Introduction to Motion Controllers from Electromate
November 16, 2023
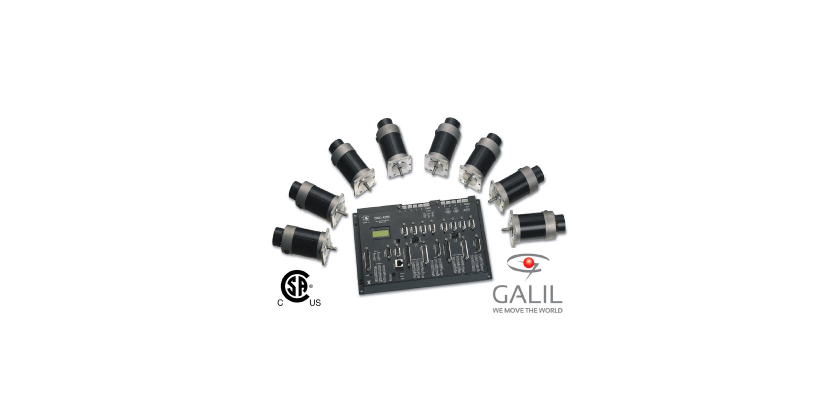
In the realm of automation and robotics, the precision and accuracy of movement is paramount. The brain behind these meticulous movements is the motion controller, a device designed to control the sequence, velocity, position, and torque of a mechanical system.
Motion controllers play a pivotal role in a myriad of industries, from manufacturing and medicine to entertainment and research. They interpret a desired movement or action, converting it into electrical signals that drive a system’s motion components, ensuring operations are accurate, reliable, and efficient.
Fundamentals of Motion Controllers from Electromate
Understanding motion controllers requires a delve into their core functionalities and components.
Command and Control Logic – The heart of any motion controller is its command-and-control logic. This is the system’s ability to understand, interpret, and execute specific movement instructions.
- Input Formats: Motion controllers can accept commands in multiple forms, including high-level programming languages or simpler point-and-click interfaces. The complexity of the instruction can range from simple single-axis moves to intricate multi-axis coordinated sequences.
- Processing Power: As the movement patterns become more complex, the processing requirements for the controller increase. Modern motion controllers come equipped with powerful processors and dedicated algorithms that can compute trajectory plans in real-time.
- Output Signals: Once the command is processed, the controller sends electrical signals to the relevant motion devices to initiate the desired movement. These signals need to be highly synchronized, especially in multi-axis systems, to ensure fluidity and precision of movement.
Feedback Systems – Feedback systems are crucial in maintaining the accuracy and reliability of motion controllers.
- Encoders: These are devices that convert the position of a shaft or axis into an analog or digital signal. There are different types of encoders, like incremental or absolute, each providing different levels of resolution and feedback detail.
- Resolvers: Resolvers function similarly to encoders but utilize analog signals and are often employed in environments where robustness against harsh conditions is required.
- Closed-loop Control: Feedback mechanisms enable motion controllers to operate in a closed-loop system. In such setups, any discrepancy between the commanded and actual positions is corrected in real-time, ensuring precise positioning and responsiveness.
Drive Interface – The interface between the motion controller and the drives is crucial, as it facilitates the conversion of commands into physical motion.
- Drive Types: The two primary drive types interfaced with motion controllers are servo drives and stepper drives. Stepper drives move in discrete steps and are simpler but might lack the precision of servo drives, which provide continuous motion with high accuracy.
- Signal Transmission: The interface encompasses both the format (analog, digital, pulse-width modulation) and the medium (wires, optical fibers) of signal transmission. Proper matching between the controller’s output and the drive’s input ensures seamless operation.
- Safety Protocols: This interface often includes safety protocols to prevent issues like overcurrent, overheating, or unexpected motion, ensuring the system operates safely and reliably.
Types of Motion – Motion controllers can govern a wide variety of movement types, catering to different application requirements.
- Point-to-Point Motion: This is the most straightforward motion type where the system moves from one predefined point to another. It’s often used in pick-and-place operationAdvantages of Motion Controllerss or any application where the journey between points is not critical. Point-to-Pont Motion can be incremental, relative, or absolute in nature.
- Continuous Motion: In this type, the movement occurs at a constant speed, suitable for applications like conveyor systems or spinning components.
