Comau Delivers a Highly Flexible Assembly Solution for JMC Ford’s High-End Pickup Manufacturing
October 21, 2024
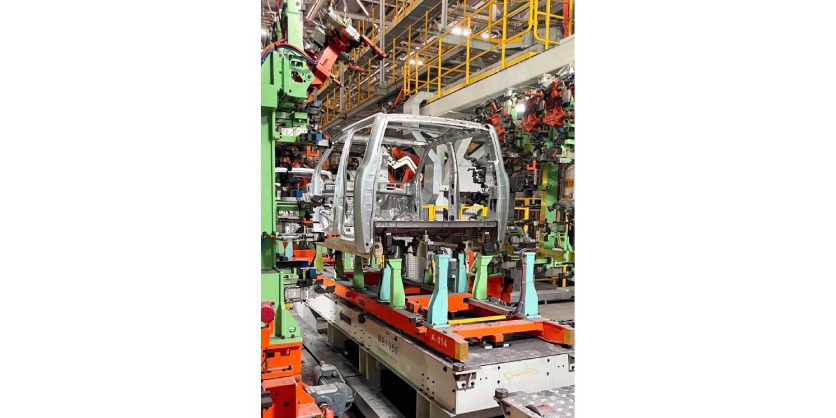
- Comau has designed and developed a fully automated assembly line to produce premium pickup truck models at the JMC Ford Xiaolan plant- The highly flexible welding automation solution has enabled 3+1 multi-vehicle co-production line with a 100% automation rate
- The project implemented the mainline and the floor line, achieving an annual capacity of 125,000 units
- The advanced solution addresses current production needs while laying a solid foundation for future expansion
Comau has designed and deployed a flexible and comprehensive Body-In-White (BIW) manufacturing solution for JMC Ford to produce high-end pickup trucks at the Xiaolan plant in China’s Jiangxi province. The project established a highly versatile production line capable of accommodating various models and configurations, including JMC Ford’s new pickup truck brand Da Dao (Avenue) and Ford’s first pickup truck model introduced in the Chinese market, the Ranger. The fully scalable, state-of-the-art solution delivers a 100% automation rate while ensuring the vehicle quality and performance JMC Ford is known for, positioning JMC Ford to better address the growing demand for diversified and personalized products.
Comau’s body-in-white welding solution improves welding accuracy and stability, thus ensuring the final product’s structural integrity and safety. The solution also optimizes production processes and includes the adoption of advanced automation technologies to enhance production efficiency, reduce cycle times and increase output. And by incorporating both the welding and tightening guns within an integrated system. Comau was able to minimize the need for frequent tool changes. The solution also leverages advanced vision inspection technology for better quality control and allows JMC Ford to reduce their equipment investment and maintenance costs.
The flexible and removable fixture loading table that Comau developed for the project can be easily reconfigured for different assembly tasks and parts. This design reduces line changeover times, reduces tooling investments, optimizes workflow, and improves product quality. Moreover, the comprehensive manufacturing set-up also features Comau’s OpenGate system, which ensures geometrical accuracy while granting inherent flexibility with an aggressive average switching cycle time of just 50 seconds.
“Our goal was to create a more efficient, reliable, and flexible production line for the rapidly expanding pickup truck market, and we have achieved impressive outcomes,” said Ma Jian, JMC Ford Head of Manufacturing Engineering. “Partnering with Comau marks an important milestone in our journey toward manufacturing excellence. Comau’s innovative approach and commitment to quality provide us with a solid foundation, paving the way for future advancement and continued success.”
“Thanks to the strong collaboration between our engineering teams, Comau has helped JMC Ford meet its quality and precision requirements, and streamline overall capital expenditure,” said Jeff Yuan, Comau APAC Countries Cluster Leader. “The collaboration has also allowed us to achieve a high level of automation and flexibility while laying a solid foundation for future expansion.”
ABOUT COMAU
Comau is a worldwide leader in delivering sustainable advanced automation solutions. With 50 years of experience and a global presence, Comau is helping companies of all sizes in almost any industry leverage the benefits of automation. Backed by a continuous commitment to designing and developing innovative and easy to use technologies, its portfolio includes products and systems for vehicle manufacturing, with a strong presence in e-Mobility, as well as advanced robotics and digital solutions to address rapidly growing markets in industrial sectors.
The company’s offering also extends to project management and consultancy. Through the training activities organized by its Academy, Comau is committed to advancing the technical and managerial knowledge necessary to face the challenges related to automation and leverage the opportunities of a constantly changing marketplace. Headquartered in Turin, Italy, Comau has an international network of 7 innovation centers and 12 manufacturing plants that span 12 countries and employ 3,700 people. Together with its wide network of distributors and partners, the company is able to respond quickly to the needs of its customers, no matter where they are located throughout the world.
More Information
Related Story
Comau Presents Its New Cell Formation and Testing Technologies at The Battery Show 2024 as Part of Its Turnkey E-Mobility Solutions
Comau showcased its advanced, turn-key battery cell formation and testing technologies at The Battery Show Europe conference, booth number 9-F50, held 18-20 June. In bringing its highly efficient and scalable battery cell formation solutions to the commercial market, the global automation company is among the first European players to locally source this key aspect of the battery manufacturing process. And because Comau can support its customers at all stages of the process – from lab-based prototypes to giga-scale production – it is in a perfect position to help enhance productivity, reduce costs, and prioritize safety and sustainability.