Heavy Payload Cobots vs Traditional Robots for Industrial Automation
May 1, 2024
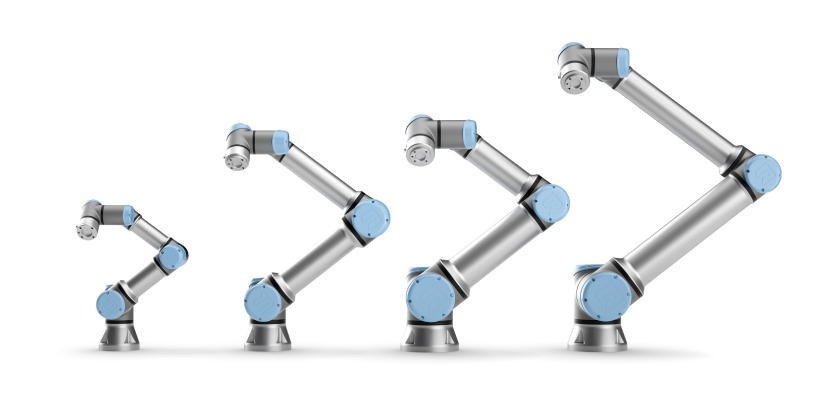
Adopting collaborative robots (cobots) represents a significant shift in automation strategies. Universal Robots is a frontrunner in the cobot sector and delivers solutions that are transforming industrial automation. This discussion provides detailed reasons why Universal Robots’ cobots are ideal for most industrial automation applications.
Rapid Deployment of Universal Robots Cobots
Universal Robots’ e-Series cobots are engineered for rapid deployment, going operational within weeks instead of months. These cobots are designed to fit into existing production environments with minimal modifications. They also feature plug-and-play capabilities, allowing for immediate connection to various production systems and compatibility with a wide range of accessories and end-effectors.
The programming of e-Series cobots is streamlined through the PolyScope Graphical User Interface, which offers intuitive touch commands and visual guides. This user-friendly interface is complemented by ready-to-use functions with customizable presets for common tasks.
Universal Robots ensures ease of operation and programming training through its Universal Robots Academy. This online platform provides comprehensive, free learning modules covering everything from basic operations to advanced programming, accessible without extensive prior training.
Programming Universal Robots (UR) Cobots
Universal Robots designed their cobots for user-friendliness, ensuring businesses across various industries can easily program and deploy. This accessibility is due to the PolyScope graphical user interface. The PolyScope interface promotes clarity and simplicity, allowing operators to program tasks through intuitive drag-and-drop actions and touch commands. This approach reduces the learning curve compared to traditional robot programming and supports real-time task adjustments.
UR cobots effortlessly switch between tasks and adjust operational pace to meet diverse production needs without manual reprogramming. The capability to store multiple task programs and the ease with which operators can switch between them enhances the scalability of these cobots. They are designed to grow alongside your business, adapting to new tasks and expanding capabilities as operational needs evolve.
UR cobots are not confined to any specific sector. They can be quickly programmed to perform precision tasks in electronics manufacturing, manage heavy lifting in automotive assembly, or handle delicate operations in the pharmaceutical industry. This adaptability, combined with straightforward programming, reduces the typical time and resources required for robotic automation, making advanced robotic technology accessible to companies of all sizes and technical capabilities. This democratization of access helps businesses optimize their production processes, swiftly adapt to market changes, and seize new growth opportunities.
Universal Robots Cobots’ Payload Capacity
Universal Robots’ cobots, particularly the UR20 model, exemplify a blend of adaptability, user-friendliness, and the capability to handle heavy-duty tasks. The UR20 stands out with a payload capacity of up to 20 kg (44.1 lbs) and an arm reach of 1750mm (68.9 in), making it suitable for a variety of industrial applications including palletizing, material handling, packaging, welding, and machine tending. Despite its capacity to carry significant weight, this cobot maintains precision and reliability in task execution, ensuring operations are consistently performed with accuracy.
The design of the UR20 extends its use to industries requiring the handling of heavier items found in food & beverage production, metal manufacturing, automotive assembly, and logistics. By undertaking physically demanding tasks, these cobots enhance workflow efficiency, reduce the risks associated with manual labor, and increase production throughput.
