Upgrading Legacy Automation: Implications, Challenges, and Best Practices
May 1, 2024
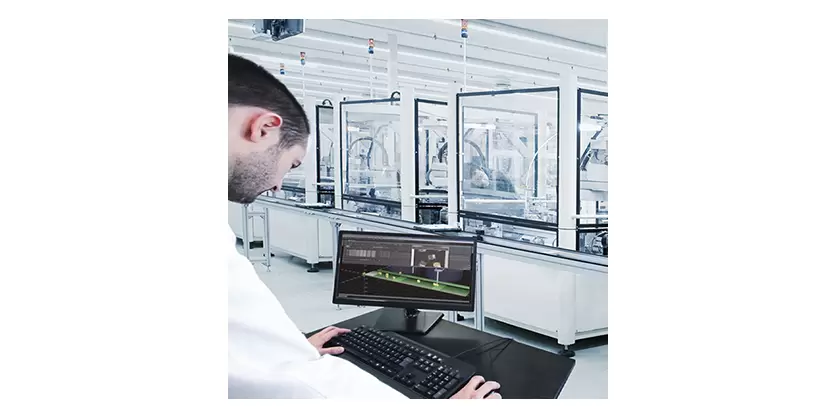
On today’s factory floor, upgrading legacy automation equipment is often a taboo subject. “Why fix what isn’t broken”? “What fix it unit it is broken”? “Why borrow trouble”? There are many quick rebuttals to team members who have faced a close call on the production floor around legacy equipment.
Legacy automation, characterized by technology in the later stages of its useful life, and where useful life is defined by receiving a disproportionately large amount of utility compared to the resources consumed, can limit efficiency, increase downtime, and jeopardize long-term factory vitality. As new automation technologies continue to emerge and interconnect at an exponential rate, failing to integrate these technologies can widen the gap between the competitive and the obsolete.
In this blog post, Ormon will explore the implications, challenges, and best practices associated with upgrading legacy automation from the factory floor perspective.
Implications of Upgrading Legacy Systems
Upgrading legacy automation brings both opportunities and challenges. Opportunities which can usher in a future of efficiency gains. Along with challenges which if not overcome could jeopardize production metrics today. Legacy equipment can cap machine performance, increase troubleshooting time, raise maintenance costs, and invite undue cyber vulnerabilities.
Therefore, it is crucial for manufacturers to address these implications and leverage new automation technologies to enhance efficiency and productivity. Allowing them to stay competitive, while also preserving flexibility to incorporate emerging technologies quicker [1].
Challenges of Upgrading Legacy Systems
Upgrading legacy automation can be daunting. Projects are typically capital and time intensive. They can showcase any past decisions which were made to address problems long forgotten. Three of the largest challenges which are common on the factory floor include:
Upgrade becoming replacements:
Motion upgrades require intimate knowledge of the application and the machine. Knowledge which may be lost because of obsolete documentation or code without notes. As an example, the perception of a motion upgrade to increase throughput may appear to be a quick project but commonly results in a completely new machine.
Technical debt masking as complexity
Commonly an abundance of networks, confusing code, as well as missing wiring diagrams makes paying down technical debt a larger capital project. Where technical debt is friction in the factory which resists efficiency gains by using the hidden inertia of status quo. As an example, tackling complex wiring carries risk. One short can stall commissioning by days as replacement components are sought.
Culture pressured by short term metrics
When success is only measured at the end of a shift not at the end of the year, teams require confidence that an upgrade will be a significant performance improvement today. Improvement to the metrics which maintenance and production teams are measured on.
Best Practices in Upgrading Legacy Systems
While each legacy system is unique, requiring a dedicated team to focus on each challenge can be beneficial to ensure the end goal is achieved for all stakeholders.
Here are three best practices could be useful in the next upgrade project:
Upgrade or replacement, the machine is a new machine
Ensuring safe operation should stay at the core of every project. Before commissioning the first production run, a safety audit should be conducted by a certified third party or internal team to ensure operator safety. In addition to operator safety audits, cyber risk assessment should be completed. Thus, ensuring that good cyber hygiene is maintained [2].
Upgrade over time and start small:
Upgrading a section of the plant floor at a time minimizes the risk to overall production by reducing the vulnerability of plant wide downtime through proper production planning. Starting small also creates an increased reservoir of spare parts for consumption elsewhere in the plant. This extends the transition period allowing for more time to train maintenance and production teams.
Plan for upgrades from day one:
Build upgrades into the natural product lifecycle of the machine. Having the upgrade conversation illuminates the future of a production facility. While being future oriented may yield more questions than answers, it is a necessary step to ensure upgrades do not become an unforeseen surprise. To aid in this selection process, automation partners who manufacture their products may have the edge, as these partners can showcase the future with a more tangible strategy.
The Importance of Talking Upgrades Today
Starting a project to upgrade automation, which is at the heart of the factory, is resource intensive. Capital requests, plant wide training, and new production planning all take valuable resources. Delaying the upgrade conversation, while allowing the plant to function today, can greatly increase hidden production risks. Hidden risks which may choose to no longer hide at the least opportune time.
Choosing the right partner to begin the upgrade conversation can de-risk an upgrade and put production teams back in control of their production by switching the narrative from reactive to proactive.
Notes
[1] Azhar, A. (2021). The Exponential Age: how accelerating technology is transforming business, politics, and society. Diversion Books.
[2] Roose, K. (2021). Futureproof. Random House.
More Information
Related Story
How Can Omron’s Certified System Integrator Partners Elevate Your Automation Solutions?
With so many companies offering system integrator services in the automation industry, finding the right partner can be a daunting task. At Omron, they understand the importance of seamless integration, efficient automation, and adaptable manufacturing process. That is why they introduced the Omron Certified Systems Integrator Program – a platform designed to elevate their partners’ proficiency in Omron technology. Their goal is to empower their partners to enhance productivity and cost-effectiveness for mutual customers.