Comau Deploys Innovative Dedicated Hybrid Transmission Assembly Lines For Hycet
December 22, 2023
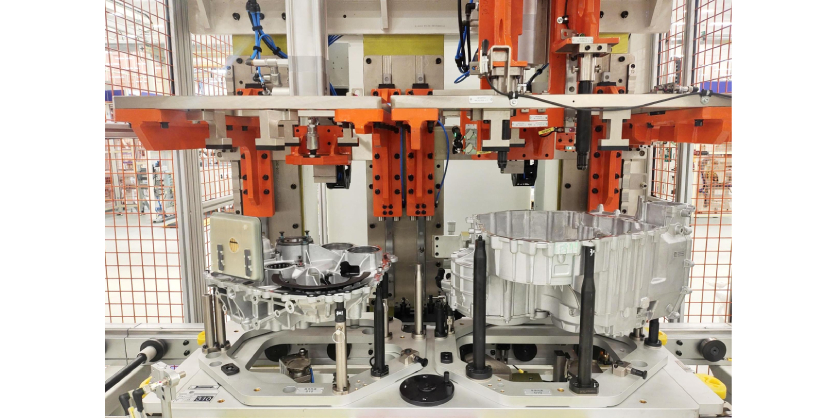
- Comau has developed and deployed a fully automated, high-volume manufacturing line to produce the L.E.M.O.N. hybrid transmission system
- The end-to-end solution grants an annual production capacity of 150,000 units per line with a cycle time of less than 2 minutes
- Delivering exceptional adaptability and efficiency, the scalable system is designed to help lower the production costs for future Dedicated Hybrid Transmission product upgrades
- The scalable production line can also be customized to meet evolving market needs
Comau has designed and deployed a high-volume, automated assembly line for HYCET, a wholly-owned subsidiary of Great Wall Motor and a leading manufacturer of DHT (Dedicated Hybrid Transmission) technology. The L.E.M.O.N. hybrid DHT is a next-generation transmission system that allows for the simultaneous use of gasoline engines and electric motors, enabling efficient power sharing between them. To meet the customer’s large-scale manufacturing targets, Comau’s end-to-end solution features a total of 12 robots across 6 lines to deliver an annual production capacity of 150,000 units per line with a cycle time of less than 2 minutes.
Within the scope of the project, Comau has wholly developed the necessary components, including e-motor assembly lines, gear and shaft assembly lines, main assembly lines, and the assembly test lines. The system also includes critical processes that grant full-process assembly from individual components to fully functional units. Furthermore, the high-speed production solution not only satisfies HYCET’s strict requirements in terms of manufacturing accuracy and product quality, it also ensures better adaptability and efficiency while lowering the production costs for future DHT product upgrades. Indeed, the Comau-designed production line can be easily customized to meet different market needs.
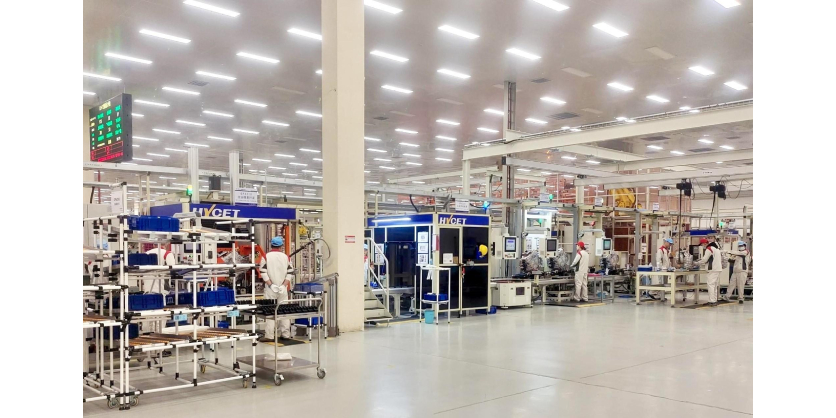
Comau has also used a process-integrated overall station design to guarantee stability and quality across the entire production line with an equipment availability rate of 90%. A MES (Manufacturing Execution System) allows HYCET to optimize the management and scheduling of the line. Finally, key process parameters, such as force and displacement, are constantly monitored to ensure quality control throughout the entire production process and support subsequent data traceability.
