Control Cabinet-Free Automation as a Game Changer in Machine and System Engineering
May 6, 2024
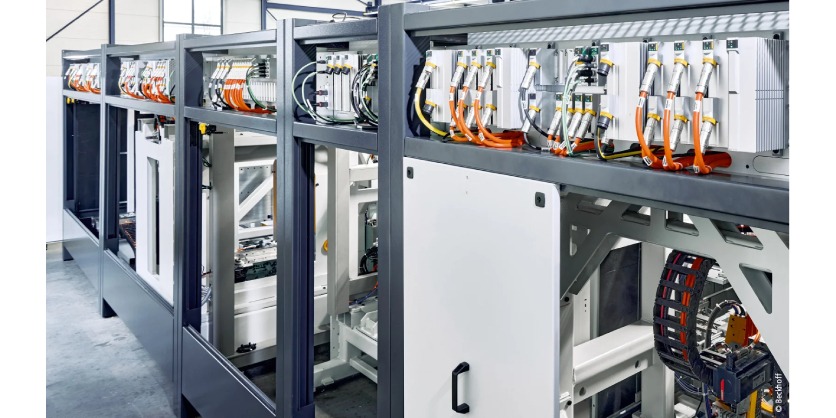
MX-System for a window profile processing machine
“The MX-System is changing the face of design and installation in the world of machine building,” explains Ludger Martinschledde, Managing Director of Schirmer Maschinen GmbH. In its initial use in a system for processing profiles, the pluggable system solution for control cabinet-free automation from Beckhoff ticked all the boxes in every project phase, from planning and design through to installation and commissioning.
Window and door construction is a high-tech business. This much is evident right from the first process step, with the fully automatic processing of raw bars on a profile processing machine from Schirmer Maschinen GmbH. Schirmer was founded in 1979 and was Beckhoff’s first customer. The company has relied on PC-based control technology from Beckhoff for over 40 years now, from the first positioning controller to the new MX-System.
This pluggable system solution for control cabinet-free automation aligns particularly well with Schirmer’s machine concept: the development of custom machines based on largely standardized process modules to create customer-specific solutions with high output and flexibility in terms of profiles and processes. The company has been a member of Beckhoff Automation Group since 2016 and currently employs around 250 people.
What does a Schirmer machine do?
Schirmer machines can be used for a variety of different processes: The individual parts for window frames and sashes are produced from approximately 6-meter long profile bars in a continuous process. As far as possible, all drilling, milling, and punching operations are carried out on the raw bar, followed by cutting and processing the ends. While the profile bars are being processed, the reinforcement profiles are cut to size on a separate line with the option to automatically insert and position them in the PVC profile. This is followed by further processes such as screwing in the profile and reinforcement, steel processing (drilling, milling), and inserting and screwing in the locking mechanisms.
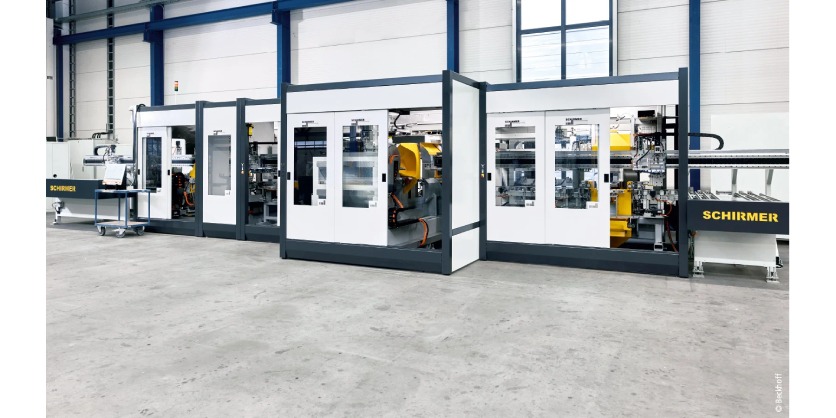
As the Schirmer machines are required to handle a wide variety of frequently changing profile geometries, the conversion process takes place automatically. “Manual set-up is definitely out of the question for us,” says Ludger Martinschledde. With this being the case, many stops and brackets have to be positioned on a fully automatic basis. “Last year, for example, we implemented a line with a total of 210 axes,” recalls Ludger Martinschledde, outlining the requirements profile for the control platform.
Control cabinets determine production processes
The electrical equipment used in Schirmer machines to date reflects the current standards. Drive amplifiers, power supplies, power distribution, and PC-based control technology are all installed in control cabinets. On Schirmer machines, there are typically several of these stations set up along the machine, where cables from usually 2 to 3 process modules of the machine are routed and connected. EtherCAT I/Os are also used in sub-distributors. These are used to collect actuator and sensor signals from each of the individual process modules; however, combining several process functions in a single control cabinet and using sub-distributors to which the signal lines are clamped rather than plugged in represents a compromise for modular machine building.
