What Goes Into Building an IO-Link System? Omron Explains
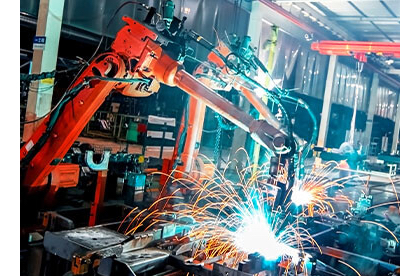
June 27, 2022
One of the easiest ways for manufacturers to transform their operations with IIoT capability is to use IO-Link. This internationally accepted platform allows sensors to go beyond a simple ON/OFF reading and communication details about default detection, condition monitoring, and component indemnification, and more throughout the system.
Thanks to IO-Link, manufacturers can shorten commissioning time, minimize the impact of downtime, and boost their production availability, so it’s no surprise that many companies are curious about what technologies they need to acquire to get started.
Omron takes a look at what an makes an IO-Link solution.
First things first: IO-Link-enabled devices
Devices that support IO-Link can be sensors, actuators, or something that combines both elements. (Sensors gather data from their surroundings and turn it into an electrical signal, whereas actuators take an electrical signal and respond by performing an action on their surroundings.)
Most sensors and actuators sold on the market today are designed to be IO-Link-enabled. For example, Omron’s E2EW Series weld field immune metal-faced proximity sensors use IO-Link to communicate any real-time condition changes that may indicate weld slag buildup.
An IO-Link master connects sensors and actuators to the automation system
To manage the data coming in from IO-Link devices, you need an IO-Link master. Essentially, this device takes care of all the push and pull of information to and from your sensors. From there, everything else is standard to whatever network you’re using. For example, if you’re using EtherNet/IP, then you would communicate back through EtherNet/IP.
IO-Link masters process both digital signals and analog values, allowing them to integrate easily into systems that are already in place. You can install them either in the control cabinet or in the field as remote I/O.
Last but not least: The IODD file
To configure your IO-Link sensors and actuators, you need to have an I/O Device Description (IODD) file containing information about those devices. This information tells you what bits you can read, what bits you can write to, and what pieces of information are considered process data (data that refreshes every 1.2 milliseconds).
An IODD file is always available for any IO-Link-capable device that’s put out on the market. If you’re following IO-Link, you’re following an IEC standard (IEC 61131-9), so you must conform to the standard to use the IO-Link branding.
What about the cabling?
Fortunately, no special cables or connectors are necessary for an IO-Link solution. For many other sensor-level communications protocols that predated IO-Link, you had to have special cabling, but the IO-Link consortium chose to standardize on the cabling — and more specifically, on 3-, 4-, or 5-pin cordsets.
This means that any cordset that you would normally use to plug into a sensor that classifies as 3-, 4-, or 5- pin will work for your IO-Link communication needs.
Want to browse Omron’s IO-Link portfolio? Click here