“HYCET’s DHT technology represents cutting-edge innovation in the hybrid vehicle sector and delivers outstanding performance for Great Wall Motor’s DHT system. As our technology partner, Comau’s design and engineering capabilities confirm their exceptional position in this field,” said Wu Hongchao, Vice President of HYCET Technology Co., Ltd. “Throughout the project implementation phase, Comau adhered to the project schedule despite the recurring impacts of the pandemic, and ensured consistent manufacturing quality. This stability is critical for our production goals, allowing us to meet market demands and maintain optimal manufacturing efficiency.”
Wu Hongchao, Vice President of HYCET Technology Co., Ltd
“This project was an incredible opportunity to work with a pioneering company in hybrid transmission technology development,” explained Jeff Yuan, Comau Head of Countries Cluster APAC. “By prioritizing flexibility, efficiency, and absolute quality within the manufacturing philosophy, Comau has designed a 100% error-proof production process that allows HYCET to enhance efficiency, reduce costs, and meet its large-scale manufacturing goals. Our competencies in e-Mobility are backed by a longstanding experience in traditional engine and powertrain systems, helping position Comau as a leader in Electric Vehicle solutions at a global level.”
Jeff Yuan, Comau Head of Countries Cluster APAC
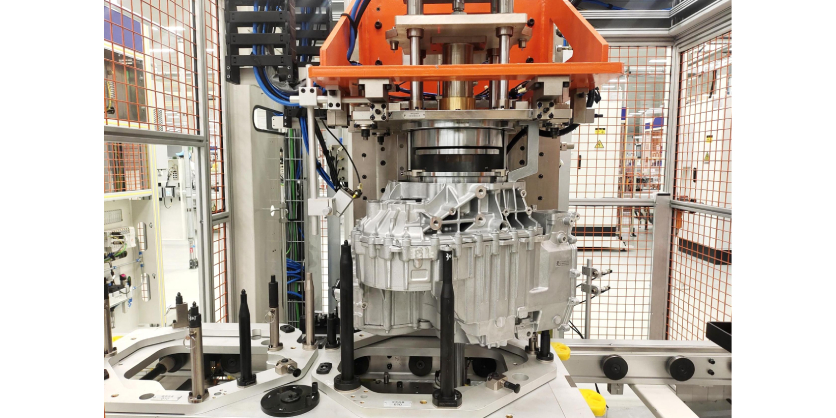
Comau invests in the development of e-drive technologies and consistently broadens its technology portfolio to meet the evolving demands of e-mobility applications. In addition to excelling in the design, manufacturing, and integration of flexible, modular, reconfigurable, and scalable automation solutions, the company specializes in stator assembly systems, rotor assembly systems, e-Drive assembly systems, electric control assembly systems, and electric housing machining solutions.
Comau is also developing automated manufacturing systems for battery cells, modules and complete packs (with any cell format), Comau offers a range of systems for different stages of the production process including battery cell forming technologies. With a 360° portfolio of products, processes and technologies, Comau can handle everything from prototyping and pre-production to mass manufacturing, and all the way to end-of-life battery recycling.
By combining pioneering competencies in automation and electrification, Comau is fully able to help its customers, anywhere in the world, leverage technology advances and process developments, in addition to the enabling digitalization tools that support them. With a keen focus on the large-scale electrification of the automotive market, Comau fully supports its customers in developing market-leading new energy vehicles, offering advanced solutions for the future.
More Information
Related Product
Comau And LiNa Energy Develop Automated Manufacturing For Solid-State Sodium Batteries
Comau has joined forces with LiNa to design an innovative and scalable manufacturing solution for solid-state sodium-metal-chloride battery cells. Through simultaneous engineering, the team has finalized a concept design, allowing LiNa, a leader in low cost solid-state sodium battery technologies, to automate their battery production process. The companies intend to validate the sustainable, safe, and efficient oxygen-free dry box environment as a step towards larger-scale manufacturing.