Cobot Welding Solutions – How Experienced Welders Feel
March 28, 2023
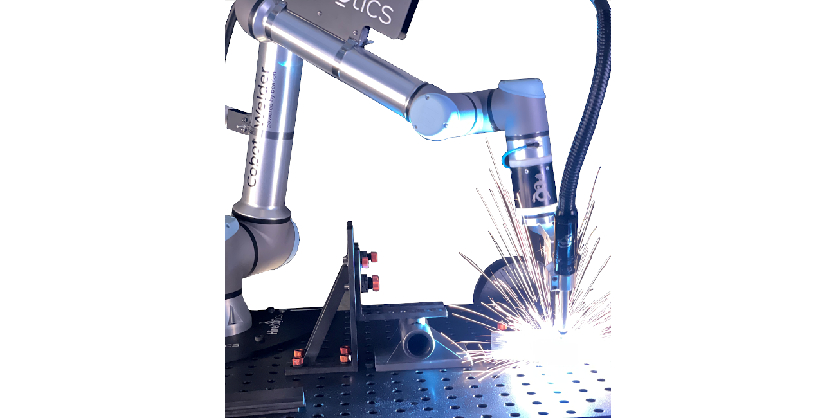
Electromate received some feedback when meeting with experienced welders who were initially resistant to the idea of using a cobot welder. After all, they’d spent years perfecting their welding techniques, and were confident in their ability to produce high-quality welds without any assistance.
However, after some experience, they often come to appreciate the many benefits that this technology offers. Many now consider it to be an important tool in their team’s welding arsenal.
What is a cobot?
For those who may be unfamiliar, a cobot welder is a collaborative robot that works alongside a human welder to assist in the welding process.
These robots are designed to be easy to use and are equipped with advanced sensors and control systems that allow them to respond to their environment in real-time.
One of the main benefits of cobot welding is that it greatly reduces the risk of injury to the welder. Welding is a physically demanding task that requires a lot of repetition and can put a lot of strain on the welder’s body. These devices can take over much of the heavy lifting and repetitive tasks can be taken over by the robot, freeing the welder to focus on other tasks. This can significantly reduce the risk of injury and help to ensure that the welder stays healthy and productive over the long-term.
In addition to improving safety, cobot welding also offers a number of other benefits that are of particular interest to experienced welders. For example, cobot welders are highly accurate and repeatable, which means that they can produce consistent, high-quality welds time after time. They also offer greater flexibility than traditional welding methods, as they can be programmed to perform a wide range of tasks and can easily be adapted to accommodate new welding techniques and materials.
Another key benefit of cobot welding is that it can significantly increase productivity. By taking over many of the time-consuming and repetitive tasks associated with welding, cobots allow welders to focus on more complex and higher-value tasks. This can result in a significant increase in overall productivity, allowing welding operations to complete more work in less time.
Of course, despite all of these benefits, there are still many experienced welders who remain resistant to the idea of using a cobot welder. Some welders may be concerned that the technology will take over their job or that they will be replaced by the robot. However, the reality is that cobots are designed to work alongside human welders, not to replace them. In fact, the use of cobot welders has been shown to create new job opportunities, as welders are freed up to focus on more complex and higher-value tasks.
While it is understandable why some experienced welders may be resistant to the idea of using a cobot, Electromate believes this technology offers a number of significant benefits that are too great to ignore. Whether you are a welder looking to improve your safety, increase your productivity, or take your welding skills to the next level, Electromate encourages you to consider the many advantages of cobot welding. Contact them today to schedule a demo.
More Information
Related Story
Setting up a Dedicated EtherCAT Master Controller Kit and EtherNet IP/Profinet Kit with the Meca500 Industrial Robotic Arm
Nadine Oliynyk is an Applications Engineering co-op student at Electromate Inc and second year Mechatronics Engineering student at the University of Waterloo.
In this article, she describes her experience programming the Meca500 industrial robot arm and setting up the dedicated EtherCAT Master Controller Kit and EtherNet IP/Profinet Kit available at Electromate. The goal of her co-op term was to prepare this kit for customer use by connecting the components and creating sample code and documentation, which would all be available for future users of the control kit.