Ludger Martinschledde describes the disadvantages of this solution as follows, “This means that most of the electrical installation and commissioning will only take place during final assembly, which is precisely when we are aiming to commission the system as quickly as possible before taking it apart again for delivery.” The discrepancy between the modular machine concept and the central control cabinets has long been identified by Schirmer as an obstacle to achieving a more efficient project workflow.
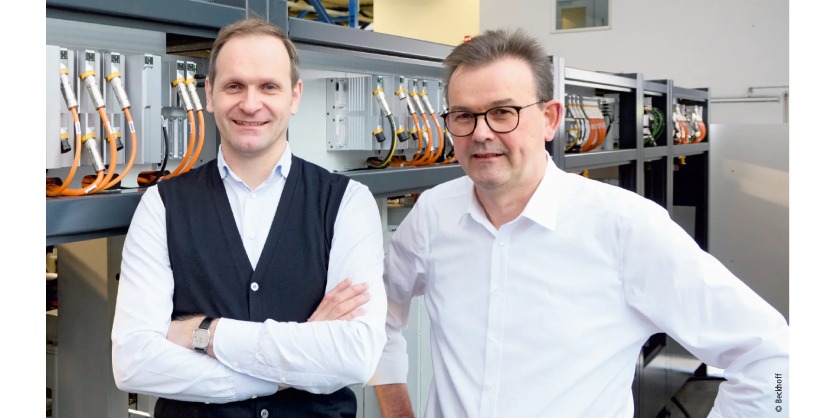
When Ludger Martinschledde and the design engineers at Schirmer heard about the possibilities of completely control cabinet-free automation with the Beckhoff MX-System in 2021, they were understandably intrigued. “The design engineers and Ludger immediately recognized the potential of the MX-System for their modular machine building projects,” recalls Daniel Siegenbrink, Product Manager MX-System at Beckhoff.
Completely new and control cabinet-free machine design
Schirmer is pioneering the MX-System on one of its machines for the first time, marking a new direction with the primary aim of optimizing the lead times and processes involved in machine building. In place of the control cabinets that used to stand next to the machines, MX-System baseplates can now be seen directly on the steel frames of the process modules. As for the sub-distributors, their tasks have either also been accommodated in the MX-System or else been replaced by decentralized I/O modules (EtherCAT Box modules) from Beckhoff. This combination of MX-System and EP box modules allows all cables to the motors, sensors, and valve terminals to be pluggable.

For Schirmer, the crucial advantage of the MX-System lies in restructuring internal processes. After all, this pluggable system solution allows the machine builder to install all the electrical components of a machine module during pre-assembly and connect them with ease using pre-assembled cables. Another crucial aspect is that, during pre-assembly, the machine modules are freely accessible from all sides, which makes it much easier to lay and connect the cables. As Daniel Siegenbrink explains, “This saves a lot of time and significantly increases the efficiency of our workflows.” This not only applies to assembly, but also begins with planning, preparatory work, and material provision in the production phase.
The function modules of the MX-System also eliminate the need for the complex individual wiring of numerous sub-components that is common in conventional control cabinet design. This prevents wiring errors and streamlines the diversity of parts. As a result, the required components (MX-System baseplates and modules as well as the pre-assembled system cabling) can be picked from the warehouse for pre-assembly directly after the electrical planning. “The aim here is to achieve an order-independent warehouse that we can manage with minimum stock levels, requirements, and replenishment times,” explains Ludger Martinschledde.
For Schirmer, this initial development project has also provided two further insights: Last-minute change requests are much easier to implement and require less effort – even in a late project phase. And with modular partial commissioning, any functional errors can be detected at an early stage and rectified without time pressure.
Fast and efficient to the end customer
In the final assembly phase, the machines take up a large area, so processes have to run quickly at Schirmer to make room for the next systems in the queue. Ludger Martinschledde notes that the upstream processes – particularly electrical installation and partial commissioning – significantly reduce downtimes and increase space efficiency in the process. This allows Schirmer to assemble, inspect, and deliver more systems in the same hall.
As a machine builder with an export share of 75%, the universal use of the automation solution is another important aspect for Schirmer. While previously the future installation location had to be taken into account during electrical planning and material procurement, the machine can now be used worldwide without requiring any time-consuming modifications since the MX-System is IEC-, UL- and CSA-compliant. This stands in stark contrast to the situation with conventional control cabinets, and further increases the degree of standardization at Schirmer.
