One-Step Production with ANCA’s Automated Blanket Grinding Solution
Save time with continuous production from bar stock to finished too
August 21, 2023
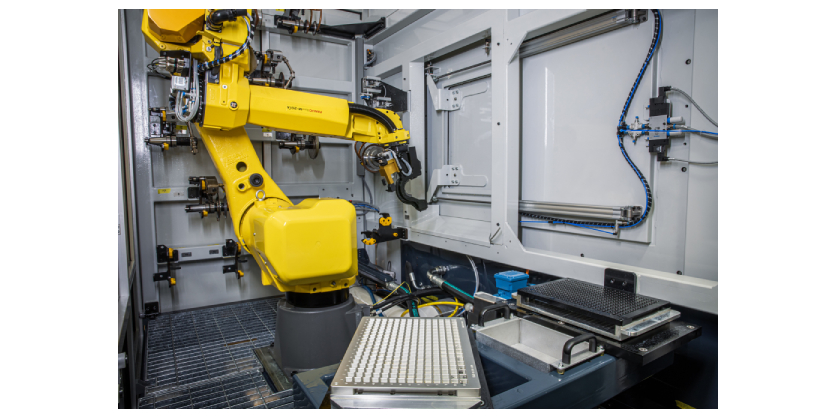
By Kaine Mulder, ANCA Product Manager
Recent events have applied extreme pressure to supply chains, with labor and raw material shortages, freight delays and increased energy costs. The need to further adapt has become significantly more important, particularly as these pressures are exacerbated by demand, driven by expectation in our “instantaneous” global culture.
ANCA continually strives to work with its customers to adapt and grow along with these market changes and pressures. One such method assisting customers to adapt is blanket grinding, enabled by ANCA’s unique robot cells offered on each of our platforms.
What is blanket grinding?
ANCA’s blanket grinding approach allows for continuous and complete tool production from longer bar stock to finished product using an automated solution, saving time in eliminating extra processes or handling.
Utilizing ANCA’s machine platforms with a robot cell, blanket grinding offers flexibility across a range of tool sizes and applications. Blanket grinding allows for full automation of tools of similar geometries, by consolidating all tool grinding processes into one single machine. A batch of complete finished tools can be produced without interruption directly from lengths of ground bar stock with no operator intervention. Ultimately this gives you the flexibility to respond to customer demands in a dynamic and agile manner. All you need to do is simply load a pallet of ground bar material into the cell, and the machine will take care of the rest.
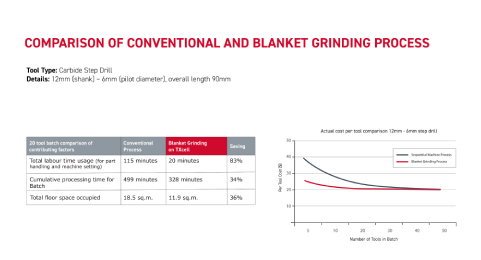
Blanket grinding is great for:
- Small batch and bespoke solutions
- Quick turnaround production
- Product development and R&D
- Accuracy and consistency over batch
- Automation and “lights out” operation
Beginning with the full 330mm bar stock material loading into the collet; the blank and tool geometry is ground, including any features (such as rear chamfer, for example), before the finished tool is cut off. The tool is then removed by the robot and loaded into the finished pallet. This program continues along the remaining bar stock until all useful raw material is consumed. To complete the automation process, waste is handled by the cell, before new bar stock is loaded into the collet.
ANCA’s TX machine platform is the solution for blanket grinding
ANCA’s machine platforms with the addition of a robot cell, can be utilized to implement the blanket grinding process. Tool size and application will determine which machine is right for you.
The two main features offered by the TX, beneficial in performing the blanket grinding function are the large working envelope and the high torque spindle. These attributes not only allow work on longer bar lengths, but also enable production of a larger range of tool sizes and geometries without limitation, including tools which require a high material removal.
The TX platform also fits any of ANCA’s robot cell solutions, including RoboMate, and the dedicated TXcell offering, which offers large format cell automation, many standard options and the flexibility for automated custom solution.
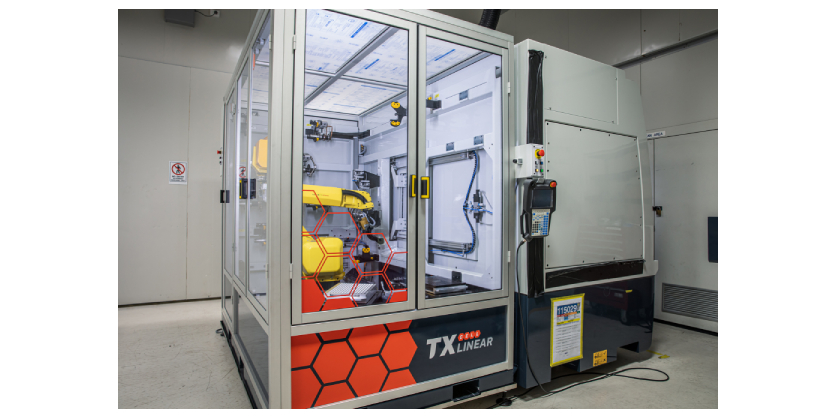
The nimble RoboMate cell is offered on both TX and MX platforms and offers customers a low barrier to entry for blanket grinding and production automation.
