Replenishment Solution for Fulfillment Automation
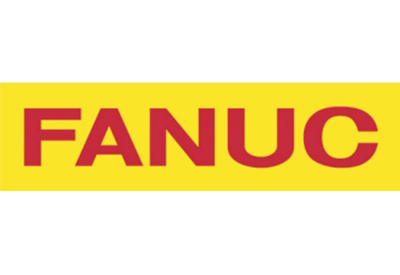
April 14, 2021
Unprecedented growth demands have prompted retail grocery companies to look for more cost-effective automation solutions. While order fulfillment picking operations are applying a variety of automated solutions, decanting operations are virtually overlooked. Decant represents the second highest labor staffing requirement and is the most hazardous.
By 2026, the overall warehouse automation markets will reach ~$30B, with a compound annual growth rate (CAGR) average of 14% between 2020 and 2026. This market’s growth curve is attributed to the transition to eCommerce and omni-channel distribution networks. The automation focus is primarily on autonomous mobile robots (AMR’s), with eGrocery being the largest category in this market.
In 2021, 290 companies (including startups) are offering and/or developing solutions for goods-to-operator order fulfillment. Applications of goods-to-operator can range into the millions of dollars for software and equipment. The solutions vary in technology, with the end goal of improved efficiency by reducing the need for operators to do a lot of walking. Most of the seven figure solutions reduce half of the labor requirement for order picking tasks.
The established providers and dozens of startups backed with hundreds of millions of dollars from investors have begun to develop robotic piece picking to automate the remaining picking/transfer of item(s) task. Robotic order picking is expected to further reduce staffing from 27% to about 6% of the total fulfillment labor cost. The final addition of piece picking robotics will automate 90% of all order picking.
Before advanced automated fulfillment systems was implemented, staffing required for order picking in grocery warehouses represented 55% of the total labor requirement, while decant operations accounted for 25% of labor costs. But so far, investments for decant have trailed behind in the order fulfillment sector.
What is Decant?
Most of the technologies applied to automate grocery distribution rely on uniform storage and handling containers such as storage totes. Decant is the process of removing items or inner packs from their original shipping containers and placing them into totes for automated storage systems that selectively move the totes to pickers and robots for order fulfillment.
While automation for order picking/fulfillment has grown rapidly, decant has been overlooked likely due to a combination of timing and the development of existing technologies. Most of the goods-to-operator automation has been a progression from conveyor based designs and technology. The evolution of automated storage and retrieval systems (ASRS) and AMR’s to service the goods-to-operator stations has been the engineering focus to date, and in reality needs to be in place before the decant process can be fully developed. The recent advancement of vertical AMR robotic ASRS systems and floor-based AMR solutions have provided major advancements, lowered costs and cut installation timelines. Some companies have already revolutionized the storage concept for goods-to-person, and AMR robotics offer additional modular and scalable solutions that have reduced justifications from three to four years to under two years.
The expansion of goods-to-operator solutions sets the table for robotic piece picking to evolve faster. Robotic piece picking costs are justifiable when combined with low cost goods-to-person or robot solutions. With the successful automation of the highest labor cost (fulfillment), automating the decant process will be the next process for the industry to address.
Decant is a New Automation Target
In 2020, articles about major online grocery retailers discussed plans to automate decant operations. FANUC’s system integrator Robotica, Inc. was already way ahead of the game. In 2017, they demonstrated piece picking soft goods at the Promat tradeshow – long before other companies had this capability. By 2018, Robotica pivoted away from piece picking to focus on pack out (ePack) and decant automation. Few solutions existed in these areas, but Robotica’s years of development related to the Automated Box Opening Technology (ABOT) and handling of goods helped.
Efforts really accelerated in 2020 due to COVID-19 pressures on eCommerce. Robotica’s first prototype ePack demonstrated with very high success. For the first time, a shipping box went into the decant area and its contents were carefully packed into tote sub-compartments.
The successful demonstration of complete decant automation providing integrated replenishment for various automated goods-to-operator systems is directly attributed to Robotica’s advanced major patents for decant technology. Through continuous development and testing for specific grocery applications, Robotica has produced robotic decant systems that can offer labor paybacks in less than 12 months.
Leveraging Existing Technology
Much of the technology for automated decant was already developed and in Robotica’s IP portfolio. Many of their box opening technologies have earned domestic and international patents that support the evolution of automated decant from automated box opening, including ABOT which is a key component in automating decant. Now, ABOT M1 is available with state-of-the-art FANUC industrial robots, metrology and the AI capabilities to support decanting of products into totes. ABOT M1’s computational and sensing power makes it the industry’s next-generation intelligent platform for automated decant processes, providing easy integration with goods-to-person AMR systems and other automated processes or work cells.
“Continued development of the ePack technology has produced improvements and new capabilities with a tremendous road map for automated pack station clearly on the horizon,” said Jay Dugat, president, Robotica, Inc.
Robotica has definitely cracked the code and developed a complete automated solution for decanting goods-to-operator systems. Standard units of ABOT M1 and ePack are in production, and further developments have led to new systems for 2021 that provide increased handling abilities, higher rates, smaller footprints and lower costs.
