HELUKABEL’s Cables and Wires for Robotics
October 16, 2024
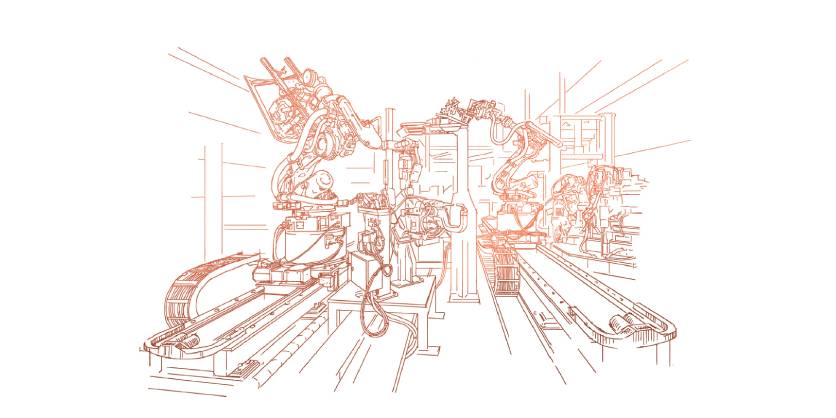
Questions by Krystie Johnston
In many industrial applications, robotics are at the forefront of automation. They allow companies to enhance efficiency and safety, and they transform the manufacturing and production processes. The motion sequences of an industrial robot hinge on the quality of the cables that transmit power and data, as well as the guidance and protection systems that prevent these pivotal components from being damaged by environmental hazards. HELUKABEL has over 25 years of experience developing electrical system solutions for the robotics field. This article explores some of them.
1. Can you start by telling us a bit about yourself and what you do at HELUKABEL?
My name is Keith Wilkerson, and I am the business segment for robotics and automation at HELUKABEL USA. In this role, I also support HELUKABEL Canada when they need additional customer support in designing an electrical system solution for a specific automated application be it on a robot or in a drag chain.
2. What is considered 2D motion vs. 3D motion sequences in robotics?
A two-dimensional (2D) motion sequence involves the robot or its parts moving along two axes, typically referred to as the X and Y axes. A few examples of this would be a robotic arm that moves only horizontally and vertically to pick and place items on a conveyor belt or a mobile robot traveling in a planar environment (like a floor) where it can move forward, backward, left, and right. 2D motion is simpler to control and program using simple sensors such as laser scanners or cameras. In most cases, a 2D motion sequence is sufficient for many industrial applications.
The three-dimensional (3D) motion sequence adds to a robot’s freedom by opening its movement to the Z axis. This allows for a more complex range of motion, including up and down movements. A robotic arm that can move in all three dimensions can reach different heights and angles. 3D motion requires more sophisticated control algorithms and sensors to manage the additional degrees of freedom such as depth sensors, 3D cameras, and more advanced actuators to navigate and manipulate objects in three-dimensional space.
3. How do these motions affect the cables that support power and communication?
There are many characteristics to consider for 2D motion (e.g. drag chain), from a mechanical perspective such as acceleration, travel speed, travel length and cycles per day. These are critical pieces of information that must be known in order to ensure that the cable is constructed using the proper material stranding, insulation, and jacketing materials, as well as the conductor stranding and shield angle.
Some of the desired properties of any industrial cable for 2D motion applications would be high strand counts for increased flexibility, minimal elongation, high tensile strength, good abrasion resistance, and a small bend radius, to name a few.
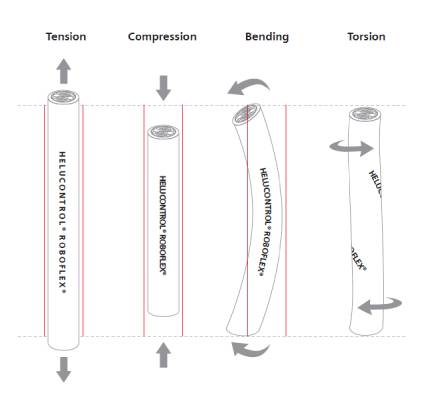
Torsional (3D robotic) cables are required to endure many of the same environmental factors as 2D cables. As previously mentioned, understanding the entire scope of the application is needed in order to make a proper recommendation or design the best solution. Although the flexing of the cable along its entire length is not present in a torsional application as it is with a drag chain application, there is the added rotational stress applied to the cable. This is demonstrated on an articulated robot when axis four (4) rotates in one direction and axis six (6) rotates in the opposite direction. A cable manufacturer must now consider the memory of the copper strands as it relates to that additional stress.
