Comau and Leonardo Leverage Cognitive Robotics to Deliver Advanced Automated Inspection for Mission-Critical Aeronautical Structures
February 29, 2024
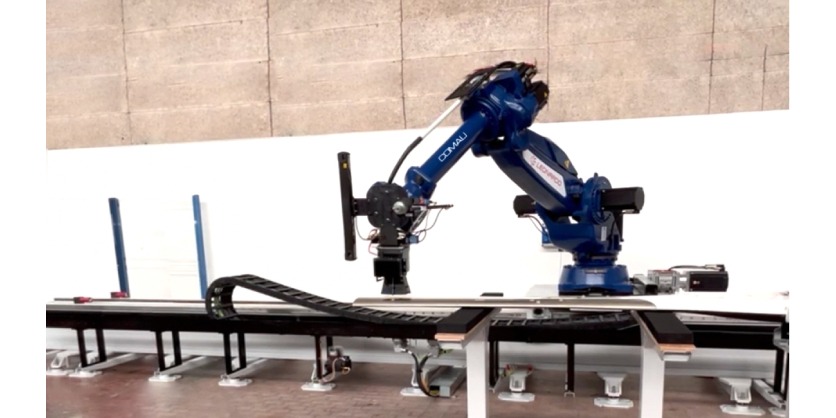
Comau and Leonardo Leverage Cognitive Robotics to Deliver Advanced Automated Inspection for Mission-Critical Aeronautical Structures
- The companies have jointly developed and are testing a powerful, self-adaptive robotic solution to autonomously inspect helicopter blades measuring up to 7 meters
- The cutting-edge solution ensures higher quality and greater flexibility without sacrificing precision or repeatability
- Comau’s intelligent robot perceives and sees its surroundings, calculates its decision making and intuitively optimizes the end-to-end inspection processes
The increasing push for faster processes, better control and higher quality in the aerospace industry necessitates a new generation of advanced automation designed to automate complex processes that until a short time ago could only be done manually. When it comes to testing critical structures such as helicopter blades, for example, the potential benefits of automation increase exponentially, as robotic inspection grants accuracy as well as efficiency. They also ensure standardization of and full compliance with the testing process by objectively completing each assigned task.
To address this need, Comau and Leonardo are working together to develop and test a powerful, self-adaptive robotic solution to autonomously inspect helicopter blades measuring up to 7 meters. The smart inspection solution has been developed as a joint pilot project and was tested on-site in Anagni, Italy, over the past year. The system may now move to another site to deliver enhanced capabilities for MRO (Maintenance, Repair and Overhaul) services.
Leveraging a combination of cognitive robotics, advanced vision systems and artificial intelligence, the solution autonomously performs tapping tests and multispectral surface inspection along the non-linear blade, to measure and verify the structural integrity with a granularity exceeding thousands of points. More importantly, robotized inspection ensures 100% accuracy within the self-adaptive process and allows operators to upskill their positions while enjoying better safety and well-being compared to the initial repetitive and labor-intensive process. Furthermore, the move from manual to robotic automation will let Leonardo leverage the full benefits of process engineering compared to a manual operation in which experience is often passed between technicians in a non-standard way.
Looking at the technical collaboration in more detail, each of the companies has shared specific competencies to optimize the end-to-end inspection process. These include intelligent algorithms and advanced path planning that allow the robot to see and respond to its surroundings, as well as a comprehensive data acquisition and processing infrastructure that facilitates optimized sound and image recognition. As the blades are mechanically stimulated by the smart robot, the sound response is both recorded and photographed using a multi spectral camera in order to detect hidden and superficial defects.
Another powerful feature of the system is that it automatically senses the environment. It first localizes the blade, which has been placed on its supports by the operator, detects any obstacles and then calculates both cycle time optimization and collision-free path planning. All this technical complexity is hidden behind a simple and effective user interface based on low code programming. This allows the operator to program the robot using simple, human commands: look for the blade, find the position and execute the action required. In doing so, the solution shifts the operator’s role from executing repetitive and labor-intensive tapping tasks to leveraging their experience when programming the robot to run the now standardized process.
Such intelligent automation helps reduce the seeming complexity of processes and optimize their outcome by enabling the robot to perceive and see its surroundings, automate its decision making and intuitively optimize the inspection processes. This grants greater flexibility without sacrificing precision or repeatability.
“Comau’s commitment to the design and development of cutting-edge technologies and solutions for elaborate processes allows us to extend the benefits of advanced automation to mission-critical sectors such as aerospace,” explained Nicole Clement, Chief of Comau Advanced Automation Solutions Business Unit. “The collaboration with Leonardo gives us the opportunity to extend our innovation reach by developing a smarter, data-driven inspection system that provides an objective assessment of key structural elements within a standardized, automated and highly-accurate process.”
“This technology demonstration project fits well in Leonardo’s strategy to transform industrial processes through digitization,” said Mattia Cavanna, Head of Technology & Innovation at Leonardo Helicopters. “It also aligns perfectly with our steadfast commitment to enhanced technical support, which in turn yields concrete benefits in terms of safety and quality”.
More Information
Related Story
Comau Will Significantly Accelerate the Testing and Verification of Automotive and Stationary Batteries
Comau has committed to developing the digitalization strategy for a next-generation battery systems testing platform as part of a multi-country, multidisciplinary consortium in support of the FASTEST project. Under the scope of the project, Comau will leverage its longstanding expertise in digitalization, process simulation and electrification to significantly accelerate the testing and verification of automotive and stationary batteries. This is expected to reduce the overall time and costs of battery production by at least 20% in addition to decreasing the number of physical experiments and the subsequent reduction in materials costs.