Automated Decant Compared to Piece Picking or Cut and Dump Methods
While piece picking offers discrete unit handling and the ability to produce efficient product stacks in totes and sub-compartments, it’s not flexible enough to handle a variety of SKUs, nor achieve desired rates. Robotic piece picking is limited to a restricted subset of SKU’s, and without AI capability, the picking system’s ability to recognize individual units when packed in a shipping box is also limited.
Tooling requirements also restrict the items that can be picked. Consider the vast range of constantly-changing product packaging, from one-gallon jugs of milk, to vertically-oriented thin foil packages of dip mix, to blister packs of cosmetics. Above all, piece picking suffers from low rates for decant requirements. A typical piece picking decant robot cell would do well at about 600 inner pack units per hour. Larger or heavier items would slow down the system due to tooling actuation times. So, a single piece picking cell performing decant may only average 500 inner pack units per hour of limited package configurations.
According to Robotica’s Dugat, their ePack single cell can handle up to 20,000 inner pack units per hour with far fewer package type limitations, including cylinders, foil packs and cartons.
Cut and dump methods can be cost-effective but have several limitations. In fact, Robotica offered this technology over 10 years ago for a narrow SKU selection in a semi-automated repack process. However, the down side to cut and dump is the vast array of SKU’s required for current decant processes. In the cut and dump method, items free fall into the tote with the likelihood of damaging products and packaging. This typically occurs when commingling SKU’s in a single tote, and it really causes problems for glass items and heavy liquids with fragile seals. In addition, scattering free falling units do not typically yield high efficiencies, and inhibit loading multiples of inner packs or different SKU’s into the tote. It is also unable to support multiple SKU’s into subdivided totes.
Successful Box Opening with AI
Reliable box opening is critical for automated decant operations. Previous automated box opening for picking or decanting processes included operator intervention. That meant that workers were required downstream to address any issues with box opening. However, as more companies experience difficulties hiring and retaining workers to do this process, it’s clear that reliable automated box opening is a “must have” for success.
Robotica’s industry leading second-generation ABOTm-1 for automated decant is a natural progression following years of experience designing and producing multiple commercialized automated box opening technologies. Now, the ABOTm-1 uses data elements to successfully open boxes without damaging the inner pack contents. Generation one systems required an operator to input data for various packages, and used a manual database to maintain the information. However, it quickly became clear that a manual database would not be effective for many eCommerce warehouses that process tens of thousands of SKUs with constantly changing packages and shipping cartons. Plus, in today’s fast-moving distribution culture, maintaining a manual database with this magnitude is far too labor intensive and time consuming.
The ABOT Generation II uses autonomous learning of box dimensions and cutting metrics. This method provides effective data management, and the ability to accurately open an ever-expanding range of box sizes and configurations while protecting the inner packs. The AI module allows for continuous learning and improvement that can be shared across multiple ABOTm-1 machines in a network.
ABOT + ePack – The Ideal Decant System Solution – Features & Benefits
The combination of ABOTm-1 box opening with decant and a FANUC robot into ePack technology is offered in two standard modular production models for quick delivery and installation. ABOT+ ePack systems are easily configured and integrated into micro-fulfillment and large DC applications. For example, a single ePack-Micro processes up to 400 shipping cases per hour, and a single ePack-DC handles up to 800 cases per hour. Higher volumes are achieved using multiple cells, and options include automated receiving, de-palletizing, dimensioning, weighing and scanning.
Robotica’s decant automation can be integrated with robotic material movement or an existing conveyor. The ePack technology simplifies material movement for decant. Replenishment supply (donor cases) and order inventory (totes) can be handled, buffered, and managed.
The ePack systems easily interface with various AMR or goods-to-operator robotics without special programming or interface equipment. In addition, ePack is adept at receiving and delivering inventory totes to and from static shelf positions or onto a takeaway conveyor. And, ePack can access totes randomly for buffering, SKU matching and/or compartment matching.
Pre-programming ePack for specific SKUs or item shapes and case sizes is not required. First time cases and contents are automatically handled based on rules constantly fine-tuned by ePack’s AI.
Multiple caseloads of inner pack unit items can be placed in a tote or sub-compartment using ePack’s volumetric efficiency, which automatically matches sub-compartment sizes with the unit batch size. The ability to consolidate items helps replenish partially filled totes; ePack can create empty spaces or voids with partially filled, randomly located items in a destination tote and then fill the void created with additional replenishment inner pack items.
ePack automatically handles an extremely wide range of unit shapes, sizes and packaging including cans, bottles, free form shapes and blister packs. Orientation of unit items is variable based on best fit or overridden (top of unit up) for items prone to leaking. Glass items and fragile unit items are loaded gently. Empty shipping cases and tops are automatically transferred to recycling.
In conclusion, it’s important to recall that in terms of labor costs, decanting is second only to fulfillment jobs. And, almost every product ordered on-line originates from a shipping box that needs to be opened before those items or inner packs are removed and placed into totes that hold product for order fulfillment. At a time when major investments are being made to develop automated picking operations, Robotica’s new ABOTm-1 represents the only complete automated decant process technology.