With this in mind, it is important to understand that the torsional value (+/- XXX°) is one of the most critical parameters of a torsional cable. When comparing cables, use this as the baseline for comparison. A cable that is +/- 180° per meter may be acceptable for a 4-axis palletizing robot, but it may not be best suited for a welding robot in an automotive plant. Also, stating that a cable is designed to “withstand torsional applications” is simply not enough to determine if it is the proper solution for the application.
4. What other considerations go into selecting the ideal cable of an industrial robot?
In both 2D and 3D applications, understanding the application from a holistic perspective is always best. In addition to the previously mentioned mechanical properties that must be taken into account, the environment and task should also be taken into consideration. From an environmental perspective, ambient operating temperature, weld splatter, presence of UV and the presence of chemicals or particulates that may come into contact with the robot should be considered. Some of the desired properties of any industrial cable would be a wide temperature range, sunlight resistance, high oil resistance, low capacitance and flame propagation.
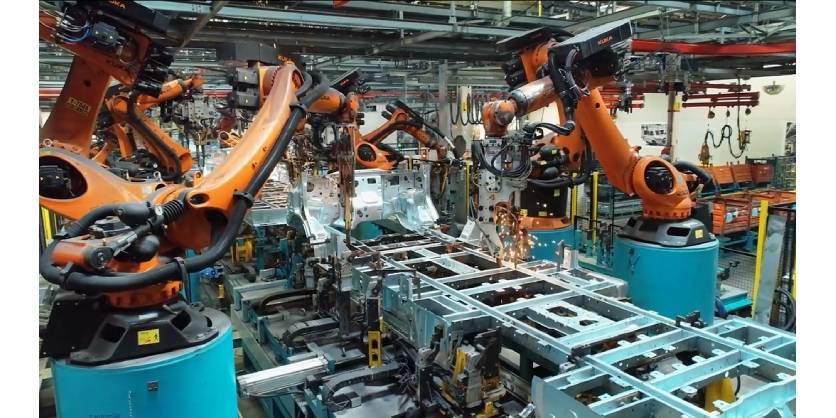
5. What is HELUKABEL’s ROBOFLEX portfolio of torsion-resistant cables?
Our ROBOFLEX® portfolio of torsion-resistant cables covers the entire range of applications that one might find on an industrial robot. These shielded, or unshielded, multi-conductor cables cover control power, data transmission, motor power, and sensor cables. Furthermore, where space-saving needs are required, hybrid cables that transmit both power and data are available. These cables are built at all levels – conductor stranding to outer jacket – to withstand chemical, thermal, and mechanical stresses associated with torsion, bending, flexibility, and abrasion, and are resistant to notches, and oil and weld spatter.
6. What do HELUKABEL’s robotic dress packs consist of?
Our robotic dress pack systems combine all of the components necessary to protect and guide the cables and media hoses around the robot to avoid any kinking, pinching, or physical damage to the robot which might incur unscheduled maintenance and downtime. The key components of this system are the corrugated tube that provides the first level of cable and hose protection, the system holders and articulating joints that route the tubing around the robot so it can move unabated, and the spring return or recirculation system that allows safe movement of the service loop portion of the corrugated tubing between Axis 3 and Axis 6.
Finally, we have impact protectors that are used to minimize wear and tear of the corrugated tubing as it “snakes” over the robot arm.
7. How does HELUKABEL’s 25 years of experience help them develop electrical system solutions for robotics?
Twenty-five years of experience in the robotics field have allowed us to collect a lot of data on the electrical system’s performance. Not only the data acquired in our testing labs on the cables but also in-the-field data to have a clear understanding of when the systems will fail so we can avoid them. It sounds negative but system failure is not an if, but a when.
