Concept Sensors: Engineering the Future Together
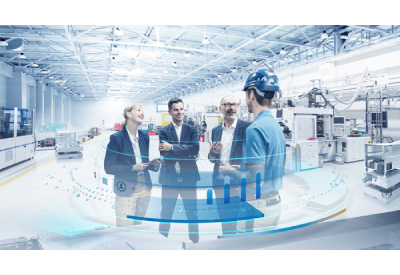
December 8, 2021
New fields of application, new sensor solutions: The digital transformation of industry presents us with new challenges every day. In the development of concept sensors, customers and partners are involved right from the start – in order to make the best possible use of all competencies. But what does that mean for the product development process in concrete terms? Questions for colleagues from research & development, product management and sales.
How does SICK define “concept sensors” and where does this term come from?
Tobias Guettler, Sales: Typically, in development processes, product concepts are created on paper with detailed considerations from a wide variety of perspectives. We, however, value a “hands-on” product concept for our customers and involve them right from the start. This means that important key customers from the industry receive a product that they install and test in their systems, and they give us immediate feedback. The choice of the word “concept sensor” was a conscious decision as opposed to the term “prototype,” because with a concept, we develop a usable product which is quickly available for individual customers in the early development phases. Market and series maturity are secondary factors.
Felix Lang, R&D: We were also inspired by the automotive industry: At the leading trade fairs, the “concept cars” always cause a big stir. They feature the finest technology that cannot yet be mass-produced. The most important thing for car makers is customer feedback! On the one hand, R&D departments always want to push the technology, and what any developer wants most is to see the new technology in actual use. But we at SICK understand that the customer is not necessarily looking for a new product, but for a solution to a problem.
How do ideas for new concept sensors come about?
Maike Syassen, Product Management: When we talk about a technology push, there are always lots of ideas which we are not really comfortable with yet. We work together with the customers on applications that are not yet satisfactory or could be made better with a new approach. What’s needed here is always a good understanding of the application and the market.
Holger Lehmitz, Product Management: The task comes from the customer. Understanding the requirements in detail is very important here. A new approach can then be created from many years of experience from existing applications and new technological concepts.
Lang: A very exciting aspect is the transfer of experience from the production areas at SICK, such as electronic card assembly or fully automatic production lines. We get a lot of inspiration from our own optimization of processes, and customers in turn are very happy with this.
When it comes to dynamic development processes, there is often talk of “accepted failure.” When and why do concept sensor processes fail and how does dynamic development work differ here from the normal process of product development?
Lehmitz: Basically, the motto is: Identify errors as quickly as possible and fix them. Testing early-on in the application is very important here. In addition, both we and the customer have to be precise, open and honest with each other when describing the task to make sure we really list all the constraints. The main difference between dynamic and standard development is certainly the fact that the customer is involved in the process more intensively and at an earlier stage.
Sebastian Berblinger, Product Management: Sometimes we decide not to follow the chosen path to its end for various reasons; for example, because we learn things that make it not worth pursuing this path, or because the desired result can be achieved in a different way. But we always end up with something really new, and that’s the main difference from what we usually do.
Which methods do the concept sensor teams use for this development work and how are the teams structured?
Syassen: We use iterative processes. In the project plans, as in the conventional product development process, we also have milestones at which we decide whether to stop or keep going, but the loops, the iterations, are shorter. And we use dynamic working methods.
Berblinger: Ideally, dynamic work is a huge advantage because we proceed in stages and also get feedback from the market at different points during the process. This is better than completing a large-scale project in the traditional way, only to discover shortly before the end that the development needs to be changed. Dynamic work requires courage, because without courage, nothing new can be created.
Guettler: Studies show that the degree of innovation in companies also correlates with the willingness to take risks. Every single employee, whether from R&D, product management, sales or even management, must work together here.
Lang: These are often people who have special skills, for instance, who anticipate developments and dare to implement something new. We have created our own production area at SICK called the “Speed Factory.” Production planners work to help us develop concept sensors with industrial reliability so that we can hand them over to customers without hesitation and obtain feedback from the market. In the Speed Factory, rapid prototyping processes are used in addition to mastered series processes.