- Synchronized Motion: Often used in complex systems, synchronized motion coordinates multiple axes of movement simultaneously. Applications include CNC machining, where the coordinated movement of the tool and workpiece is vital, or in robotics, where an arm might need to move along multiple axes simultaneously to reach a destination.
Advantages of Motion Controllers
Precision and Accuracy – Motion controllers are foundational in achieving highly precise and accurate movements in automated systems.
- Real-time Adjustments: With continuous feedback, motion controllers can make instantaneous corrections to ensure the motion system follows the exact desired path or reaches a specific position. This is especially crucial in applications like CNC machining or robotic surgery where even minute deviations can be costly.
- Elimination of Manual Errors: By relying on pre-programmed instructions and real-time feedback, the chance of human-induced errors in motion is significantly reduced, leading to consistent and repeatable results.
Speed and Efficiency – The incorporation of motion controllers can drastically improve the operational speed and efficiency of systems.
- Automated Sequences: Complex sequences that might take humans hours to perform manually can be executed in mere minutes or seconds, significantly enhancing throughput and productivity.
- Reduced Downtime: With fewer errors and real-time adjustments, systems experience less downtime due to mistakes or recalibrations, leading to more consistent operations and improved overall efficiency.
Versatility – Modern motion controllers offer unparalleled versatility in how they can be used.
- Adaptable to Variable Motions: Whether it’s simple point-to-point movement, continuous rotation, or synchronized multi-axis coordination, motion controllers can be adapted to manage them all.
- Reprogrammable Nature: As production needs change or new tasks arise, motion controllers can be reprogrammed, providing flexibility without the need for major hardware modifications.
Safety – Safety is paramount in automated systems, and motion controllers play a pivotal role in ensuring it.
- Anomaly Detection: Advanced motion controllers continuously monitor operational parameters. If they detect anything outside the preset thresholds—like overheating, excessive force, or rapid unplanned deceleration—they can initiate corrective actions.
- Proactive Prevention: Instead of just reacting to issues, many modern controllers predict potential problems using algorithms and historical data, allowing for preemptive interventions before actual issues arise
Integration – Integration capabilities are a standout feature of modern motion controllers, allowing them to be part of holistic control environments.
- Interoperability with Other Systems: Many motion controllers are designed to work seamlessly with other system components, from sensors and vision systems to databases and user interfaces, ensuring a harmonious operation.
- Centralized Control: With integration capabilities, a single motion controller can often manage and coordinate multiple subsystems, offering Challenges and Considerationscentralized oversight and control, simplifying the overall system architecture.
The advantages underscore the transformative potential of motion controllers in the realm of automation. They enhance precision, speed, safety, and versatility, all of which are critical for the modern industrial and technological landscape.
Challenges and Considerations
While motion controllers bring substantial advantages to automated systems, it’s crucial to be aware of the challenges and considerations associated with their adoption.
Complexity – The precision and capabilities of modern motion controllers come with inherent complexities:
- Programming Nuances: Setting up and programming advanced motion controllers to achieve desired outcomes might require deep technical knowledge. This can be particularly challenging for intricate tasks or when integrating with other complex systems.
- Maintenance and Troubleshooting: As with any sophisticated equipment, diagnosing and rectifying issues can be challenging. Overlooking a minor configuration or calibration error might lead to larger operational issues, necessitating well-trained personnel to ensure smooth operation.
Cost – Financial implications are always a consideration in system upgrades or overhauls:
- Initial Investment: High-end motion controllers, particularly those offering state-of-the-art precision and features, can come with a substantial price tag. Additionally, the cost isn’t just for the controller; supplementary components like HMIs, specific drives and motors, or advanced feedback systems may also contribute to the overall expenditure.
- Ongoing Expenses: Beyond the initial purchase, there might be ongoing costs for software updates, periodic maintenance, and/or potential replacements of downstream system parts. It’s essential to consider the total cost of ownership over the system’s lifespan
Compatibility – Compatibility challenges can arise, especially in mixed-brand or older systems:
- Hardware Compatibility: Ensuring that the motion controller can seamlessly communicate and control the drives, actuators, sensors, and other system components is crucial. Mismatched components might lead to reduced performance, increased wear, or even system failures.
- Software Integration: Motion controllers typically come with their software platforms or interfaces. Ensuring this software can integrate with other system software or databases is crucial for a cohesive operation.
