Mitsubishi Electric Helps Elevator Technicians “Peer Through Walls” for Better Troubleshooting
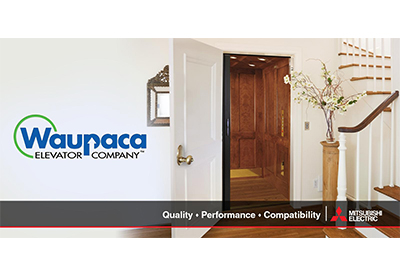
November 2, 2021
A new case study released, highlighting the success of Mitsubishi Electric’s PLC data logging and diagnostics technologies, as well as its variable frequency drives.
Mitsubishi Electric has announced its newest customer success story, focused on Waupaca Elevator Company, which manufactures residential elevators and dumbwaiters for applications across North America. Waupaca Elevator sells through independent dealers, who need consistent reliability and simple, intuitive ways to service and maintain the elevators.
Waupaca Elevator implemented Mitsubishi Electric’s latest iQ-F compact programmable logic controllers (PLCs). The systems’ built-in data logging and diagnostic capabilities enable dealer service technicians to track the usage history of each elevator and monitor service fault codes. Technicians get deep visibility into the elevator system to more easily troubleshoot issues.
This visibility results in faster installations, since technicians can quickly pinpoint where trouble is occurring, as well as faster and more accurate diagnoses of specific issues. It also allows for preventive maintenance, which addresses issues before they escalate. All of these benefits lead to significantly quicker service calls and greater productivity overall.
Another way the manufacturer helped dealers is by implementing Mitsubishi Electric variable frequency drives (VFDs) to mitigate the effects of voltage fluctuations on elevator braking resistors. VFDs allow braking resistors to turn off automatically as needed, thereby eliminating the effects of voltage fluctuations such as overheating and reduced resistor life.
Mitsubishi Electric has helped Waupaca greatly increase ease of installation and ease of service. Gary Ziebell, Vice President and General Manager at Waupaca Elevator, says, “The other nice thing is that, now, if a drive gets damaged in the field, we can just send them a drive right off the shelf. We don’t have to program it. The technician can just drop it in and the unit is up and running. The PLC does the programming automatically.”
To learn more, read the complete case study.