The Many Types of Inconsistencies in Barcode Printing and Marking
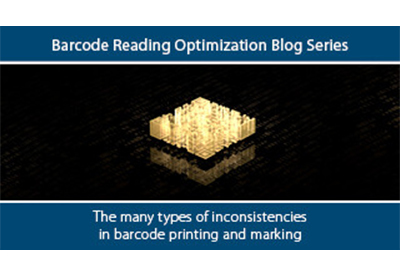
January 13, 2021
Variations in the printing or marking method of barcodes and direct part marks (DPMs) – including poor ink distribution, incorrect thermal printer heat settings, or uneven pressure in surface abrasion – can hamper readability. Since no-reads can make production inefficient, it’s important to understand the types of print/mark inconsistencies and their causes.
Here, each category of inconsistency will be defined and then some possible solutions discussed.
Types of barcode and mark printing issues
1. Contrast is the difference between the light and dark elements of a barcode, or between the code and its quiet zone (the blank area surrounding a barcode) and other perimeter elements. For example, if the dark elements and the light elements of a DPM are too close in value due to low pressure in the marking process, readability will be poor.
2. Axial non-uniformity refers to the amount of deviation along a symbol’s major axes. (For example, a symbol’s Y-axis could be much larger than its X-axis). This inconsistency of X- and Y-dimensions typically indicates unexpected movement of the substrate as the barcode is applied by a printer or direct part marking device.
3. Grid non-uniformity is the amount of deviation in a barcode’s bar or cell elements from the ideal grid of a theoretical “perfect symbol.” Printing or marking errors that cause grid non-uniformity (usually due to unexpected movement of the substrate during code application) will produce a code that appears skewed or distorted, which may be unreadable by standard decoding devices.
4. Modulation refers to the uniformity between light and dark elements of a barcode. If either set of elements does not have a consistent value, unreadability can result. Like low contrast, this issue is often due to inconsistent distribution of ink for printed codes or uneven abrasion for direct part marks.
5. Print growth is the deviation of symbol element size from the theoretically “perfect” element size for a particular symbol. When a symbol is printed, the ink may bleed when it comes in contact with the substrate, causing an overprint. If there isn’t enough ink or pressure applied by printing or marking equipment, the result may be an underprint.
6. A quiet zone is the area surrounding a barcode that must be kept free of text, marks or other obstacles. When a barcode has been printed outside of the designated quiet zone area and is overlapping with other elements on the substrate, no-reads can result. This issue could be due to misalignment or movement of the substrate in relation to the printing equipment.
7. The reflectance of light from a symbol’s light or dark elements is what lets a barcode reader distinguish symbol elements from the background, as well as light elements from dark elements. Low reflectance may increase the probability that a symbol element may be incorrectly identified as light or dark, causing a no-read when the barcode reader attempts to interpret incorrect element patterns. Low reflectance may be caused by inconsistent print distribution or marking pressure by the equipment.
What can you do about printing inconsistencies?
It’s important to regularly inspect and maintain printing and marking equipment to ensure the production of consistently high-quality barcodes and their correct application to parts. When using ink to print codes, be sure to verify the correct distance of the printhead, clean and unblock printheads and nozzles, and ensure correct speed and setup of the printing process.
If barcodes are produced by laser coding, correct focal distance and a continuous power supply to the equipment ensures high-contrast printing without losses in print distribution or speed. Avoid ribbon wrinkles, verify correct insertion of the ribbon into equipment, and use high-quality technologies to evenly apply barcodes and avoid missing elements.
What can you do about inconsistencies in DPM application?
Direct part marking is accomplished by a number of methods, such as electromechanical etch, laser etch, chemical etch (methods in which codes are “scratched” into the substrate) and dot peen (a percussive method in which the symbol is hammered into the substrate with a metal stylus).
The key to producing high-quality marks by direct abrasion is consistent pressure of the abrading component against the substrate. It’s important to verify the quality of the material used to create the abrasion and the amount of power supplied to the marking equipment to ensure that barcodes are applied uniformly and with consistent pressure.