Top Five Industrial Applications of Cobots by Universal Robots
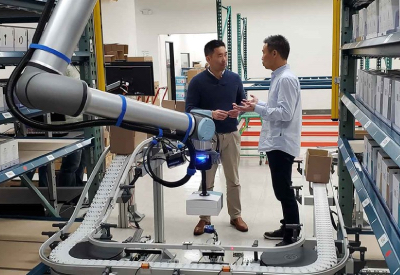
May 11, 2022
The industrial applications of cobots are vast, and these smart machines have capabilities that virtually every manufacturing plant or production line can make use of. A cobot arm handles dull, dirty or dangerous jobs on behalf of their human colleagues and minimizes downtime by boosting round-the clock-capacity, if that is what the business needs. Cobots’ capabilities are incredibly varied, and their tasks can be tailored to your business’s needs, even multiple times per day.
Cobots can be used to introduce industrial automation to lots of different areas of a business. Each machine has a wide range of applications, from detailed work to palletizing, but different models are better suited to certain types of tasks. A tabletop model such as the UR3e will suit a business that is looking to automate tasks that aren’t load-bearing, while a larger cobot arm will be able to pull its weight with heavier jobs.
For a small business, the fact that cobots have many uses is one of their biggest assets. They can be reprogrammed to fill gaps that emerge in virtually any area of the business, from palletizing to production line, in very little time. And one core component is responsible for cobots’ versatility: their end effectors.
End effectors, also known as end of arm tooling (EOAT), are a vital component of all cobots. They attach to the end of the robotic arm and allow it to carry out specific tasks, which range from laborious tasks such as picking and packing to technical jobs like welding and sanding. One cobot could handle upwards of a dozen tasks over the course of a working week, depending on a business’s needs.
Here are some of the most common industrial applications of cobots, and why some companies are choosing them over industrial robots.
Pick and Place
Pick and place cobots are an important part of material handling. They quickly and accurately secure components of surface mount devices (SMDs) onto printed circuit boards (PCBs). Using a specific script, a cobot can be programmed to select the right parts, reject unsatisfactory pieces, and solder them onto a PCB with greater speed and accuracy than a person. For electronics manufacturers that are aiming to boost their capacity while keeping production costs low, a pick and place cobot could be ideal.
Our client Beyerdynamic uses collaborative robots to produce its loudspeaker membranes – a key part of its audio equipment. Its challenge was finding a way to significantly boost productivity without compromising the quality of the products or increasing its human production resources. The business had found that, during one key part of the process, there were significant fluctuations in the quality of the membranes of the loudspeakers.
Beyerdynamic has split the process into two parts, which are handled by two separate cobots. First, a ur5, equipped with an integrated Robotiq wrist camera and a Robotiq two-finger gripper places a welded headphone loudspeaker on a rotary motor. Next, a ur3 with an integrated spray gun coats the member with a dispersion membrane. For Beyerdynamic, these two machines have increased productivity by 50% and improved the quality of the product at the same time.
Peter Härtel, Head of Strategic Operations and Quality at the firm, explained how simple the process has been.
“Thanks to the intuitive control interface, our employees can quickly learn to operate the robots themselves. Thanks to this Plug&Play integration between the UR robot arm and the Robotiq supplies, our pilot project could be implemented in no time at all.”
Assembly
Some tasks on an assembly line require skills, attention to detail and the careful eye of a human. Others are incredibly monotonous, less efficient in human hands, or come with a higher risk of injury to workers. Using cobots on an assembly line can increase the pace of production, protect workers from harm and ensure the irreplaceable people in your business are being utilized in the most effective way.
In the US alone, it’s predicted there will be a manufacturing skills gap leading to 2.1 million unfilled jobs by 2030, costing the economy up to $1 trillion per year. Freeing up skilled workers to tackle tasks that require their expertise and experience by installing cobots for roles that recruitment efforts fail to cover could be one way to close this gap.
Machine Tending
It is not just simple material handling tasks that cobots can carry out. They also have the ability to handle a wide range of machine tending jobs, including:
- •Computer numerical control (CNC)
- •Injection molding
- •Press brakes
- •Stamping presses
- •Manually loading and unloading parts or components
There are many tasks that are a poor use of an operative’s time, such as those that require them to simply hang around and switch out a part every minute or so. By getting your cobot to handle these jobs, your people can move to more delicate or thoughtful work that genuinely utilizes their human touches or nuanced intelligence.
Welding
Currently, over 70% of cobot applications fall into the first three categories. But as cobot technology becomes more sophisticated and sensitive, it is being used for tasks that require more attention to detail. Cobot welding has a number of benefits to workers and companies. It ensures complete consistency on simple welding tasks, which would be difficult for a human employee to maintain for hours on end, ultimately reducing wasted materials.
While cobots are capable of Arc, TIG, laser, MIG, ultrasonic, plasma and spot welding, they will not be suited to every welding task. As such, allowing cobots to handle welding does not mean that skilled welders will lose their jobs. In fact, it can lead to greater employee satisfaction as those workers will get to tackle more challenging lower-volume projects that require their expertise.
Palletizing
Palletizing is a part of material handling that refers to moving and stacking goods onto pallets so they’re ready to be transported out of the factory or plant. It is an exhausting and potentially dangerous task, particularly if workers are handling heavy or hazardous items, that can easily lead to injury and loss of stock due to one simple mistake.
In large manufacturing plants, traditional industrial palletizing robots have typically handled this heavy and repetitive task to remove the risk of harm or human error. While an employee may struggle to keep pace, maintain correct lifting form or stack correctly throughout a long shift, a robot will not get fatigued or start making mistakes no matter how long it is in operation.
Smaller businesses that cannot justify the expense of a traditional industrial robot, or do not have the floor space, may feel that there is no option other than to have workers handle palletizing. Thankfully, cobots are allowing even modest businesses to automate this repetitive and tiring task. Though they do not have the lifting capacity of industrial robots, cobot arms can lift loads of up to 16kg and can work together to move heavier objects.
Cobots also mitigate some of the biggest risks and drawbacks associated with industrial robots. They can work side-by-side with human employees without safety caging thanks to sensors that can automatically stop any motion if someone gets too close. And if there are other, more urgent labor shortages within the factory, the cobot can be repurposed.
Get in touch with one of Universal Robot’s cobot experts to discuss how they can meet your needs today.