How Safety Can Make Your Cobot Work Harder and Safer for You
July 10, 2023
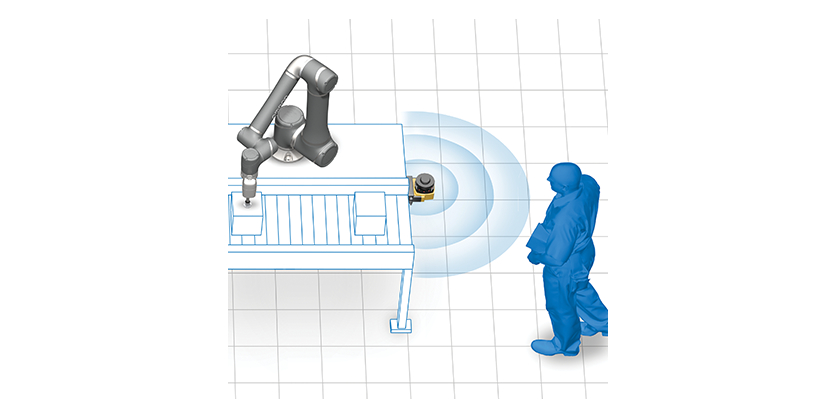
Collaborative robots, or Cobots for short, can greatly enhance productivity and employee satisfaction by taking over dull, reparative, and dirty tasks that humans would rather not perform. Because these robots are designed to work safely around people, many manufacturers are under the impression that no further safety measures are needed.
This is a misconception, however. Appropriate safety measures based on comprehensive risk assessments are still very important. In fact, safety is crucial to unlocking your cobot’s full range of capabilities and maximizing its performance, as we’ll explain in this blog post.
Learn more about cobots and how they’re going to revolutionize a variety of industries in Episode 16 of Omron’s Operation Automation podcast
Wait — but don’t cobots already have safety measures built in?
It’s true that cobots come equipped with numerous safety features including a lightweight frame, collision detection technology, and minimized pinch points. However, these don’t necessarily account for elements that will be added for the purpose of a specific application, such as the type of gripper or end effector and any other equipment being used nearby.
The cobot’s internal safety programming is based upon the length of the robotic arm only when it has no additional elements. Since grippers and end effectors extend the length of the arm, and yet the cobot’s software is unaware of this added length, the built-in safety measures might not be sufficient.
Going beyond these concerns, however, one of the main reasons to add safety to your collaborative workspace — i.e., the area around the cobot in which a human might also be working — is that it allows you to get your cobot running faster when humans aren’t present.
Unlocking your cobot’s full potential with a layer of safety
Without safety, cobots have a maximum allowable speed in any application where a human might enter the collaborative workspace at any time (even if it’s just for a few minutes per day). This maximum speed of 250 millimeters per second per axis is mandated by the RIA TS 15066 standard.
For many applications, this speed is not very fast, and it’s a far cry from the cobot’s maximum possible speed based purely on axis capability. Given that the cobot could be moving much faster when people aren’t around, it sure seems like a waste to keep it going at such a slow rate if the collaborative workspace will be human-free most of the time.
Fortunately, there’s a way to get a much better return on investment for your cobot, and that’s by adding safety measures to the collaborative workspace. If you equip the area with a safety scanner, you can let the cobot know when humans are present or absent, and it will alter its speed accordingly. This dramatically expands its usability.
How a cobot safety scanner system works
A safety scanner uses a laser to scan a designated area and detect whether a person is nearby. Because safety scanners can determine distances, you can set them up with a warning zone in addition to an active trip zone. In the warning zone, you can have the cobot cut its speed down by 1/3, whereas in the trip zone it can go down to 250mm/s/axis or stop altogether.
More Information
Interested in learning more about collaborative robot safety?
Download the White Paper: Collaborative Robot Safety
Related Story
Omron’s Robotic Solutions: Thousands of Possibilities
Robots can improve the productivity of many industries and processes. They can handle a variety of tasks, such as laborious or repetitive work, and can dramatically improve processes in industries such as machine tending, assembly, packaging, and other manufacturing activities. Moreover, they can handle routine operations, allowing employees to perform higher-value tasks.
This article will look at a selection of Omron’s robots and robotic solutions, such as autonomous robots and collaborative robots, and will explore how these products can be integrated into facilities to improve productivity. It also discusses the next evolution in factory automation: MoMa’s, or Mobile Manipulators – the growing trend of having collaborative robots mounted onto AMRs to achieve new levels of automation.