Enhance Your Performance – New OCF Features Released!
AGLIOX is excited to unveil the cutting-edge advancements in their Autonomous Mobile Robots (AMRs) – the OCF (Omnidirectional counterbalanced Forklift)
July 25, 2023
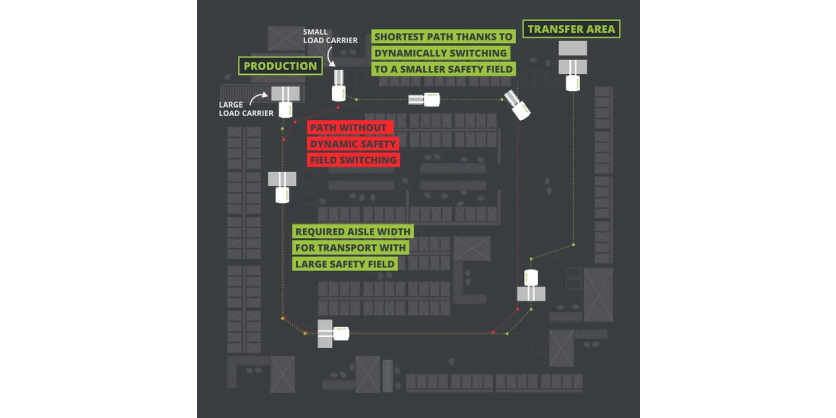
At AGILOX, they always prioritize safety and efficiency in all their solutions. They are thrilled to announce the release of three remarkable features that will revolutionize the way you handle material handling tasks in your facility. From Auto Fork Adjustment to Active Pick-Up Monitoring and Dynamic Safety Field Switching, these game-changing enhancements for our OCF will elevate your workflow, streamline processes, and ensure the utmost safety for your workforce. Here they dive in and discover how the OCF is moving and lifting to make work life easy and safe!
Dynamic Safety Field Switching
