CM3C.. (Medium Inertia) Synchronous Servomotors
October 2, 2024
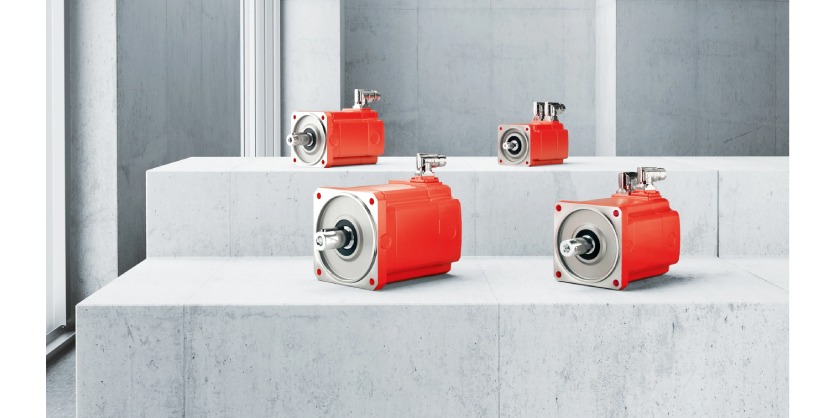
The dynamic, high-precision solution for heavy external load
The lowest possible ratio of load moment of inertia to motor moment of inertia is key for transporting heavy loads from A to B at high speed and with great precision. That’s why CM3C.. series servomotors benefit from increased inertia. These servomotors are therefore particularly suited to all automation, handling and transport applications with a correspondingly high load moment of inertia. With their four sizes – 63, 71, 80 and 100 – they can cover standstill torques from 2.7 to 40 Nm.
The servomotors are also exceptionally small and have a space-saving design. What’s more, the option of mounting the motor directly on the gear units (direct motor mounting) eliminates the need for adapters and couplings. The multi-stage surface protection concept and smooth surfaces (hygiene-friendly design) make the medium-inertia servomotors particularly robust and dirt repellent. In addition, the rotors, which are equipped with permanent magnets, deliver a very high level of efficiency, thus ensuring exceptionally energy-efficient operation.
Flexibility and reliability are also key features of the brakes that are available for the servomotors. Alongside the 24 V holding brake typically used for servomotors, users also have the option of a brake with increased working capacity. Thanks to this equipment, the synchronous motors can even handle applications where emergency braking is needed. Requirements of this kind are typical in machine automation, handling gantries and travel unit drives.
Thanks to SEW-Eurodrive’s modular system, the highly flexible CM3C.. series servomotors can be adapted to meet specific needs. At the same time, single-cable technology means they can be installed quickly and integrated intelligently into state-of-the-art Industry 4.0 concepts.
Facts about CM3C.. series servomotors
Properties standard version
- Four sizes – 63, 71, 80 and 100 – in three lengths – S, M and L
- Compact and powerful thanks to cutting-edge magnet and winding technology
- RH1M resolver
- Adjustable right-angle flange sockets
- PK temperature sensor (PT1000)
- IP65 degree of protection
- Long bearing service life
- High permitted overhung loads
- Stand-alone servomotor or direct gear unit mounting
- Virtually no perceptible cogging
- Continuous standstill torques (M0) from 2.7 to 40 Nm
- Maximum torques (Mpk) of up to 120 Nm
- Up to four speed classes: 2000 min-1, 3000 min-1, 4500 min-1and 6000 min-1
- Condition monitoring and extensive options for fault diagnostics with the MOVILINK® DDI digital motor interface
- Optimized operation on MOVIDRIVE® inverters from the MOVI‑C® modular automation system
Available options
- Forced cooling fan for enhanced thermal motor capacity utilization
- Terminal box
- Safety-rated design with brake and encoder
- Explosion-protected design: ATEX and IECEx (in preparation)
- All standard approvals (UL, CSA, EAC, UkrSEPRO, CEL and CMIM)
- Optional encoder systems:
- HIPERFACE® encoder with electronic nameplate
- Two-cable technology
- Scalable (128/1024 sin/cos)
- Single-turn and multi-turn
- Encoderless design with hybrid plug connector:
- Single-cable technology
- MOVILINK® DDI digital encoder interface:
- Single-cable technology
- Scalable (12 bit / 18 bit)
- Single-turn and multi-turn
- Compatible non-SEW encoder systems:
- DRIVE‑CLiQ from Siemens for operation using standard Siemens Sinumerik and Sinamics controllers
- EnDat2.2 from HEIDENHAIN
- HIPERFACE DSL from SICK Stegmann
Digital motor and data integration
Digital motor and data integration is possible thanks to the MOVILINK® DDI digital interface. It’s all based on single-cable technology. In fact, motors and inverters from the MOVI‑C® modular automation system require just one hybrid cable for power supply and data transfer. The hybrid cable supplies the motor with power and MOVILINK® DDI, a digital encoder, transfers all necessary power, brake and diagnostic data between inverter and motor. This saves you both time and money during installation and startup.
