Guide to Mechatronics – Part 4: Software & Programming
September 17, 2024
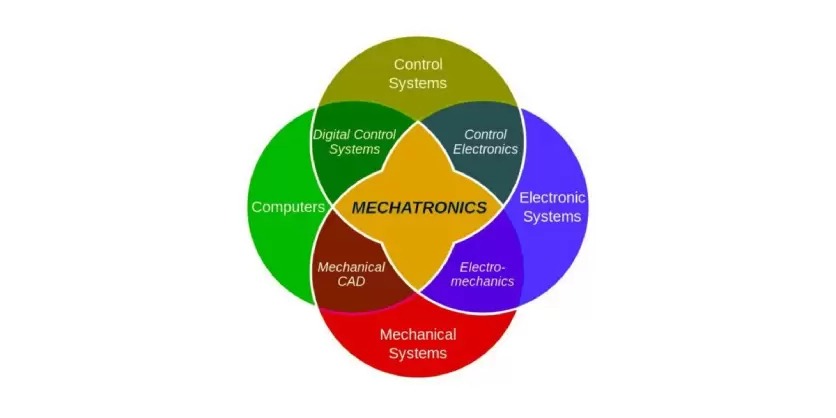
In mechatronics, software plays a pivotal role, acting as the central nervous system that orchestrates and controls the interactions between mechanical and electronic components. The development and implementation of software in mechatronic systems encompass several key areas:
Software’s Role in Control:
Software is integral to controlling mechatronic systems, from simple feedback loops to complex algorithms governing robotic movements.
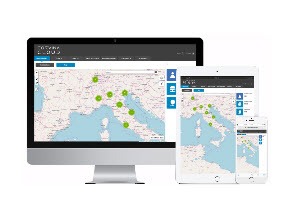
It interprets sensor data, makes decisions based on programmed logic, and sends commands to actuators, ensuring the system responds appropriately to its environment.
- Algorithm Development: Involves creating algorithms that dictate how the system responds to various inputs and conditions.
- Real-Time Control: Software in mechatronics often operates in real-time, requiring rapid processing and response to maintain system stability and performance.
Data Processing:
Software is crucial in processing the vast amounts of data generated by sensors, converting raw data into actionable information. This includes filtering noise, analyzing signals, and executing data fusion from multiple sensors.
- Signal Processing Algorithms: Used to interpret sensor outputs and extract meaningful data.
- Data Fusion Techniques: Combine data from different sources to provide a more comprehensive view of the system’s state.
System Integration:
Software facilitates the integration of various mechatronic components, ensuring they work together harmoniously. This includes managing communication protocols and data exchange between subsystems.
- Interface Management: Ensures different components can communicate effectively, whether through wired or wireless connections.
- Integration Testing: Software is used to test and verify the integration of different components, ensuring they function as intended when combined.
Embedded Systems Programming:
Many mechatronic systems use embedded software, which is directly programmed into the hardware. This software is often highly specialized and designed for efficient performance with limited computing resources.
- Resource Optimization: Embedded systems must often operate with limited memory and processing power, requiring efficient code.
- Hardware-Software Co-Design: Involves designing the software in tandem with the hardware to optimize performance and functionality.
Real-Time Operating Systems (RTOS):
For complex mechatronic systems, an RTOS may be used to manage the execution of software, ensuring tasks are completed in a timely and predictable manner.
- Task Scheduling and Management: RTOS manages the priorities and execution order of various tasks, crucial in systems where timing is critical.
- Reliability and Fault Tolerance: RTOS is designed to be reliable and capable of handling system errors or unexpected conditions gracefully.
Tools and Languages in Mechatronics Software Development
The development of software for mechatronic systems employs a variety of programming languages and tools, each suited to different aspects of the system. The choice of these tools is guided by factors like the system’s complexity, real-time requirements, and hardware specifications.
Programming Languages:
- C/C++: Widely used in mechatronics for their efficiency and control over system resources, ideal for real-time applications and embedded systems. Examples include programming microcontrollers for motor control and robotic arm movement.
- Python: Known for its simplicity and versatility, Python is often used in data analysis, machine learning applications, and prototyping. It is commonly used in vision systems and sensor data analysis.
- MATLAB/Simulink: These are used extensively for modeling, simulation, and algorithm development, especially in the initial design stages. They are particularly valuable in control system design and signal processing applications.
- Java: Used in some mechatronic applications for its portability and robust ecosystem, particularly in networked or IoT-based systems.
- LabVIEW: A graphical programming environment used for data acquisition, signal processing, and instrument control. It is favored in test and measurement applications.
Software Tools:
- Integrated Development Environments (IDEs): Tools like Eclipse, Visual Studio, and Arduino IDE provide comprehensive environments for coding, debugging, and testing software.
- Simulation and Modeling Tools: Software like ANSYS, SolidWorks, and AutoCAD are used for 3D modeling and simulation, crucial in the design and testing of mechanical components.
- Version Control Systems: Tools such as Git and SVN are essential for managing software versions, especially in collaborative projects.
- Real-Time Operating System (RTOS) Platforms: RTOS platforms like FreeRTOS or QNX are used to manage the execution of real-time tasks in embedded systems.
Data Analysis and Machine Learning Libraries: Libraries like Pandas, NumPy, and TensorFlow are used for advanced data analysis and implementing machine learning algorithms.
Use Cases:
- Automated Manufacturing Systems: Use C++ or Java for real-time control and Python or MATLAB for data analysis and machine learning algorithms.
- Robotic Systems: Implement control algorithms using MATLAB/Simulink, with C/C++ for programming the embedded systems that control actuators and sensors.
- IoT Devices in Mechatronics: Utilize Java or Python for managing network communications and data processing.
In the field of mechatronics, the software tools and programming languages chosen must align with the specific requirements of the system being developed. While some languages are suited for low-level, real-time control, others are better for high-level data processing and analysis. The versatility and adaptability of these tools are key to the successful implementation of complex mechatronic systems.
This article is original content created and posted by Electromate. Please do not re-post this content without prior approval from Electromate.
Related Stories
A Guide to Mechatronics – Part 1: Introduction & Fundamentals
A Guide to Mechatronics – Part 2: Composition of a Mechatronic Subsystem
A Guide to Mechatronics – Part 3: Strategies for Integrating Mechatronic Subsystems