Comau Grants Flexibility To Hycan Electric Vehicles With Its Innovative Body Welding Solution
April 27, 2023
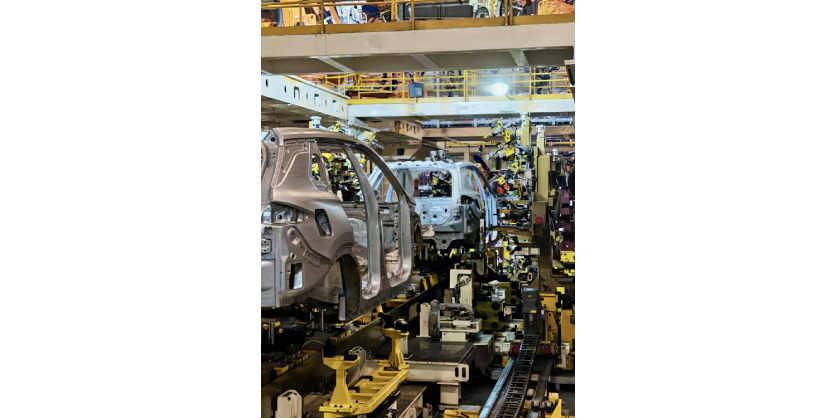
- Comau’s customized welding solution is being used to mass produce the brand’s first electric Sedan and SUV
- Hycan can achieve random mix production of up to 6 models with an annual capacity of 200,000 vehicles
- The solution also ensures full flexibility to seamlessly introduce a variety of new models in the future, allowing Hycan to achieve true zero loss production
Comau has supplied Hycan Automotive Technology Co., Ltd. (Hycan) with a highly intelligent welding solution for its framing line. The innovative system ensures multi-model manufacturing of new energy vehicles, high JPH (Jobs per Hour) and a concrete reduction in production losses. Deployed at the Hycan Hangzhou manufacturing base, the flexible automated production system can randomly switch between four different platforms, is fully compatible with the existing manufacturing platforms and is mass producing the brand’s smart, pure electric A06 sedan and stylish, intelligent-driving, pure electric SUV Z03 at a cycle efficiency of 60 JPH.
Hycan Automotive Technology Co., Ltd. (Hycan) specializes in the development of electric vehicles, with a strategic focus on attracting young generations in the Chinese market. Given the diverse preferences of its target users, the need to develop a rich product range in a short period of time, and the rapid iteration of its offer, Comau engineers made sure the highly flexible welding assembly line could keep pace with the automaker’s evolving manufacturing needs. In addition to facilitating the seamless introduction, adaptation and scaling of new Hycan models, it grants Hycan complete flexibility in the future.
The comprehensive solution is based on a customized version of Comau’s Opengate framing system, which grants flexible high-precision body-in-white assembly, and virtual commissioning technologies.
Comau also added a flexible servo positioning mechanism to the conveying system to help shorten the production cycle while ensuring both economies of scale and the ability to meet Hycan’s product diversification needs. With an OEE (Overall Equipment Effectiveness) exceeding 90%, the solution delivers an annual production capacity of up to 200,000 units. And because it can complete random mix production from 1 to 6 models, it allows Hycan to achieve true zero-loss production.
“The results of the first collaboration between Hycan and Comau are very satisfactory. Comau’s innovative technologies and professional engineering management throughout the project have fully demonstrated its position as a leader in body solutions and provided an important guarantee of the processing efficiency and quality for our first model production project,” said Feng Yiqiang, Director of Hycan Intelligent Process.
Feng Yiqiang, Director of Hycan Intelligent Process
“This important project in the electric vehicles field is the result of working side-by-side with the Hycan team to achieve their targeted production capacity while meeting their challenging product diversification needs,” explained Gaetano Cantalupo, Comau Head of Countries Cluster APAC. “The highly intelligent framing line reflects Comau’s commitment to improve flexibility and efficiency in body assembly and leverages our longstanding expertise in process and design excellence.”
Gaetano Cantalupo, Comau Head of Countries Cluster APAC
More Information
Body Assembly: Body Assembly and Production Processes
Related Product
Comau Is Developing A New Mobile Robotics Solution Featuring Collaborative Robots In The Context Of 3 EU Projects
- Part of R&D initiatives and applied within three different EU projects, the new Mobile Robotic Arm combines collaborative safety features, industrial performance and complete mobility when and where it is needed
- Modular approach enables the robot to address a large number of applications in different areas of the plant without changing the SW and HW architecture
- The platform can be used across multiple different industries
Comau is designing a powerful mobile robotics platform as part of an open, highly collaborative production environment, in the context of 3 different European Projects.