Customers often need to move several different load carriers from station A to station B as quickly as possible. Autonomous Mobile Robots (AMRs) use so-called safety fields in the travel direction to ensure safe transport and to prevent endangering personnel in the immediate vicinity. The size of the safety field usually corresponds to the size of the load carrier (LC).
In the past, if the AMR needed to move different types of load carriers, it usually employed a larger safety field since it could not distinguish between two different LCs. This often forced the AMR to travel longer distances than strictly necessary, resulting in significantly longer cycle times for entire swarms of AMRs. Our new Dynamic Safety Field Switching feature eliminates this inefficiency.
Process
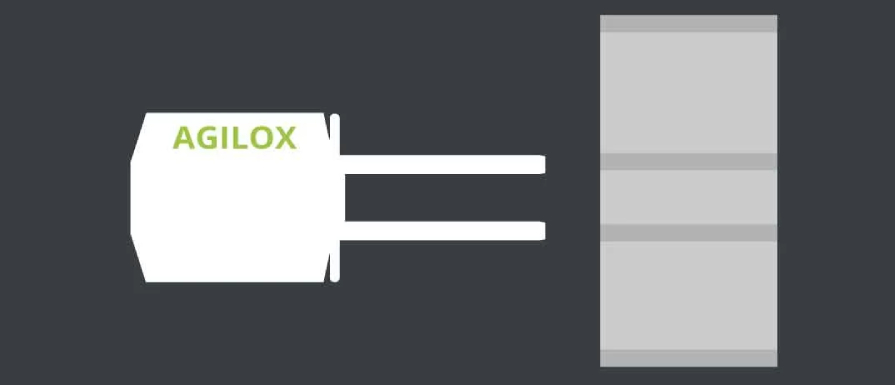
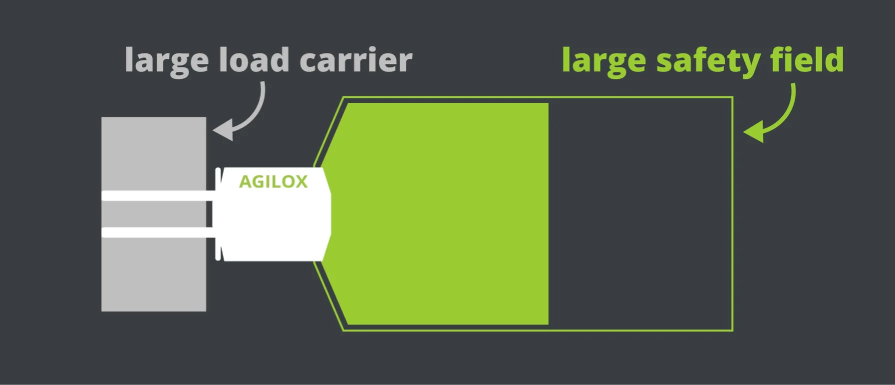
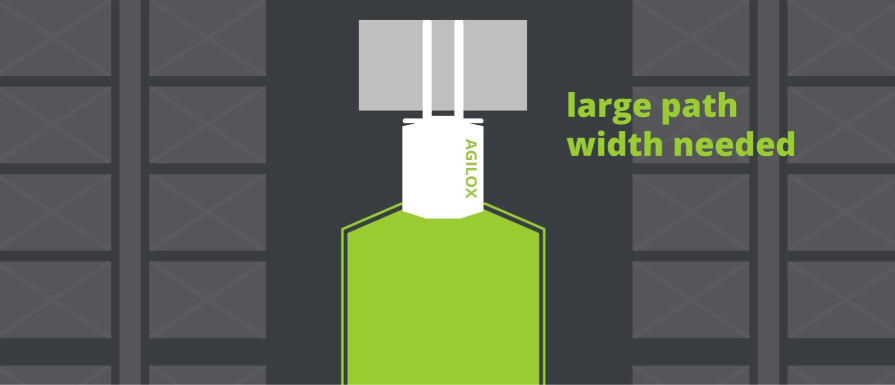
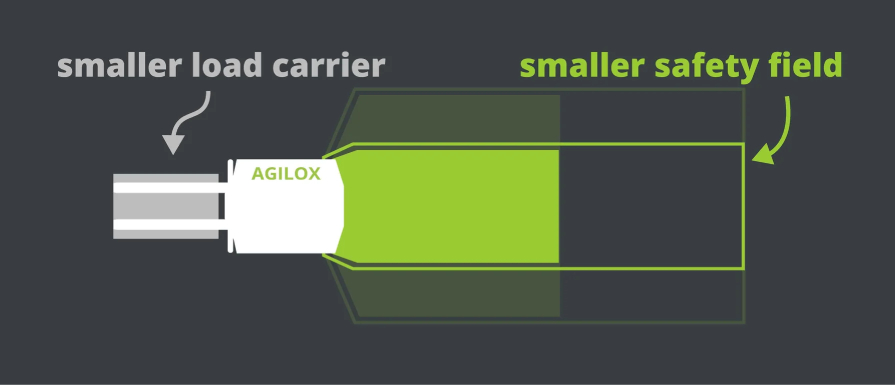
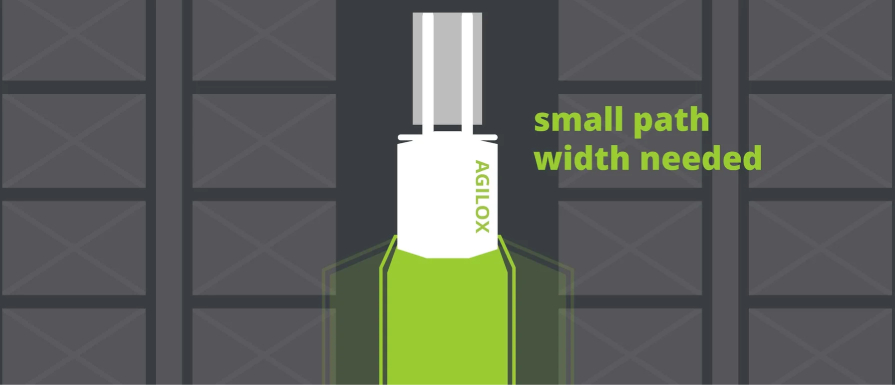
- The size of the safety field is adjusted to the load carrier type, thus optimizing paths and significantly reducing cycle times.
