A Basic Guide to the Types of Communication Interfaces Used in Mechatronic Automation
February 26, 2024
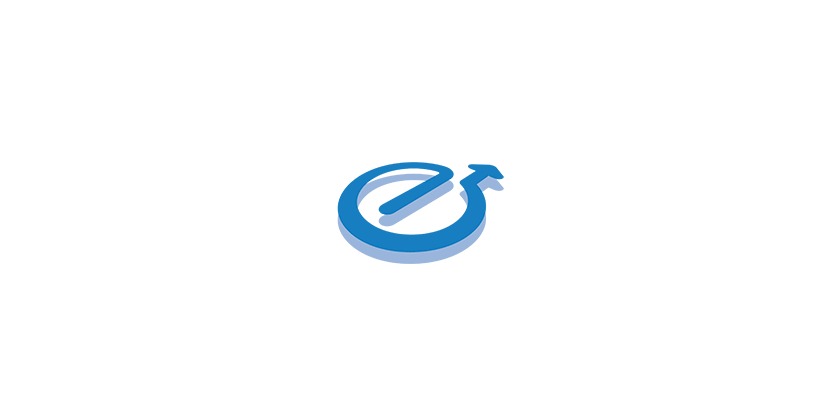
Mechatronic components, such as feedback devices, motors, and drives, often use various communication interfaces to interact with control systems and other devices. These communication interfaces have evolved over time to meet specific needs and standards in the industry. This article explores some of the common communication interfaces and provide a simplified overview of their history, purpose, and usage.
Main Types of Communication Interfaces
- Analog:
- Analog signals are continuous and represent physical quantities as varying voltage or current levels.
- They were one of the earliest communication methods used in mechatronics for basic control and feedback.
- Analog signals are still used when precision is not a primary concern, and simplicity is preferred.
- SSI (Synchronous Serial Interface):
- SSI is a digital interface used for position and speed feedback in rotary and linear encoders.
- It provides accurate and noise-resistant data transmission.
- SSI is widely used in applications where high precision is required, like CNC machines.
- RS (Recommended Standard):
- RS is a series of serial communication standards like RS-232, RS-485, and RS-422.
- They have been used for decades for various applications, including data transmission between computers and peripherals.
- RS-485 is commonly used in industrial settings due to its robustness in noisy environments.
- Modbus:
- Modbus is a popular protocol for serial communication between industrial devices.
- It’s simple and widely supported, making it a standard for connecting various devices in industrial automation.
- CAN (Controller Area Network):
- CAN is a robust and efficient serial communication protocol initially developed for the automotive industry.
- It’s widely used in mechatronics for real-time control and data exchange due to its reliability and high data rates.
- DeviceNet and CANopen:
- These are higher-level protocols built on top of the CAN bus.
- DeviceNet focuses on connecting industrial devices in a network, while CANopen provides a more standardized way to communicate with devices on the CAN bus.
- Ethernet:
- Ethernet is a widely used networking technology that provides high-speed communication.
- Ethernet is increasingly used in mechatronics to connect various devices and components in industrial settings.
- EtherCAT:
- EtherCAT is an Ethernet-based real-time communication protocol designed for automation and control systems.
- It offers low latency and high-speed communication, making it suitable for demanding applications.
- Ethernet/IP:
- Ethernet/IP is an industrial communication protocol that uses standard Ethernet hardware and the Common Industrial Protocol (CIP).
- It enables seamless integration of industrial devices into an Ethernet network.
- PROFIBUS and PROFINET:
- PROFIBUS is a widely used fieldbus communication protocol, while PROFINET is its Ethernet-based counterpart.
- They are popular in automation and process control systems, with PROFINET providing faster communication and greater flexibility.
- USB:
- USB (Universal Serial Bus) is a common interface for connecting various peripherals to computers.
- In some mechatronic applications, USB is used for configuration and data transfer to and from devices.
The reason for having many communication types is the diversity of mechatronic applications and the need for different levels of performance, reliability, and compatibility. Industries and applications have specific requirements, leading to the development of various communication standards over time. Choosing the right communication interface depends on factors such as data speed, distance, noise immunity, and compatibility with existing systems.
