A Robust Gripper for a Lock System
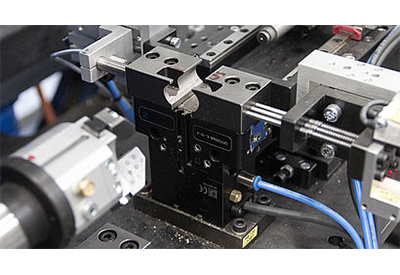
December 24, 2020
Quite inconspicuously at the end of a street the company AUMAT Maschinenbau GmbH is located in an industrial area at the outskirts of Solingen. But the company has it all! Since 1970, the name AUMAT has stood for high-quality broaching and special machines. Customers come from the automotive industry and the cylinder lock industry. The many patents of the company, which have been implemented there, prove that resourceful minds also work there. Whether you want to profit from the highly developed delivery programme of sophisticated machines or are looking for a special and flexible solution for your complex task: AUMAT promises to give the customer very competent advice and to supply him with the appropriate technology. This was also the case with the Iseo company – a lock system manufacturer from Gera – which asked AUMAT for a suitable solution for the machining and testing of its newly developed lock cores.
After several months of development, AUMAT succeeded in automating this complete process with a machining centre developed especially for the customer. The approximately 20 square metre plant in Solingen, which is currently about to be delivered to Iseo, consists of a total of 10 variable stations in which the lock core is drilled, reamed, deburred, filled with pins and pressed. A conveyor belt and a six-axis robot from Kawasaki Robotics are used to transport the cores.
Test and measuring station forms the centre of the plant
The heart and highlight of the facility is the testing and measuring station for the lock cores with the aforementioned Kawaski robot. Right at the very beginning of the project, the AUMAT development team headed by Dipl. Ing. Achim Ihlefeld was still thinking about solving the complex testing process by means of a clamping device for the process-safe holding of the lock cores and micro probes for tolerance evaluation. However, corresponding research led to a completely new idea and possibility, which should simplify the entire process extremely: A special gripper could perform the two test steps as a convenient all-in-one solution. This would not only provide a more compact solution, but also fewer sources of interference.
In the search for a gripper which now had exactly these required characteristics, AUMAT found what they were looking for in the Zimmer Group. The technology company from Rheinau has been developing handling solutions and gripping systems for a wide range of industries for 40 years. The Zimmer Group was able to convince the Solingen-based developers with its GPP5000IL hybrid gripper. This gripper has a pneumatic drive combined with modern IO-Link technology. Valve technology, sensor technology, status display, pressure and temperature monitoring are integrated in the gripper. In addition, it has a part detection in the range of +/- 0.05 mm with a freely teachable tolerance range. This was a decisive factor for the developers at AUMAT, since the lock cores were to be checked for dimensional accuracy (diameter, position and length) at the test station. Due to the large number of different types of lock cores, it was also helpful that 32 workpiece data records can be programmed into the GPP5000IL gripper. In addition, an unlimited number of recipes can of course be stored in the PLC, which can be continuously called up by the gripper if required. A pleasant side-effect for AUMAT – which places great emphasis on high and long-lasting quality – is that the Zimmer gripper is guaranteed maintenance-free for up to 30 million cycles.
Automated machining increases profitability
At the inspection station, the lock cores fed from the belt into boxes are fed by the robot into the GPP5000IL hybrid gripper and checked for the correct diameter. The core is then aligned for further processing and, by means of spring-loaded metal pins which are scanned by laser light sensors, it is checked whether the holes are present and in the right position. The workpiece is then measured by a distance measuring system and inspected for the presence of a coupling bore. With this detailed inspection, the lock core is released for further production or is noted as NOK (not in order) and sorted out.
The automated solution will increase Iseo’s profitability enormously, ensures process reliability in the machining and testing of lock systems and frees the employees from monotonous work. This increases both the company’s profitability and the health of the employees. The automated and optimum provision of the lock core in the correct sequence means that work steps can be saved.
Some hurdles had to be overcome
The challenges for the AUMAT developers were great. For example, the cycle time of the process was set very high by the customer at 11 seconds. Due to the variety of products, the machine had to be designed extremely variable, which made it much more complex. As the space available at the customer’s premises is also limited, a very compact design was required. Here, the Zimmer Group gripper scored points with the connection of the gripper via only one single pneumatic line and IO-Link cable. Mr. Müller, project manager at AUMAT, was extremely satisfied with the cooperation with the Zimmer Group: We had been looking for a solution to a problem and the Zimmer company was able to provide an answer very quickly. Encouraged by this positive experience, especially in the field of electric or hybrid grippers, we at AUMAT are now thinking about using them more in the future,” said Mr. Müller.