- The AGILOX scans the load carrier and dynamically adjusts the safety field to the size of the LC.
- The robots plan the optimal route depending on current load carrier dimensions, safety fields, and available aisle widths.
- The OCF detects the smaller load carrier and automatically adjusts its safety field to the size of the load carrier.
- Thanks to XSWARM technology, we detect the OCF environment and automatically adjust its route depending on the size of the current load carrier.
Auto Fork Adjustment
Different load carriers often require different settings for the distance between the forks. A smaller load carrier, such as a Euro pallet, requires different fork settings than a larger specialty load carrier. If both load carriers are transported by the same vehicle, the Autonomous Mobile Robot (AMR) has to adjust its forks to the particular load carrier.
The OCF now features automatic fork width adjustment, which allows for different load carriers to be used in the same workflow without having to make any manual adjustments, making time-consuming changeover times a thing of the past.
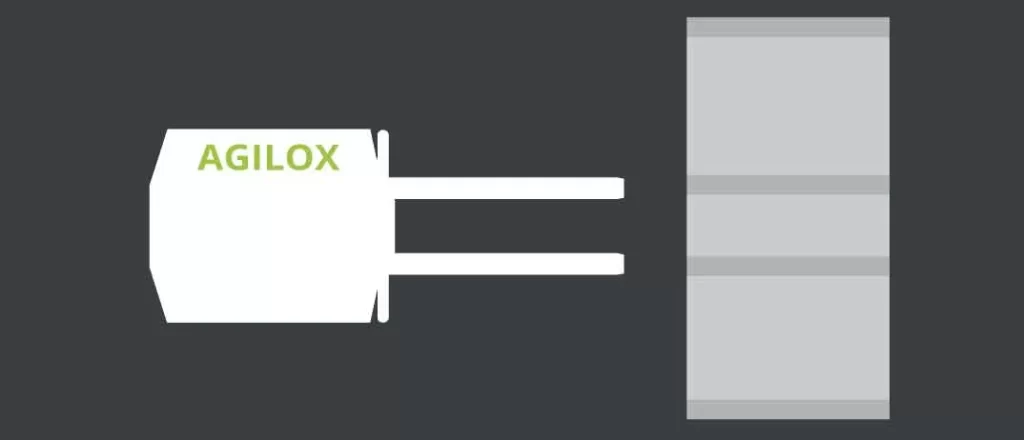
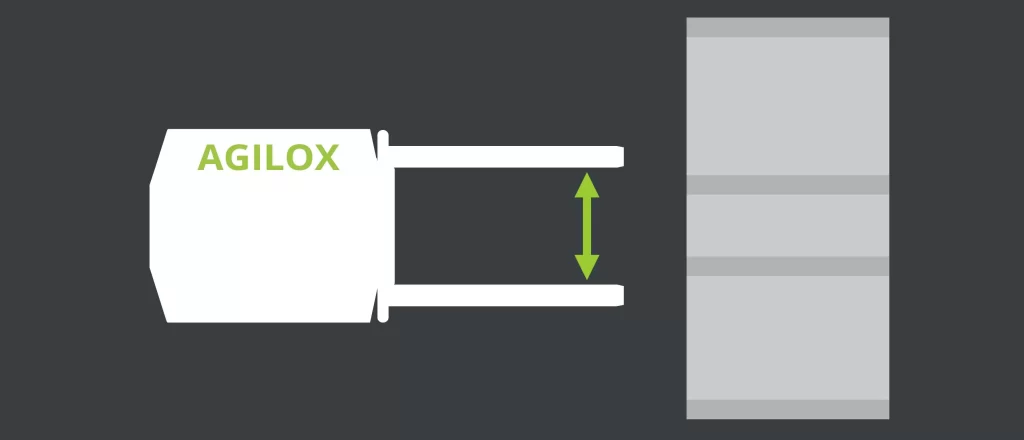
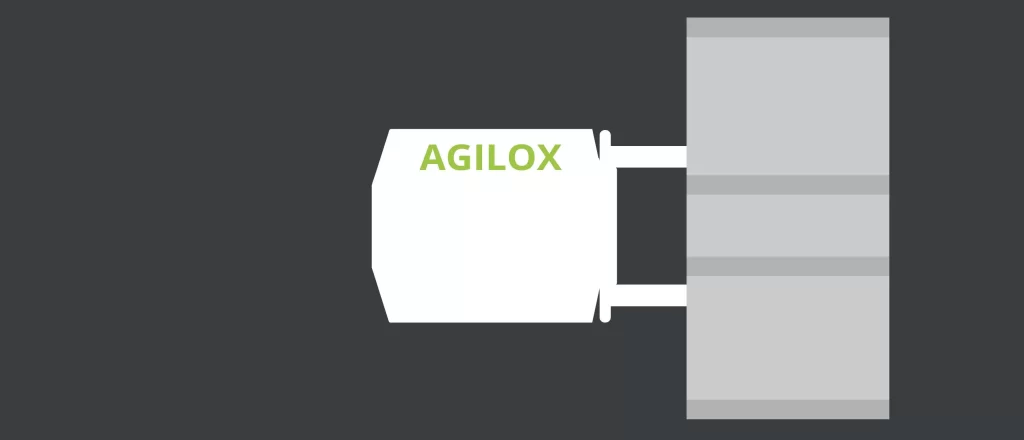
- The OCF uses its sensors to check the dimensions of the load carrier before the forks move in.
- It then adjusts the fork width toa previously defined specific load carrier setting.