Communication Interface Comparison Chart
Communication Interface | OSI Model Layers | Data Rate (Typical) | Topology | Message Format | Error Detection | Master-Slave Model | Data Types Supported | Addressing | Security Features | Common Applications |
Analog | Physical Layer | N/A | N/A | Continuous Voltage/Current | N/A | N/A | Analog Signals | N/A | Limited | Basic Control, Sensor Feedback |
RS-232 | Physical Layer | Up to 115.2 kbps | Point-to-Point | Serial Frames (Binary) | Parity, CRC | Master-Slave | Binary, ASCII, Custom Formats | Device IDs | Limited | Legacy Serial Communication |
RS-485/RS-422 | Physical Layer | Up to 10 Mbps | Multi-Drop | Serial Frames (Binary) | CRC | Master-Slave | Binary, ASCII, Custom Formats | Node IDs | Limited | Industrial Automation, Building Control |
SSI | Data Link Layer | Varies | Point-to-Point | Binary | CRC | N/A | Binary | Device IDs | Limited | CNC Machines, Precision Positioning |
CAN | Data Link Layer | Up to 1 Mbps | Multi-Drop/Bus | Frames (Binary) | CRC | Master-Slave | Binary | Node IDs | Limited | Automotive, Industrial Automation |
Modbus (RTU) | Data Link Layer | Up to 115.2 kbps | Multi-Drop/Bus | Binary | CRC | Master-Slave | Binary, ASCII | Slave IDs | Limited | SCADA, PLCs, Industrial Automation |
Modbus (TCP/IP) | Transport Layer | Up to 1 Gbps | Ethernet Star/Bus | TCP/IP | CRC | Master-Slave | Binary, ASCII | Slave IDs | Limited | Industrial Ethernet, SCADA, HMI |
DeviceNet | Data Link Layer | 500 kbps to 5 Mbps | Bus | Binary | CRC | Master-Slave | Binary | Node IDs | Limited | Industrial Networking, Device Communication |
CANopen | Data Link Layer | Up to 1 Mbps | Multi-Drop/Bus | Frames (Binary) | CRC | Master-Slave | Binary | Node IDs | Limited | Industrial Devices Communication, Machine Control |
PROFIBUS | Data Link Layer | Up to 12 Mbps | Bus | Frames (Binary) | CRC | Master-Slave | Binary, ASCII | Node IDs | Limited | Factory Automation, Process Control |
PROFINET | Data Link Layer | Up to 100 Gbps | Ethernet Star/Bus | Ethernet Frames | CRC | Master-Slave | Binary, ASCII | Node IDs | Enhanced | Industrial Ethernet, Real-time Control |
Ethernet | Data Link Layer | Up to 100 Gbps | Ethernet Star/Bus | Ethernet Frames | CRC | N/A | Binary, ASCII | MAC Addresses | Enhanced | General Networking, Industrial Applications |
EtherCAT | Data Link Layer | Up to 100 Gbps | Ethernet Bus | Ethernet Frames | CRC | Master-Slave | Binary, ASCII | Node IDs | Enhanced | Real-time Control, Motion Control, Automation |
Ethernet/IP | Data Link Layer | Up to 1 Gbps | Ethernet Star/Bus | Ethernet Frames | CRC | Master-Slave | Binary, ASCII | MAC Addresses | Enhanced | Industrial Ethernet, Integration with PLCs |
USB | Physical Layer | Up to 10 Gbps | Point-to-Point | Packets (Binary) | CRC | N/A | Various Data Formats | Device IDs | Enhanced | Consumer and Industrial Device Connectivity |
Timeline of Communication Interfaces in Mechatronics
The order in which communication interfaces and protocols were introduced is not entirely linear, as multiple developments often occurred concurrently. However, this is a rough chronological overview of some of the major developments in mechatronic communication interfaces:
- Analog – As one of the earliest forms of communication, analog signals have been used for many decades.
- RS (Recommended Standard) – The RS series, including RS-232, RS-485, and RS-422, dates back to the mid-20th century.
- SSI (Synchronous Serial Interface) – Introduced in the late 20th century, SSI became popular for precise position and speed feedback.
- CAN (Controller Area Network) – Developed by Bosch in the 1980s for the automotive industry and later adapted for industrial applications.
- Modbus – Introduced in the late 1970s, Modbus has been widely used in industrial automation.
- DeviceNet – Developed in the late 1990s as an extension of the CAN bus for industrial networking.
- CANopen – Similar to DeviceNet, CANopen also emerged in the late 1990s as a higher-level protocol for CAN-based communication.
- PROFIBUS – Introduced in the late 1980s as a fieldbus communication standard.
