Machine Vision: Hardware, Software, and Applications
August 16, 2023
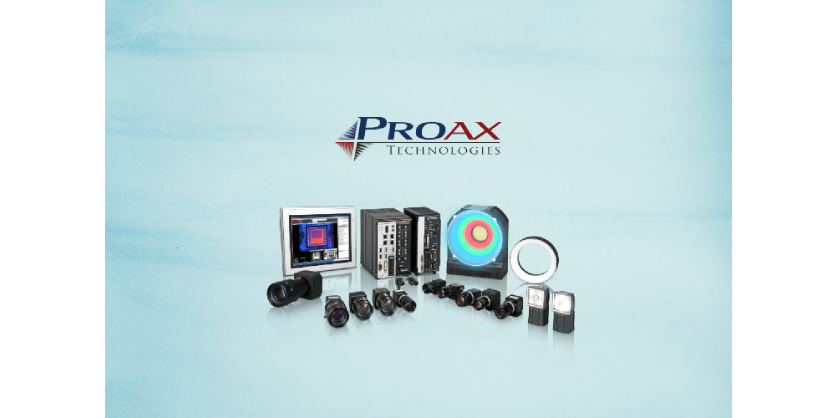
What is Machine Vision?
Machine vision is a fascinating area that merges elements from computer science, optics, mechanical engineering, and industrial automation. It gives machines the ability to ‘see’ by letting them capture and interpret digital images or video in real time.
In simpler terms, machine vision is all about giving machines a kind of visual sense. It enables machines to inspect, measure, identify, and recognize different objects or areas. This is especially useful in industries like manufacturing, where machines can use this vision to spot defects, sort items, or guide other equipment accurately and efficiently. Computer hardware and software together are used to perform the following tasks:
- Image & video capture
- Image processing & analysis
- Visual inspection & measurement
- ID mark reading & verification.
- Machine & robot guidance
How Does Machine Vision Work?
Image Acquisition: The first step is image acquisition referred to as a process of capturing visual information using cameras or sensors. It involves capturing images or video frames of an object or scene which is then analysed and interpreted by machine vision software. The quality of the acquired data serves as input for various machine vision tasks such as object recognition, tracking, and measurement.
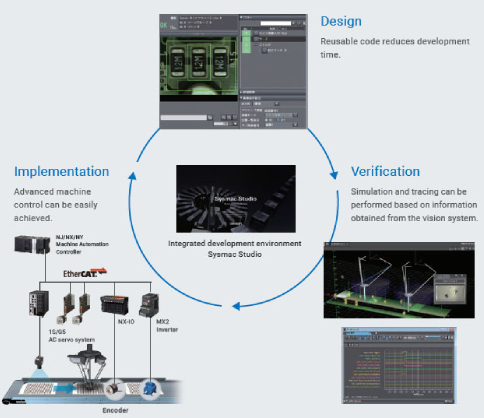
Detection/Segmentation: In this step, image processing algorithms can be used to separates the objects from its surrounding features. Segmentation is the name given to this procedure. Depending on the attributes of the image and the application, several techniques are available, including greyscale or color thresholding, grayscale or color, thresholding, thresholding, high and low pass filtering,dilate and erode, and gradient methods.
Preprocessing: After an image has been acquired, it may go through preprocessing image tools to enhance the image data. Various approaches, such as noise reduction, contrast enhancement, or image sharpening, can be used during preprocessing. Enhancing the image quality can draw attention to certain features the image.
Analysis/Recognition: The system can examine the image segments following segmentation. For instance, a facial recognition system might search for particular features like the lips, nose, and eyes. These characteristics could be arranged to identify a face.
Last, the system tries to comprehend or interpret the image in light of the analysis. A system may, for instance, recognize many pictures of the same face. Additional research may be required for the interpretation, or it may simply be the outcome.
How can Proax Help You?
A. Identifying Your Requirement:
The first stage is to identify the problem that needs to be resolved precisely. What purpose must the machine vision system serve? What potential obstacles might arise?
B. Choosing the Appropriate Hardware:
A machine vision system typically comprises cameras or other detectors and appropriate illumination. The choice of hardware will be influenced by factors such as the required level of detail, the working environment, and the required performance.
C. Utilizing or Developing Appropriate Software:
Software is crucial in interpreting the machine vision system’s collected imagery. It may involve developing custom software or utilizing existing solutions. Machine learning algorithms can also enhance image analysis, particularly in more complex scenarios.
D. Seamless Integration with Your Existing Systems:
Proax must ensure their machine vision system is compatible with your existing robotic controllers, PLCs, and data management systems. This procedure necessitates careful planning and testing to ensure faultless execution.
E. Rigorous Testing and Optimization:
Thorough Testing and Fine-Tuning: Once the system has been installed, it is essential to conduct rigorous testing and fine-tuning to ensure optimal performance.
F. Empower Your Staff:
They will ensure that your staff is thoroughly trained in the operation and maintenance of the new machine vision system. In addition, they will provide ongoing support to resolve any issues.
Machine vision systems often require the following in manufacturing environments:
● Lighting: Imagine reading a book in a dark room – pretty tricky, right? Well, the same principle applies to machine vision systems. Good lighting isn’t just about ensuring everything is bright enough to be seen. It’s about strategically illuminating what interests us so the features stand out clearly. Think of it like shining a spotlight on a stage performer.
