Festo Introduces a Heavy-Duty Palletizing Gantry With Lift Capability of Up to 200kg per Pick
April 4, 2024
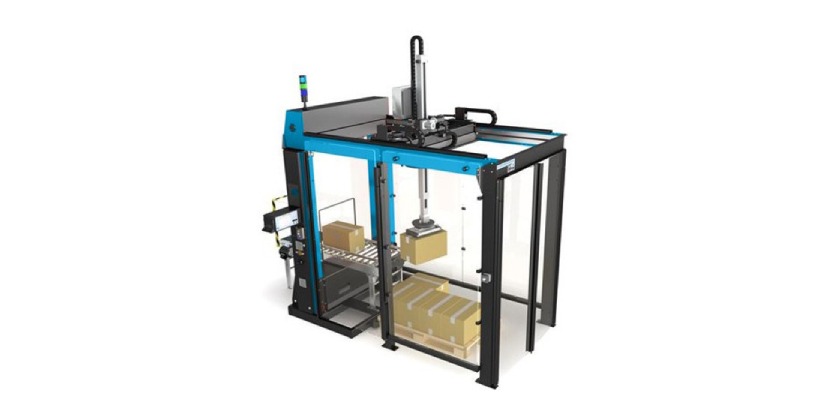
Festo design tools, component availability, and ready-to-assemble kits shorten projects and lower overhead
Festo introduces a heavy-duty Cartesian gantry for palletizing with lift capacity of up to 200kg, Z-axis stroke lengths exceeding eight feet, and speed of up to five feet per second. With free online design tools; off-the-shelf servo drives, motors, and other components; and quick assembly kits, this Festo palletizing solution shortens project time and reduces engineering and assembly costs.
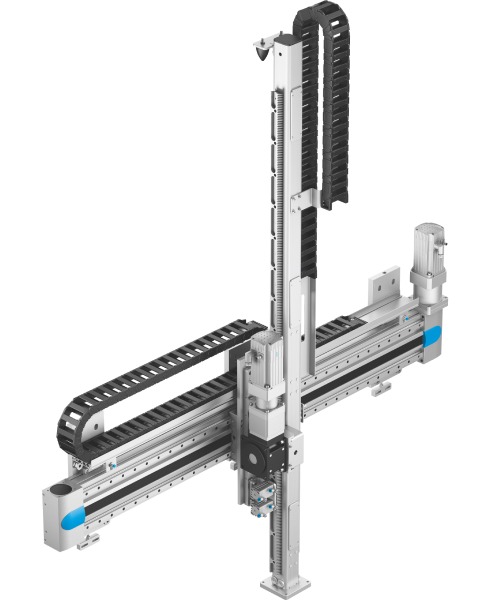
Robust, high rigidity electric actuators provide the core of this new solution. These actuators include the tough cantilevered Z-axis EHMH rack and pinion actuator for loads up to 200kg and the ELCC toothed belt actuator with ball bearing guides for loads up to 100kg. For an X-axis solution, the Festo EGC-HD heavy-duty toothed belt or ball screw actuator is ideal for most heavy duty applications.
Cartesian gantries are lower cost than six-axis robotic palletizers. They offer superior accuracy and speed whether handling a small load over a long reach or a heavy load over short distances. Unlike six-axis robots that lose accuracy and lift capacity at the periphery, gantries cover the entire workspace with equal accuracy, speed, and performance at each point on the X/Y axes. Cartesian palletizers offer a smaller footprint than six-axis robots, a plus for today’s smaller and more compact operations.
OEMs, system integrators, and end users utilize the free online design tool, Handling Guide Online (HGO), to specify a gantry in as little as 20 minutes. Engineers simply input application parameters such as distance, speed, torque, weight, and HGO offers a range of solutions to choose from based on performance and cost. HGO ensures interoperable components that are accurately sized for the system. Matched components lower risk and improve performance. Each gantry has a single unique overall part number, making reorder of any component under that number a quick and accurate process.
At the end of the specification session, HGO provides 2D and 3D CAD files, parts list, quotation, and expected delivery date. Having the CAD files allows system design to continue while the gantry’s ready-to-assemble kit is prepared.
Used in combination with HGO, the Festo Motion Control Package (FMCP) software designs the control panel, which arrives pre-built. Users simply connect the cables and program the robot using function blocks. Crews can complete the initial set up in hours or days, not weeks.
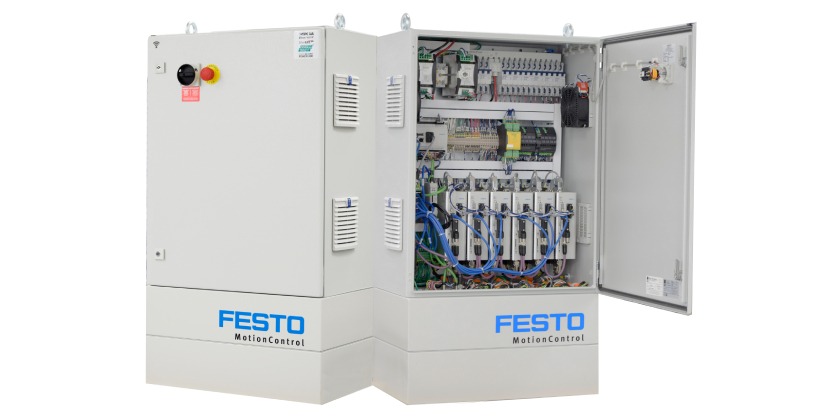
Other key components in the Festo Cartesian palletizer include the compact CMMT-AS servo drive that now features multiprotocol capabilities – one drive for EtherNet/IP, PROFINET, EtherCAT, and Modbus TCP protocols. CMMT-AS drives are in stock and ready for shipment. These drives provide seamless interpolation and motion control. The CMMT drive family (from 300 Watts to 12 KW) means one multiprotocol series covers the gamut of motion control challenges.
For control, a single CPX-E Codesys-based controller can manage multiple synchronized gantries while communicating with third-party controllers. The compact size of the CPX-E makes it an ideal alternative to the larger controllers required to manage multiple articulated robots. Festo also offers the CDPX HMI that features an IP67 rating for on-unit mounting, increasing ease of use and reducing space in the control panel.
More Information
For more information on the advantages of working within the Festo ecosystem of less engineering overhead, fast time to market, seamless connectivity, and high-quality components, visit www.festo.ca
Related Story
Festo Electric and Pneumatic Intralogistics Solutions Push/Sort, Grip/Pick, and Lift/Convey
New distribution centers and existing facilities deploy robotic systems to lower labor, increase throughput, and reduce the risk of error when moving their products internally. Seventh-axis robots – robots on an electromechanical linear actuator moving horizontally, vertically, or both – offer productivity and cost advantages in picking and placing and unloading and loading applications.