- PROFINET – PROFINET, the Ethernet-based counterpart of PROFIBUS, became prominent in the 2000s.
- Ethernet – Ethernet technology has been around since the 1970s but started to gain traction in industrial automation during the 1990s.
- EtherCAT – Developed in the early 2000s, EtherCAT brought high-speed, real-time Ethernet communication to industrial applications.
- Ethernet/IP – Became prominent in the 2000s as an industrial communication protocol based on standard Ethernet hardware.
- USB – Introduced in the mid-1990s for connecting various peripherals to computers and later adapted for some mechatronic applications.
It’s important to note that while these protocols and interfaces were introduced in specific time periods, their adoption and widespread use in various industries might have occurred at different rates. Additionally, new versions and updates of these protocols continue to emerge to meet evolving industry needs. The choice of a communication interface often depends on factors like industry standards, compatibility, and application requirements.
Obsolescence and Evolution with Mechatronic Communication Interfaces
The replacement or obsolescence of communication interfaces in the mechatronic industry is not always straightforward, as different interfaces serve different purposes and continue to coexist for various applications.
However, here are some examples of how newer technologies have sometimes replaced or supplemented older ones:
- Analog:
- Analog signals are still used in many applications where simplicity and cost-effectiveness are more important than precision.
- They have not been replaced but are less common in applications requiring high accuracy.
- RS (Recommended Standard):
- RS-232, which is widely used for serial communication between computers and peripherals, has been largely replaced by USB for consumer devices due to its higher data transfer rates and ease of use.
- RS-485 and RS-422 are still used in industrial settings where longer-distance communication and noise immunity are required.
- SSI (Synchronous Serial Interface):
- SSI remains a popular choice for high-precision position and speed feedback in mechatronic systems, and it hasn’t been replaced by a single alternative.
- CAN (Controller Area Network):
- CAN has become a standard in automotive and industrial applications but has not been fully replaced by other technologies.
- Higher-speed versions of CAN (e.g., CAN-FD) have evolved to meet increased data rate requirements.
- Modbus:
- Modbus is still widely used in industrial automation but has seen competition from Ethernet-based protocols like EtherCAT and PROFINET.
- DeviceNet and CANopen:
- These protocols have been used alongside CAN and have not necessarily replaced it, but they offer higher-level communication and network configuration capabilities.
- PROFIBUS and PROFINET:
- PROFINET, being Ethernet-based, has largely superseded PROFIBUS in new installations due to its higher data rates and flexibility.
- Ethernet:
- Ethernet has become a prevalent choice for industrial communication, supplementing or replacing older fieldbus technologies.
- In some cases, Ethernet has replaced older proprietary networking solutions.
- EtherCAT:
- EtherCAT has gained popularity as a high-speed, real-time Ethernet alternative and has been adopted in applications where traditional Ethernet might not meet the required performance criteria.
- Ethernet/IP:
- Ethernet/IP is an industrial protocol that uses standard Ethernet hardware, offering compatibility with existing Ethernet infrastructure while adding industrial-specific features.
- USB:
- USB has replaced older serial communication interfaces like RS-232 for connecting consumer devices to computers.
The replacement or obsolescence of communication interfaces depends on factors such as technological advancements, industry standards, data transfer rates, noise immunity, and application requirements. Many interfaces continue to coexist and find their niche in various applications within the mechatronic industry. The choice of which interface to use often depends on the specific needs and constraints of the application in question.
In the dynamic landscape of mechatronic communication interfaces, there is no one-size-fits-all replacement or obsolescence pattern. Rather, the evolution of these interfaces reflects the industry’s continuous quest for improved performance, efficiency, and compatibility.
Analog signals persist for their simplicity, while newer digital protocols like Ethernet-based solutions offer higher data rates and enhanced capabilities. The choice of which communication interface to use remains a nuanced decision, influenced by application requirements, industry standards, and technological advancements.
As mechatronic systems continue to advance, a diverse range of communication options ensures that each component can be effectively integrated into a wide array of applications, ultimately driving innovation and efficiency in the field of automation and control.
More Information
Related Story
A Guide to Encoder Types in Mechatronic Automation
Encoders are pivotal sensor components in mechatronic automation, converting mechanical motion into an electrical signal that can be interpreted for precise control and positioning of mechanical parts. This article explores various encoder types, focusing on their unique components, advantages, and applications.