Comau’s Digital Technologies to Improve Battery Cell Production Reaching up to Zero Defects for The Battwin Project
April 22, 2024
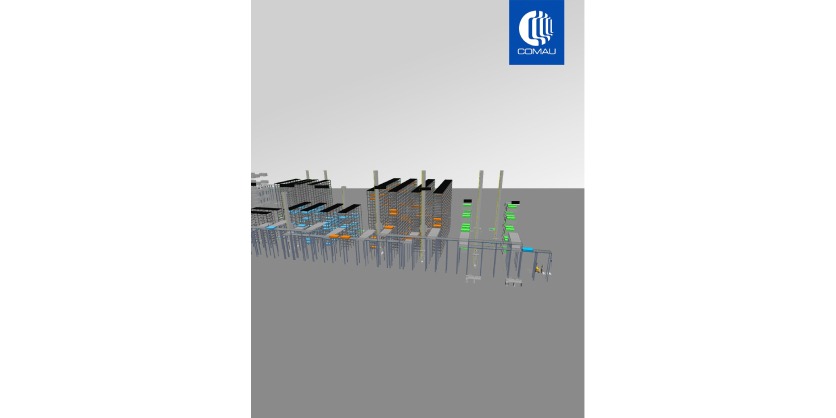
Comau’s Digital Technologies to Improve Battery Cell Production Reaching up to Zero Defects for The Battwin Project
- Comau expands its commitment to large-scale and cost-effective battery manufacturing solutions by joining yet another important EU project
- BATTwin seeks to develop a Multi-level Digital Twin platform to reduce defect rates in battery production lines arriving at a zero-defect manufacturing goal
- Comau will leverage its 360° process and advanced digitalization competencies to identify, collect and analyze data parameters to help improve battery cell manufacturing quality
- Comau will also distribute real-time defect data via its proprietary In.Grid IoT platform and develop modeling simulations of the manufacturing plants
Comau has joined yet another important pan-European energy transformation initiative, in the field of e-Mobility, this time in support of the BATTwin project, in the field of e-Mobility. Under the scope of its participation, Comau will work with the project’s partners to identify and define crucial data parameters, hardware, software and digitalization technologies that can be used to meet the goal of zero-defect cell production. After which, the company will leverage its 360° process and advanced digitalization competencies to define and implement a multi-sensor data acquisition and management strategy to improve battery cell manufacturing quality.
Funded by the European Commission within the framework of the Horizon Europe research and innovation program, BATTwin, coordinated by Prof. Marcello Colledani, Department of Mechanical Engineering, Politecnico di Milano, aims to develop a Multi-level Digital Twin platform that will help reduce defect rates in Lithium-Ion battery production, which the organization expects could reach up to 30% during the ramp-up phase of Europe’s new Gigafactories. With the goal of reaching zero-defect manufacturing in European Gigafactories, the digitalized virtual environment will be deployed and tested in-field to validate its flexibility, scalability and overall effectiveness.
Under the scope of the project, Comau will leverage its longstanding expertise in digitalization, digital twinning, process simulation and electrification to enable automatic data acquisition and transmission to a cloud-based virtual environment. The company will also perform Discrete Event Simulation (DES) modeling at a production level and develop a digital twin for the production system design and re-design. This will allow cell manufacturers to optimize their work flow, analyze cycle times, prevent bottlenecks and manage both energy consumption and manufacturing performance at a machine level. Thanks to the continuous information feed to and from the virtual environment, manufacturers can instantly recognize and prevent potential production issues, which will further increase overall quality and cost-effectiveness within the battery cell production process.
“Comau’s electrification strategy is founded upon innovative ideas and the continuous Research & Development of next generation battery technologies, cell formation competencies and alliances with pan-European partners and organizations, such as Upcell. This groundbreaking project, which was conceived within the framework of various Upcell discussions, aligns perfectly with our future-focused technology roadmap,” explains Daniela Fontana, Comau’s Battery Innovation Manager.
In addition to its partnership with Upcell – European Battery Manufacturing Alliance, an association that promotes the creation of an integrated European value chain for the development and production of electric batteries, Comau’s steadfast dedication to energy transformation solutions is further seen through its active involvement in various industry alliances; among which three of Europe’s top battery consortiums: European Battery Alliance (EBA), the Batteries European Partnership Association (BEPA) and the European Technology and Innovation Platform (ETIP).
The company also participates in numerous other projects regarding electrification as part of the HORIZON 2020 and HORIZON EUROPE programs. These include, but are not limited to, SPINMATE, aimed at large-scale manufacturing of next-generation solid-state battery cells and modules, GIGABAT, a collaborative e-Mobility project aimed at strengthening the EU production chain for large-scale cell manufacturing, and FASTEST, which seeks to accelerate the development process of reliable, safer and more durable batteries and Flex-BD, a battery recycling project.
Related Story
Comau Will Significantly Accelerate the Testing and Verification of Automotive and Stationary Batteries
Comau has committed to developing the digitalization strategy for a next-generation battery systems testing platform as part of a multi-country, multidisciplinary consortium in support of the FASTEST project. Under the scope of the project, Comau will leverage its longstanding expertise in digitalization, process simulation and electrification to significantly accelerate the testing and verification of automotive and stationary batteries. This is expected to reduce the overall time and costs of battery production by at least 20% in addition to decreasing the number of physical experiments and the subsequent reduction in materials costs.