● Lens: The lens is the system’s eye. It’s responsible for collecting all the light bouncing off the object or scene and focusing it onto the camera’s sensor, much like how our eyes work. It’s essential to make sure the lens is suitable for the job, considering how far away it is from the object and how comprehensive a view it needs to capture.
● Capture Board, Frame Grabber, or Sensor: Once the lens has done its job, it’s over to these components. They’re like the brain’s translator, turning the light from the camera into a digital language of pixels that the processor can understand.
● Processor: Speaking of the processor, you can think of it as the system’s detective. It uses software and algorithms to examine the digital image, find meaningful information, and solve whatever problem we’re interested in – maybe identifying shapes, measuring distances, or recognizing patterns.
● Communication/Output: Finally, once all the work is done, the machine vision system must share its findings. Whether part of a more extensive network of machines or a standalone system, it communicates what it’s learned, often triggering the next step. Think of it like a team player passing the ball to a teammate.
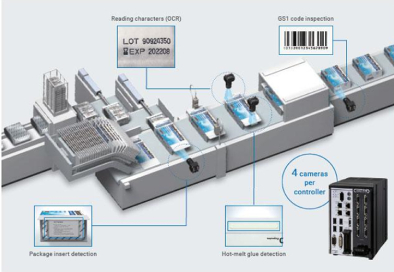
Machine Vision products are versatile and designed to meet various industry needs. Here’s a breakdown of what they have to offer:
- Vision Systems: Think of these as the powerhouses of vision inspection. They are adaptable and can tackle all kinds of identification and inspection tasks.
- Vision Sensors: These handy gadgets are compact, easy to incorporate into any system, and provide a cost-effective solution for your vision inspection needs.
- Smart Cameras: These all-in-one devices pack a camera, a processor, and vision software. They’re perfect for robust inspection tasks and are a breeze to set up and use.
- Code Readers: Need to keep track of things or ensure everything is traceable? we got you covered with their code readers. Whether you prefer handheld or fixed-mount models, these readers can easily handle 1D and 2D codes.
- Lighting and Lenses: Vision inspection can only be successful with the proper lighting and optics. That’s why Proax offers a variety of lighting solutions and top-notch lenses to ensure you get the best possible image.
- Vision Software: This is where things get technical. But don’t worry, vision software is designed to make the development and deployment of vision applications as easy as possible. Plus, it comes with user-friendly interfaces and some pretty impressive features.
Machine Vision’s Advantages in The Manufacturing Industry:
Enhanced Precision: Machine vision systems powered by advanced algorithms and high-resolution cameras deliver highly accurate results. This technology makes it easier to detect even the tiniest product flaws or deviations, ensuring stringent quality control standards are met.
Simple Integration: With user-friendly machine vision software and straightforward programming interfaces, integration into existing systems is simplified. This enables seamless communication with current production lines and systems, minimizing disruption and enhancing overall efficiency.
Versatility and Adaptability: Machine vision systems are extremely flexible, accommodating a range of applications and industries. With various camera types, including area scans, line scans, and 3D cameras, these systems can perform a wide array of inspection tasks, such as surface inspection, defect detection, measurement, and barcode reading.
Machine vision systems provide real-time surveillance and data reporting, which facilitates immediate adjustments and interventions when any issues or irregularities are detected. This proactive approach prevents production delays, minimizes waste, and boosts overall manufacturing efficiency.
The integration of machine vision systems with automation systems allows for automated control and communication between different pieces of equipment. This improves the complete process automation by enabling synchronized inspections, initiating actions based on these inspection results, and triggering the actions themselves.
Machine Vision Cameras: Machine vision cameras are imaging instruments designed specifically for industrial applications. They capture images with a high resolution and send them to vision systems for analysis. These cameras are endowed with high-speed shutters, interchangeable lenses, and advanced sensors, allowing them to operate effectively in demanding manufacturing environments. diverse types of machine vision cameras, such as area scan cameras, line scan cameras, and 3D cameras, are suited to diverse inspection tasks.
Vision Controllers and Cameras:
These machines are powered by vision controllers, which function as the operation’s central processing unit. Vision controllers are responsible for receiving image data from cameras, analyzing the data using complex algorithms, and issuing system instructions based on the data analysis. Their primary responsibilities are image capture, preprocessing, feature extraction, pattern recognition, and decision-making. Commonly, these controllers work with potent processors and interfaces for seamless integration with other industrial automation equipment.
Cameras explicitly designed for machine vision are essential to this configuration. These cameras acquire high-resolution, high-speed images of the objects or products being inspected. The captured images are then transmitted to the vision controller for processing, where decisions are taken according to predefined principles or machine learning algorithms. These cameras are designed with industrial applications in mind, allowing them to operate in various lighting conditions.
Advanced visual surveillance systems that automate quality control, enhance safety measures, and streamline processes are provided by machine vision technology, transforming the manufacturing sector. The capacity of this technology to process vast quantities of data and produce accurate, consistent results has made machine vision systems indispensable in contemporary manufacturing. Enhance your machine vision capabilities with Omron.
More Information
Contact Proax Technologies to discuss advanced machine vision solutions
Related Story
Omron Honours Proax Technologies as 2022 Strategic Partner of the Year
Omron Automation Americas, a provider of industrial automation solutions, takes great pride in naming Proax Technologies as its Canadian Strategic Partner of the Year. This honor underlines Proax’s exceptional dedication and contribution to both Omron and its clientele over the previous year. As a leader in automation distribution, Proax has collaborated with Omron on numerous projects, earning its place as a reliable Canadian partner.