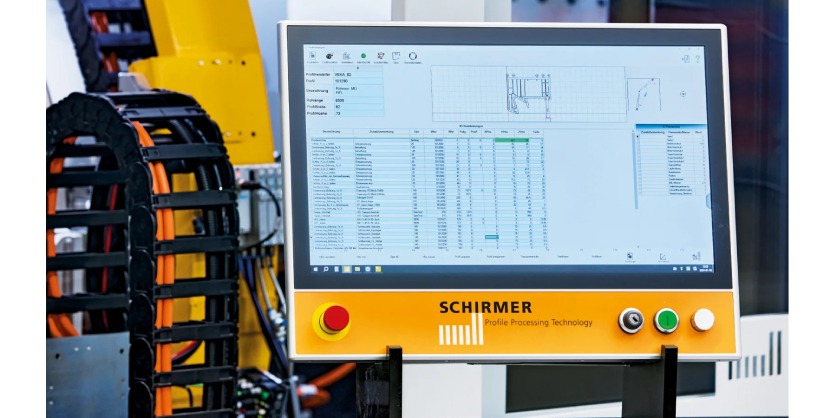
But it’s not just Schirmer that benefits from control cabinet-free automation, as the MX-System also offers tangible benefits for end users. These notably include better accessibility to the machine structures, and the reduced space requirements due to the elimination of control cabinets. This means that the production facilities can be positioned closer together on the shop floor, optimizing the valuable space without, for example, violating escape route requirements. The 10-fold reduction in the number of components also reduces the size of the spare parts warehouse.
The Beckhoff Diagnostics App, which is being launched on the market together with the MX-System, is a tool that makes it easier for maintenance personnel to localize and rectify faults. “The end-to-end pluggability and the use of the diagnostic app as a replacement for the multimeter means that no specially trained electricians are required to connect or replace the MX-System modules,” emphasizes Daniel Siegenbrink.
Successful start to control cabinet-free automation
The use of the Beckhoff MX-System has resulted in significant advantages and optimizations throughout the entire process chain at Schirmer. This includes a reduction in the previous workload for electrical planning by around 50%, as the usual two to three weeks of assembly time for conventional control cabinet design was cut down to just a few hours of system assembly. Ludger Martinschledde also expects a significant reduction in downtimes at the final assembly stage.
The new machine was presented for the first time at Fensterbau Frontale 2024, the industry’s leading international trade fair, and Ludger Martinschledde believes that this will certainly not be the last system of its kind on the way to a new era of control cabinet-free automation: “Schirmer will continue to rely on this innovative solution from Beckhoff. We are fully on-board with transitioning our machines to control cabinet-free automation with the MX-System, and this will also apply to the product lines for aluminum and steel profiles in the future.”
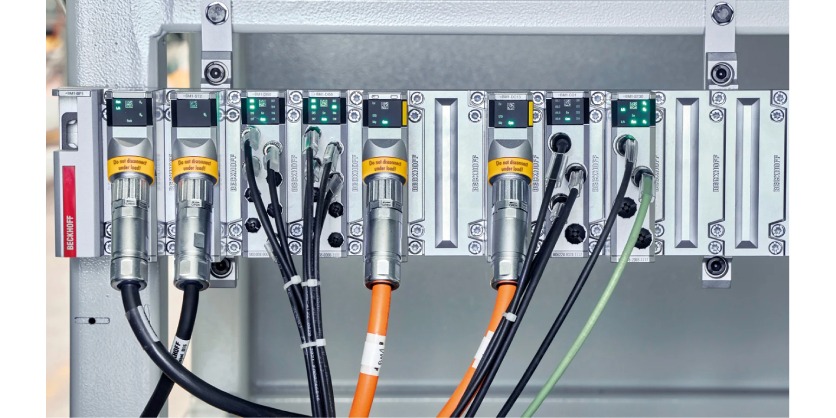
Features of the Fensterbau Frontale machine
- 14 m system length
- 11 machine process modules
- 67 axes
- 23 AM8000 synchronous servomotors
- 4 AL8000 linear servomotors
- 28 AM8100 synchronous servomotors
- 12 three-phase asynchronous motors
- 18 valve terminals
- 11 MX-System baseplates
- 118 MX-System function modules
- 1 IPC module
- 39 system modules
- 34 I/O modules (including 28 for compact drive technology)
- 7 relay modules
- 37 drive modules
- 64 EtherCAT Box modules
- 1 customer-specific control panel
More Information
- Pluggable system solution for control cabinet-free automation: The MX-System
- SCHIRMER Maschinen GmbH
Related Story
Beckhoff Redefines Cabinetless Automation with New Plug-and-Produce MX-System
The MX-System from Beckhoff is a flexible, space-saving and intelligent automation hardware system that can completely replace conventional control cabinets, creating entirely new levels of efficiency in plant automation. Control system installation processes that normally took 24 hours or more can now be completed in just one hour.