Get a Handle on Gripper Technology
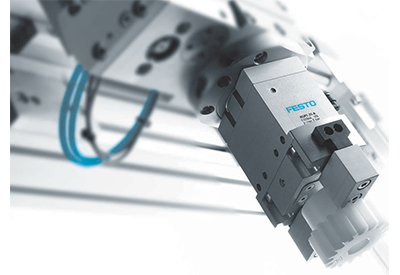
February 3, 2021
From electronics manufacturing to automotive assembly, grippers have become an important part of material handling processes in many industries. Their recent growth is tied to the rise of robotics—including the need for robots to take on specialty tasks and handle increasingly complex workpieces. The result: you now have more grippers to choose from than ever.
So how do you know which gripper is best for your application? Let’s break down some of the key facts and features.
Types of Grippers
Grippers fall into several categories. When it comes to handling applications, mechanical grippers — pneumatic or electric — are the most common. Pneumatic grippers, which make up 90 percent of the market, tend to be more lightweight and cost-effective than their electric counterparts. They also feature higher grip forces, can handle faster cycle rates and are more suitable for harsh environments.
In addition to mechanical grippers, other types include:
Soft and adaptive grippers. These grippers can handle workpieces of various shapes and sizes. Because they don’t have any sharp edges, they can handle food, glass and other delicate objects without damaging or marking the surface. An example is the Festo DHAS Series of adaptive grippers, which is available in lengths of 60, 80 and 120 millimeters—making it ideal for pick-and-place applications in narrow environments, as well as applications involving fragile or irregularly shaped parts.
Vacuum grippers. These grippers, which include suction cups and vacuum generators, can work in small spaces and handle workpieces at high speeds. Because generators often involve high rates of air consumption, you’ll want to look for units that feature energy efficient features. And when it comes to suction cups, consider the nature of your workpiece when selecting the material. Buna suction cups, for example, are ideal for oily or plain workpieces, while Silicon is a good bet for food, as well as hot or cold objects.
Magnetic grippers. This type can handle metallic objects like sheets of metal. Although these grippers are limited to applications involving ferrous metals, they require minimal air consumption to actuate—achieving energy savings up to 90-percent compared to suction cup grippers.
And finally, keep in mind that unique handling applications may require custom gripping devices, which can be made using standard cylinders.