Four Ways to Maximize the Value of Your Safety Interlocks
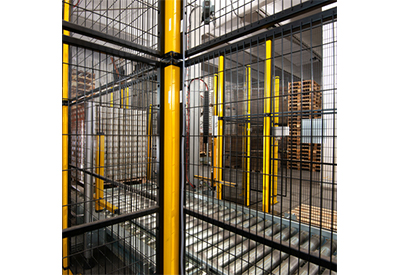
October 27, 2021
Did you know that there are hidden savings in your machine safety devices? Manufacturers often overlook this type of technology in their cost-cutting plans, even though the devices’ proper selection, installation and maintenance can work wonders for the bottom line. In fact, these cost savings go beyond the technology’s primary function of keeping people safe.
Let’s take a look at four things you can do to get the greatest ROI on these devices.
1. Get a risk assessment to make sure you’re getting the right type of safety interlock.
Choosing the right safety interlock for a machine might sound easy, but it shouldn’t be done outside the context of a risk assessment. This ensures that all machine cycle phases have been considered, that the risk level is fully understood, and that the performance level requirements are well known.
To find more information about these considerations, you can refer to ISO 14119:2013 (“Safety of machinery — Interlocking devices associated with guards — Principles for design and selection”). This safety standard offers principles for the selection of interlocks associated with guards and additional guidance to prevent tampering.
2. Install the safety interlocks correctly.
When safety devices aren’t considered during the machine design stage, they can contribute to unplanned downtime, or – in the worst-case scenario – to an accident. This often occurs when an interlock is placed on the wrong side of a machine where it’s easy to manipulate or where it blocks the operator’s view of the process.
Other common mistakes include installing safety interlocks in ways that lead to hazards, such as when they expose actuators or don’t protect them from foreseeable external damage. According to ISO 14119:2013, Clause 5, correctly fastening your interlocks is crucial.
3. Minimize the likelihood that your safety interlocks will be defeated.
Safety device manipulation can lead to serious and potentially fatal accidents in addition to causing unplanned downtime and raising costs. Safety devices on machinery, like safety interlocks, are typically defeated only if they affect the production cycle.
A safety strategy based on a risk assessment should be developed in parallel with the machine design process, so that the selected technology is suitable for the machine type and risk involved and will be installed in a way that prevents tampering. When safety device selection is left to the end of the design process, there’s often a high incentive to defeat it.
4. Avoid fault masking.
Fault masking in one of the least understood potential hazards that can affect the overall performance level of a safety system and make it unsuitable for protecting operators. The term refers to the unintended resetting of the safety system even when using a safety-rated control system.
The risk of fault masking in the conventional series connection of the safety switches restricts the performance level that can be achieved. In some cases, depending on the performance level required, the risk of fault masking and its impact on the diagnostic coverage capabilities makes the solution unsuitable as part of a risk reduction strategy.