The digital motor and data integration works with synchronous motors, asynchronous motors and decentralized drive technology.
Functional safety overview
- You can also request motors from the CM3C.. series with a safety brake and safety encoder. These can be integrated into the servomotor individually or in combination.
- The following safety functions are possible with the safety brake:
- SBA (Safe Brake Actuation)
- SBH (Safe Brake Hold)
- Using safety encoders, safety functions relating to rotational speed, direction of rotation, standstill and relative position are possible, such as SS1, SS2, SOS, SLA, SLS, SDI and SLI to IEC 61800‑5-2.
Ambient conditions
- Degree of protection:
- Standard IP65 according to EN 60529
- Optional IP66
- Ambient temperature:
- -20 °C to +40 °C (Standard temperature range)
- -20 °C to +60 °C (With derating for increased ambient temperature)
- -40 °C to +10 °C (with measures for low temperature range)
- Sustainability and excellent energy-saving potential:
- Complies with efficiency class up to IE5 based on IEC TS 60034-30-2
Certifications/conformity
- CE (European Economic Area)
- CEL (China)
- CMIM (Morocco)
- UL (USA and Canada)
- EAC (Customs Union of Russia, Kazakhstan and Belarus)
- UKCA (United Kingdom)
- UA.TR. (Ukraine)
Ready for use in your application: CM3C.. series servomotors
Recommended for their compact design
Save time and money
They are impressively compact.
The electromechanical components and the drive electronics both benefit from an extremely compact design.
Further complementary features such as direct motor mounting on the gear unit, high torque density and less installation work between hardware components thanks to single-cable technology mean this combination is highly recommended if your focus is on saving time and money.
Recommended for energy efficiency
Flexible and energy efficient
during planning, startup and production.
The new CM3C.. series of synchronous motors achieves energy efficiency class IE5 – an advantage over asynchronous motors.
Only when combined with further motor features such as direct mounting on any gear unit, wide-ranging options and accessories, hygienic design credentials and a cable length of 200 m between motor and inverter, however, does this create a truly flexible and energy-efficient solution.
Recommended for safety
Functional safety and reliable availability
that extends worldwide.
You can also request the motors from the CM3C.. series with a safety brake and safety encoder – to make protection against personal injury as easy as possible in your system, for example. Used individually or in combination, the functionally safe options contribute to a safe concept.
The modular system also means you are dealing with just one supplier, who delivers worldwide and ensures both short delivery times and long-term product availability.
Related Story
SEW-Eurodrive Is Your Complete Source for Motion Control
SEW-Eurodrive specializes in custom, scalable drive solutions that focus on meeting the needs of customers today – and into the future. SEW-Eurodrive’s decentralized variable frequency drives combine power, communications, integration, and support all-in-one, saving you time and money. They have this and so much more to offer.
SEW-Eurodrive has set the trends and standards in drive engineering for years. Their universal concept of gearmotors, control systems, software, service, and extensive accessories are the cornerstone of many industrial motion systems. Dominique Salvail, Product Specialist, Factory Automation Solutions at SEW-Eurodrive, discusses how they have everything you need for your motion control application, and highlights how their decentralized VFDs can save you time and money.