Get to Know Omron’s Top Three Trends in Sensor Innovation by Omron
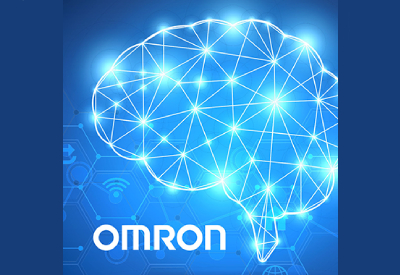
July 11, 2022
At Omron, they are always working to expand the limits of what is possible with sensors. Presence detection – whether through proximity, photoelectric, or fiber optic sensor technology – is crucial for all manufacturing industries, and Omron’s goal is to be able to cover the unique requirements of any application.
Although there are many ways to make progress in sensing technology, they place a premium on three key areas of innovation: smarter sensors, longer sensing distances, and robust, IP-rated technology. In this article, Omron looks at each in turn.
1. They’re making their sensors smarter.
Did you know that sensors can now offer more data besides a simple ON/OFF reading? As Omron continue to expand their already broad sensing portfolio, they’re finding ways to incorporate IO-Link functionality so that users can access the data they need for real-time condition monitoring and better predictive maintenance.
IO-Link lets you pull more data from discrete sensors. If you’re using photoelectric sensors in a weld environment, you’ll be able to see when their light intensity dips below a certain level, indicating lens occlusion. IO-Link-enabled sensors utilize the same internal components as traditional sensors, so access to this additional information comes at no additional cost.
2. They’re offering longer sensing distances.
Long sensing distances are very important for maximizing uptime. When sensors are farther away from the targets, they’re less likely to get damaged. Omron is always striving to achieve stable detection at industry-leasing sensing distances.
Having the option to increase sensing distances is also great for flexibility, since it enables the use of smaller form factor sensors for the same applications and helps address size and layout constraints. Our E2E NEXT proximity sensors, for example, have an exceptionally long sensing distance and are ideal for flexible manufacturing. (They also have IO-Link.)
3. They make sure their sensors are robust.
There’s a lot going on in a typical manufacturing environment, and there are lots of ways that sensors could get damaged. Corrosive chemicals of various types are common in food and beverage washdown environments, while automotive plants feature grease, dust, cutting oil, and weld slag. If any of these things can easily damage your sensors, that’s a big problem.
Fortunately, automation industry leaders like Omron are addressing this issue by designing sensors with high IP ratings that protect against dust and water ingress. Additionally, many Omron sensors are resistant to cutting oil, which is very important given that approximately 30% of unexpected component failures can be traced back to cutting oil.
Interested in learning more about Omron’s trends in sensor innovation? Check our Omron’s sensing technology portfolio by clicking here