Operating Principles of Omron Inductive Proximity Sensors
August 12, 2024
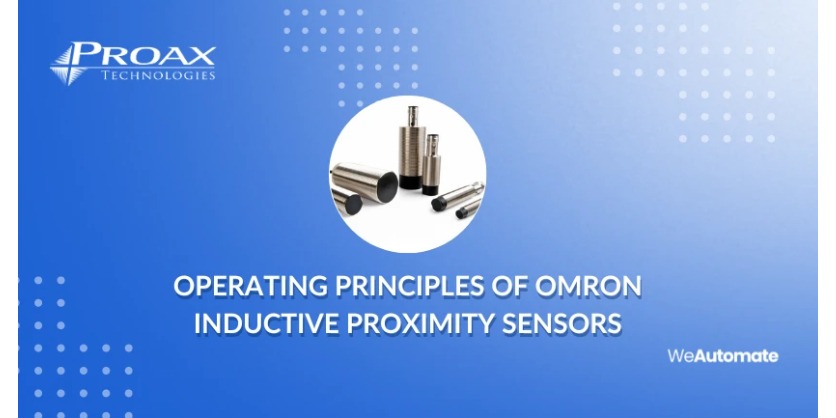
Modern automation and industrial control systems rely heavily on inductive proximity sensors like ones from Omron. These sensors use the principles of electromagnetic induction to determine if metallic items are present or absent without coming into direct touch with them. Their resistance to harsh circumstances, such as exposure to dust, grime, oil, and moisture, makes them appropriate for a variety of industrial settings and applications. Proax Technologies is here to provide the best sensor options from Omron, a leading manufacturer of industrial automation components, and a renowned range of inductive proximity sensors.
Commons types of inductive proximity sensors
Shielded (Embeddable) Sensors: The metal housing of shielded sensors enables them to be installed flush with metal surfaces without being impacted by nearby metal objects. Their tiny design makes them perfect for usage in areas where metal interference from neighboring objects may be a problem.
Unshielded (Non-Embeddable) Sensors: Compared to shielded sensors, unshielded sensors feature an exposed sensing coil and a greater sensing range. To prevent interference from adjacent metals, they do, however, need extra room surrounding the sensor.
Factor 1 (Equal Sensing Distance for All Metals) Sensors: These sensors are incredibly adaptable since they have an equal sensing distance for all metals, including non-ferrous metals like copper and aluminum and ferrous metals like iron. They are widely used in sectors including recycling centers, mixed-metal production lines, and applications involving a variety of metal components where different metals must be reliably recognized.
Operating Principles
Omron inductive proximity sensors operate based on the principle of electromagnetic induction, enabling them to detect metallic objects without direct contact. These sensors generate a high-frequency electromagnetic field from their detection face, typically through a coil. When a metallic object enters this field, it induces small electrical currents, known as eddy currents, on the object’s surface. These eddy currents create a disturbance in the sensor’s electromagnetic field, leading to a reduction in the amplitude of the oscillation within the sensor’s circuit.
The sensor’s detection circuitry monitors this disturbance, and once it reaches a specific threshold, the sensor activates its output circuit. This output usually serves as a simple on/off signal, indicating whether a metal object is within the sensor’s detection range. The sensing distance varies depending on the size, shape, and material of the object, as well as the sensor’s design. Shielded sensors, which can be mounted flush with metal surfaces, have a shorter sensing distance, while unshielded sensors, with a longer sensing range, require more space around the sensing face to avoid interference.
Omron inductive proximity sensors are known for their fast response times, making them ideal for high-speed applications. They are also robust and can operate in various environmental conditions, including dusty or wet environments, due to their sealed construction. These sensors are widely used in industrial applications for tasks such as position detection, object counting, and automation in manufacturing processes.
Key Features:
- Non-contact Detection: These sensors detect objects without physical contact, reducing wear and tear and increasing the lifespan of both the sensor and the target object.
- Durability: They are robust and can operate in harsh environments, including areas with dust, dirt, oil, and moisture.
- High Speed and Precision: Inductive sensors can detect metallic objects quickly and accurately, making them ideal for high-speed automation processes.
- Safety: By detecting the presence or absence of objects, these sensors contribute to safety in automated systems, preventing machinery from operating under unsafe conditions or avoiding collisions.
- Maintenance Reduction: The non-contact nature and durability of these sensors reduce maintenance requirements, leading to lower operational costs and less downtime in industrial settings.
Applications
Because inductive proximity sensors can detect metallic objects without making physical contact, they are frequently employed in industrial and automation applications. They are frequently used in position-sensing procedures in manufacturing to keep an eye on whether metal components are present in machinery and assembly lines. These sensors play a critical role in automated manufacturing lines by identifying metal components and triggering operations like drilling, welding, or cutting only when the metal is positioned appropriately.
In conveyor systems, inductive proximity sensors are used for object counting, detecting metal objects as they pass by, which helps in managing inventory or quality control. Additionally, these sensors are used in safety systems to detect the position of machine parts, preventing machinery from operating when a part is missing or out of place. Inductive proximity sensors are also found in automotive applications, such as detecting the position of metal components in engines or transmission systems, contributing to the efficiency and safety of vehicles.
Contact Proax today to further discuss your needs and discover more about Omron inductive proximity sensors. Their experts are here to provide tailored solutions that drive efficiency and performance.
Related Story
Omron Honours Proax Technologies as 2022 Strategic Partner of the Year
Omron Automation Americas, a provider of industrial automation solutions, takes great pride in naming Proax Technologies as its Canadian Strategic Partner of the Year. This honor underlines Proax’s exceptional dedication and contribution to both Omron and its clientele over the previous year. As a leader in automation distribution, Proax has collaborated with Omron on numerous projects, earning its place as a reliable Canadian partner.