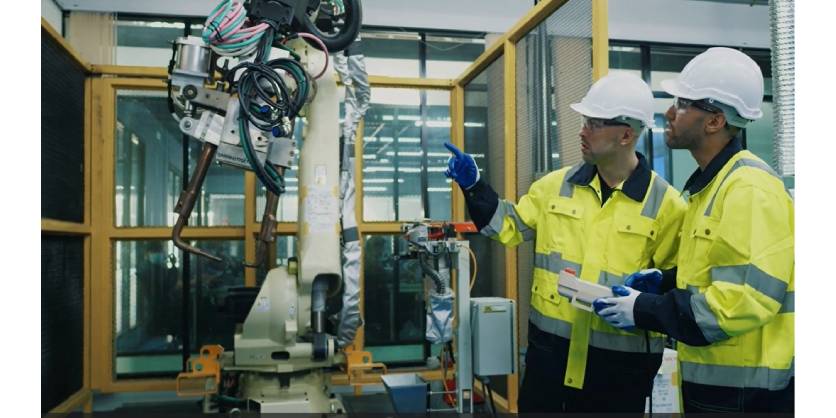
From torsion cycle counts and the proper materials and cable construction, we are able to know well in advance the service life of the cables we provide for each dress pack system. This way, customers know when to properly schedule maintenance to replace components in order to maximize uptime.
8. Are HELUKABEL’s cables and wires pre-assembled or are they customized? Or both?
They can come both pre-assembled and custom-made. In most cases, our standard product range will work and can be combined with the correct connectors as we build the fill package. If we have to tailor-make the cable this is due to our standard product range not being able to fulfill the demands of the application. This is why we strive to understand the application from a holistic perspective to provide the best solution that is tailored to the customer’s unique circumstances.
9. What are some guidelines HELUKABEL follows with respect to using cable assemblies versus hard wiring industrial robots?
Thanks to low installation costs, hardwiring remains the most common way to bring power and data signals to an industrial robot. However, everyone in the design/build process needs to consider the total cost of each option. Hidden installation costs associated with hardwiring have their own labor and time-to-market considerations.
For example, many industrial robotic cells must be disassembled for shipping and reassembled on site, meaning the machine must be hardwired twice. Additionally, field wiring errors without the proper documentation or wiring identification can cause commissioning delays. Furthermore, on-site testing of the hard-wired systems can be complex and expensive. After installation, reducing downtime caused by unforeseen disruptions or for scheduled maintenance is crucial. When disruptions occur (not if they occur), replacing hard-wired cable can take hours.
Cable assemblies enable “plug-and-play” installation of the dress pack’s electrical components, which saves time and ensures wiring integrity. When you factor in wiring costs, including initial wiring during assembly at the integrator’s facility, and routine maintenance and repairs requiring certified electricians, and all other sources of downtime, those initial savings seen with hardwiring can quickly evaporate. The advantages of “plug-and-play” solutions aid in making dress pack systems easier to ship, assemble, and maintain, while also being more cost-effective over the long term.
10. What other accessories do you recommend for industrial robotic systems? Or what are some common accessories customers use from HELUKABEL to support industrial robots beyond the wires and cables?
Critical spares are a valid consideration for any high-volume production scenario. Having a “safety net” when a dress pack has some sort of failure within the fill package can mitigate extended downtime. Also, spare bulk cables, especially data or smaller gauge I/O type cables, are wise to have on hand. A final suggestion would be to keep a few of the HELUKABEL impact protectors with the quick-clip system in stock. These can be installed to indicate high-wear areas in and around the knuckle. They are also ideal for marrying two dissimilar sections of corrugated tubing when a section needs reworking.
More Information
Cables and Wires for Robotics from HELUKABEL
Related Story
HELUKABEL Group Builds New Facility for Automation Cable Solutions
The HELUKABEL Group, a global cable system solutions provider, announced it is going to build a new facility in Haan, Germany that will house its robotic dress pack and drag chain system subsidiaries under one roof. The new building will also serve as the headquarters of HELUKABEL’s Rhine-Ruhr sales branch, and is planned to be completed by 2025.
Robotec Systems’ core business is robotic dress pack solutions and has been a HELUKABEL subsidiary since 2012 operating out of Duisburg, a suburb of Duesseldorf in northwest Germany. EKD Systems, which recently joined the HELUKABEL Group in the beginning of 2022, specializes in the development and production of cable drag chains made of steel, stainless steel, and plastic. Due to the similarities in both customers and business areas, the corporate group is hoping for considerable synergistic effects from the move to the new location in order to support its global sales network.
The rapid adoption of automated equipment in manufacturing, material handling, and many other industrial sectors, makes providing complementary products and system solutions almost mandatory for manufacturers to remain competitive and sustain growth in an ever-changing supply chain landscape. In addition to its core capabilities as a manufacturer of cables, wires and accessories, HELUKABEL has added to its portfolio over the years to encompass cable assemblies, robotic dress packs, drag chains, cable storage and processing equipment.