Reducing Automotive Downtime with Remote IO and IO-Link Innovations
January 2, 2025
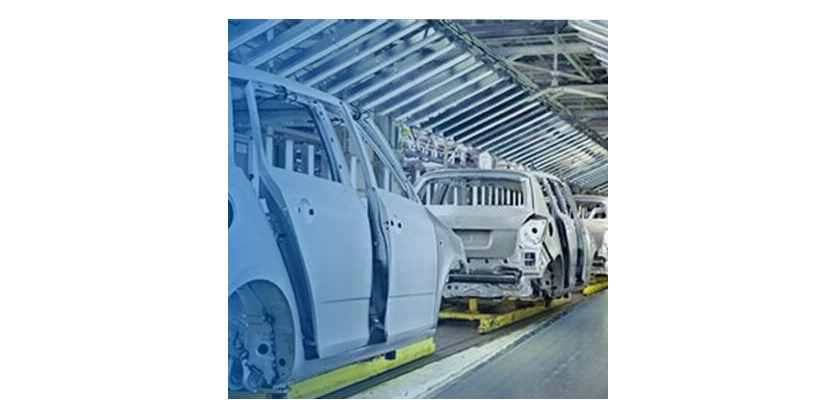
In the fast-paced automotive industry, every second of manufacturing uptime counts. With potential losses of over $30,000 per minute, minimizing downtime is not just important – it is crucial. Enter the game-changes: remote I/O and IO-Link technologies. These innovations have transformed the landscape, enabling automotive plants to significantly reduce downtime and shift towards proactive maintenance strategies.
Remote I/O with IO-Link offers an unparalleled advantage with the ability to isolate and address issues without halting the entire production line. IO-Link technology takes this a step further, facilitating both predictive maintenance and swift component replacement. When an IO-Link sensor or device fails, it can be seamlessly swapped out with a new one. The best part? All settings are automatically updated, eliminating the need for manual recalibration and saving precious time. This isn’t just about keeping up with the pace; it’s about setting it.
Navigating Downtime Challenges in the Automotive Sector
While these technologies offer substantial benefits, several challenges persist. Although sensors can be automatically restored, Remote I/O and IO-Link Masters still require manual configuration during replacement. When these devices fail, technicians must connect them to a laptop and manually adjust settings, prolonging downtime. Retrieving a laptop and locating setting files can be cumbersome, and if the technician is unfamiliar with the software, troubleshooting becomes more time-consuming. Furthermore, not all technicians have immediate laptop access, potentially necessitating off-site assistance and further delaying repairs.
Identifying Common Failure Points in Automotive Applications
In automotive plants, IO-Link masters are particularly susceptible to failure in two key applications. In welding, weld slag can damage sensors and wiring, causing short circuits. In stamping, prolonged vibration can lead to shorts as wiring wears down over thousands of cycles. While IO-Link masters typically include short circuit protection, this safeguard is temporary, lasting only a few hours. If a short circuit goes undetected and unresolved, the IO-Link master will ultimately fail. Although these devices have features to alert users to short circuits, these notifications are often overlooked during system setup. Consequently, maintenance technicians must attend not only to failed IO-Link devices but also to the IO-Link masters themselves.
OMRON’s Quick Switch Feature: Revolutionizing Downtime Solutions
OMRON, recognizing the challenges in traditional machine maintenance, innovated a new approach with their patent-pending Quick Switch Feature. This advancement enables the setup and replacement of IO-Link masters without the need for a laptop, streamlining the maintenance process. The device can be easily configured using a simple rotary dip switch and a screwdriver. When a replacement is necessary, the maintenance technician merely needs to replicate the switch settings from the failed unit onto the new one. This not only simplifies the procedure but also significantly reduces downtime during failures. By eliminating the need for additional equipment and complex configurations, OMRON’s Quick Switch Feature enhances efficiency and minimizes disruptions in automotive plant operations.
Enhancing Efficiency with Advanced Maintenance Solutions
As technology advances, it’s crucial not to overlook the importance of maintenance and the tools required to minimize downtime. Have you considered what your maintenance team needs to ensure the shortest possible downtimes? Innovations like plug-and-play replacements that don’t require a laptop can significantly reduce downtime and enable any member of your maintenance staff to perform repairs when failures occur. By investing in such advanced solutions, you can enhance overall efficiency and keep your operations running smoothly.
Proven Success in Welding Applications
Discover how Omron minimizes downtime across your critical sensors. Explore the success story below to learn how they assisted a Tier 1 Automotive Supplier in significantly reducing machine downtime with their welding sensors.
More Information
Related Story
Improving Industrial Sensing: Omron’s Smart Fiber Sensor
Omron, a leader in industrial automation, has recently unveiled its latest Fiber Optic Amplifier which addresses critical market problems, and improves the way industrial sensing is approached. This blog post will delve into the big picture impact of this product release, focusing on the solutions it offers and the effects it can have on various industries.