- This allows for more flexibility in picking up different loads.
Active Pick-Up Monitoring
AGILOX’s Autonomous Mobile Robots adhere to the highest safety standards. All of their vehicles comply with the current ISO 3691-4 safety standard for driverless industrial trucks.
Their new Active Pick-Up Monitoring goes one step further, improving those very high safety standards even more. Their OCF will scan the entire space between the vehicle and the load carrier for any obstacles, such as personnel when preparing to pick up the load. If anyone is detected in this area, the vehicle will stop immediately, ensuring you and your staff enjoy even better protection.
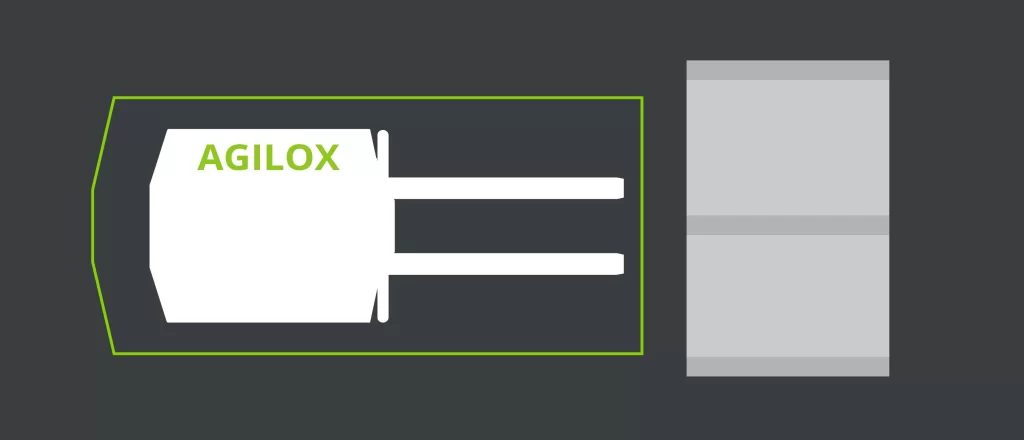
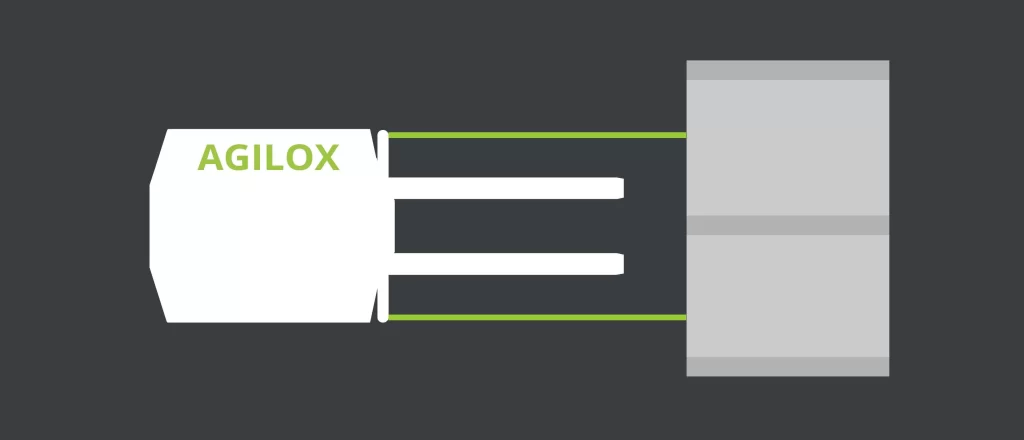
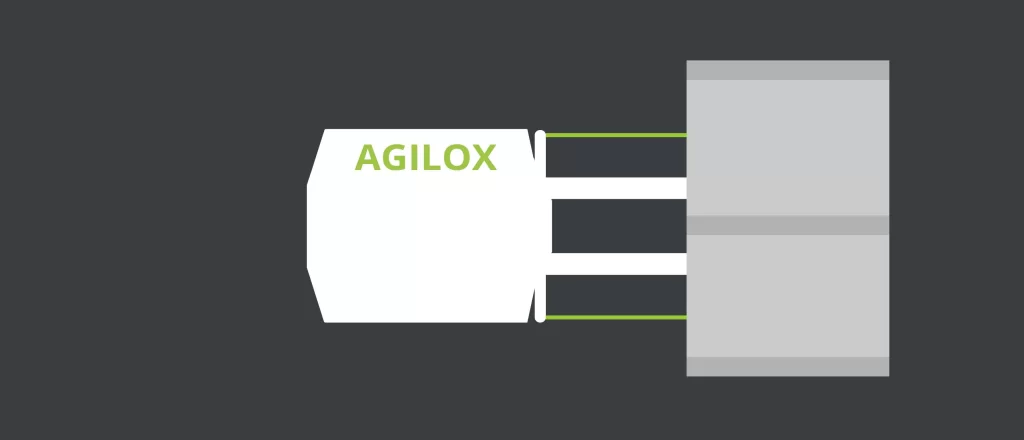
- The horizontal safety laser scanner runs a one-time check to determine if an object is under the load.
- If no objects are detected, the Active Pick-Up Monitoring feature is activated to monitor the spacebetween the AMR and the load carrier (LC) for any personnel.
- Upon entering the station,Active Pick-Up Monitoring remains active to provide the highest level of protection
AGILOX – Moving and lifting to make work life easy and safe
In conclusion, AGILOX’s OCF with its innovative Auto Fork Adjustment, Active Pick-Up Monitoring, and Dynamic Safety Field Switching features is setting new standards in the world of Autonomous Mobile Robots. With a relentless focus on safety, efficiency, and adaptability, they are dedicated to providing you with the most advanced solutions for your material handling needs.
Are you ready to take your productivity to the next level? Embrace the future of automation with AGILOX and experience the seamless integration of technology and safety. Say goodbye to manual adjustments, long cycle times, and unnecessary risks, and say hello to an optimized, agile, and secure material handling environment.
Contact them today to learn more about the OCF and how it can transform your operations. At AGILOX, they are committed to moving and lifting to make work life easy and safe. Together, they can help you unlock the potential of autonomous material handling and shape a smarter, more efficient future for your business.
More Information
Related Story
AGILOX in the Limelight at AUTOMATE 2023
AGILOX is producing the AMRs for tomorrow with a team of highly skilled technicians and hardware and software engineers. All the mechanical components, electrical engineering, and the entire software solution are developed in-house at their headquarters in Austria. They draw on feedback from their team of salespeople and field technicians, and a decade-long track record of in-depth knowledge of material handling processes. Customers choose AGLIOX for their logistics planning because “it just works.”