. And there are steps that can be taken right now to make improvements today and for the future of work.