How blanket grinding can help you
Customers are increasingly demanding products that are more unique and with higher complexity – but more importantly, with immediate response and shorter delivery time; when meeting these expectations, costs take a back seat, while focus is on delivery.
Using ANCA’s robot automation solutions in blanket grinding enables you to realize these demands with minimal disruption to existing production lines, less planning, reduced manual handling and increased utilization and efficiencies. These benefits can compound to deliver an overall value proposition and increased return per tool.
Blanket grinding may also offer a reduction in floor space by removing separate machines and consolidating processes into a single footprint to produce the same tool. The process consolidation allows changes in parts and features to be easily handled. For example, grinding of shank features (Weldon flats or coolant slots) and the handling of very small parts can be made simpler by adding many features in a single setup.
Benefit from blanket grinding
Become more agile
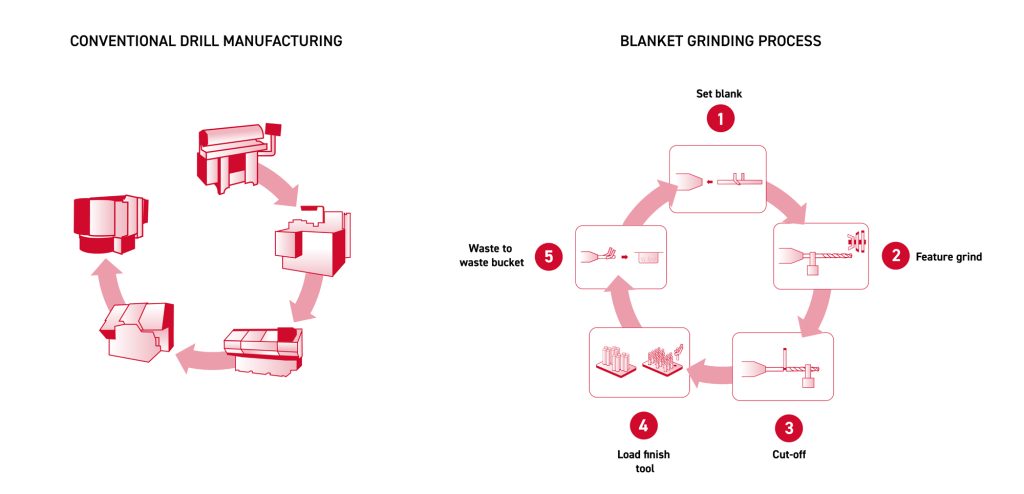
You can provide a quick response to customer requests without the need for re-tooling or disruption to high volume production lines, while also guaranteeing highest quality across the batch.
- Eliminates need for re-tooling
- Reduced setup times
- Quick response without disruption, allowing further utilization of more specialized machinery
- Improved quality
- Ability to easily add special shank features in single setup, e.g. coolant slots, Weldon flats, and more
Reduce costs
Applying blanket grinding will go a long way to improving cost recovery, through increased utilization and efficiencies as well as removal of manual labor and setup times. There is also a benefit in reduced footprint through process consolidation into a single machine.
Blanket grinding can reduce costs through:
- Machine utilization
- Reduced stock waiting in process
- Minimal manual handling
- Reduced tooling and setup; single machine setup, not multiple stations
- No process interruption
Reduce lead times
- Eliminate setup times
- Eliminate tooling across multiple machines
- Variations of the similar profile/geometry can be produced uninterrupted
- Enables automation and “lights out” production
More Information
Amanda Bakun, Marketing & Communications Manager – Americas, 248-497-1168 amanda.bakun@anca.com
Related Story
Edmund Boland Appointed as General Manager of ANCA CNC Machines
ANCA is proud to announce the appointment of Edmund Boland as the new General Manager of ANCA CNC Machines. Edmund is the son of ANCA co-founder Pat Boland and brings an impressive 15-year tenure at ANCA. Pat Boland, ANCA co-founder said, “When Pat McCluskey and I founded ANCA, our primary goal was to design the best technology that solves real customer problems. I am proud that my son has joined this mission and has accepted this important leadership role in the business to continue fostering a culture of innovation.”