- Legacy Systems: When integrating a new motion controller into an older system, compatibility issues might arise due to outdated interfaces or protocols. Such challenges might necessitate additional adapters, converters, or even component replacements.
Despite these challenges, the benefits of motion controllers often outweigh the downsides, especially in applications where precision, speed, and efficiency are paramount. It’s about understanding these challenges and effectively addressing them in the design, integration, and operation phases.
The Future of Motion Controllers
In an era marked by rapid technological advancement, motion controllers are not remaining static. Their evolution promises not just enhancements in their primary functionalities, but also an integration into the broader ecosystem of advanced technologies. AI and Machine Learning Integration – The potential of artificial intelligence (AI) and machine learning (ML) in motion control is profound:
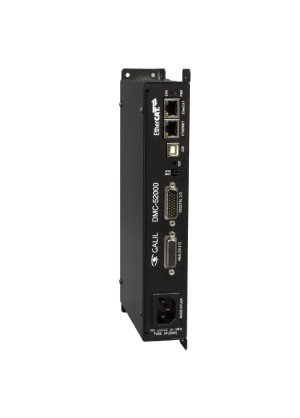
- Self-optimization: By analyzing vast amounts of operational data, ML algorithms can identify the most efficient motion paths and strategies, continuously refining system performance over time.
- Predictive Maintenance: Leveraging AI, motion controllers could foresee potential component failures or wear-and-tear, suggesting maintenance activities before a breakdown occurs. This proactive approach can lead to increased uptime and reduced costs.
- Adaptive Response: Motion controllers could utilize AI to dynamically adapt to changing external conditions or unexpected obstacles, ensuring smooth operation even in unpredictable environments.
IoT Connectivity – With the Internet of Things (IoT) revolutionizing how devices communicate:
- Real-time Monitoring: Motion controllers integrated with IoT can stream operational data in real-time, allowing system managers to remotely monitor performance, diagnose issues, and even make on-the-fly adjustments.
- Predictive Alerts: By analyzing data trends, IoT-enabled controllers might preemptively alert operators to potential issues or required interventions, minimizing downtimes.
- Global Control: Especially beneficial for multinational operations, IoT connectivity means motion controllers in different locations can be monitored and controlled from a centralized location.
Miniaturization – As technological components shrink in size:
- Compact Designs: The miniaturization trend will allow motion controllers to be integrated into applications where space is a premium, from medical devices to micro-manufacturing setups.
- Energy Efficiency: Smaller components typically mean less energy consumption. This not only reduces operational costs but also aligns with global sustainability goals.
- Increased Versatility: Smaller controllers can be more easily retrofitted into existing or embedded systems or adapted for novel applications, broadening their potential usage scenarios.
Enhanced User Interfaces – The way we interact with technology is evolving:
- Immersive Programming: With augmented reality (AR) and virtual reality (VR), engineers and technicians could virtually step into the motion control environment, making programming and troubleshooting a more intuitive and immersive experience.
- Gesture Control: Leveraging advancements in sensor technology, future motion controllers might be programmable through hand gestures or even voice commands, simplifying the user experience.
- Collaborative Environments: AR and VR can allow multiple users to collaboratively interact with the motion control environment, facilitating team-based problem-solving and design sessions.
Embracing the advancements on the horizon for motion controllers not only promises enhanced operational efficiencies but also opens doors to innovative applications and methodologies previously deemed unattainable. As we step further into the digital age, motion controllers stand poised to be pivotal components in the automated systems of tomorrow.
For a comprehensive range of motion controller solutions, explore Electromate’s Motion Controllers. Whether you’re seeking precise control for intricate tasks or robust performance for demanding applications, our motion controllers have you covered. Elevate your automation and motion control projects with Electromate’s cutting-edge technology.
Related Story
ADVANCED Motion Controls Takes Servo Drives to New Heights (and Depths) with FlexPro® Extended Environment Product Line
Advanced Motion Controls (AMC), a leading provider of servo amplifier solutions, is proud to announce the addition of six new CANopen servo drives with Extended Environment capabilities to their FlexPro® line. These new drives join AMC’s existing EtherCAT Extended Environment FlexPro drives, making the FlexPro® line the go-to solution for motion control applications in harsh environments.