Universal Robots’ high-capacity cobots challenge the notion that collaborative robots are only suitable for light tasks. Capable of significant lifting and maneuvering, these cobots are invaluable in a broad range of industrial settings. Additionally, they retain the same ease of programming and flexibility as their lighter counterparts, allowing for seamless integration into existing production lines without extensive reconfiguration or downtime.
Versatility and Adaptability of Universal Robots Cobots
Universal Robots’ cobots are designed for versatility and adaptability, making them highly suitable for integration into diverse production environments. Their compact and lightweight construction allows them to fit seamlessly into tight spaces on production lines. This feature reduces downtime and facilitates quick adjustments to production setups.
These cobots can perform a broad range of tasks, from precise assembly to consistent painting, making them invaluable across various stages of manufacturing. The straightforward design of the cobots also allows for easy adjustments. This adaptability ensures that production lines can continuously improve without the need for new robotic investments.
Universal Robots+ Ecosystem
Universal Robots holds over 65 patents and has garnered more than 35 global awards. This commitment to innovation ensures that businesses using UR cobots remain at the cutting edge of technology. The UR+ ecosystem enhances this advantage by offering a comprehensive suite of compatible third-party end-effectors, accessories, and software solutions.
The UR+ platform significantly increases the utility of UR cobots by ensuring compatibility with a broad range of third-party accessories and software. This facilitates the setup and expansion of automation capabilities across various applications. The ecosystem includes a diverse array of solutions like gripping, sensing, and vision systems, allowing users to tailor cobot functionalities to the exact needs of different operations, ensuring optimal configuration.
Universal Robots’ UR+ ecosystem represents the company’s dedication to making robotic automation accessible and flexible. By providing an open platform that fosters innovation and compatibility, Universal Robots ensures businesses can fully leverage the potential of collaborative robotics to boost their competitive edge.
Transition to Automation with Universal Robots: A Step-by-Step Guide
Adopting Universal Robots’ cobots is a strategic move towards embracing automation that’s straightforward, adaptable, and scalable. Here’s a concise guide to integrating these advanced tools into your production processes, ensuring you leverage their full potential to enhance your operations.
Step 1: Identify Automation Opportunities
- Assessment: Evaluate your production line to identify tasks that are repetitive, physically demanding, or prone to human error. These are ideal candidates for automation with cobots.
- Consultation: Utilize Electromate for expert advice on potential automation opportunities.
Step 2: Choose the Right Cobot
- Selecting a Model: Based on the payload, reach, and the specific tasks identified, select a cobot model that best suits your needs. Models range from the UR3e for light, precise tasks up to the UR30 (coming soon) for tasks requiring a higher payload.
- UR+ Ecosystem: Consider the end-effectors and accessories available through the UR+ platform that could enhance the cobot’s functionality for your specific applications.
Step 3: Plan for Integration
- Layout Planning: Determine the cobot’s placement on the production floor, considering workflow, safety, and ease of interaction with workers.
- Safety Assessment: Although cobots are designed to work safely alongside humans, conduct a risk assessment to ensure all safety considerations are addressed, adapting safety measures as needed.
Step 4: Installation and Programming
- Setup: Follow the simple setup instructions for installing the cobot. Thanks to their design, UR cobots can be up and running in a matter of hours.
- Programming: Utilize the PolyScope GUI for programming. The interface is intuitive, and with Universal Robots Academy, your team can quickly learn to program and reprogram tasks as needed.
Step 5: Training and Operation
- Operator Training: Ensure operators are trained on the cobot’s operation, making full use of the Universal Robots Academy’s free online training resources.
- Deployment: Begin with simpler tasks to gain confidence and understanding of the cobot’s capabilities, gradually expanding to more complex applications.
Step 6: Evaluate and Expand
- Performance Monitoring: Regularly review the cobot’s performance and the impact on production efficiency, quality, and worker satisfaction.
- Scalability: As your familiarity with cobot technology grows, explore additional applications and consider expanding your cobot fleet to further enhance productivity and innovation.
Choosing Universal Robots as your automation partner opens the door to a range of possibilities for enhancing efficiency, product quality, and workplace safety. By following these steps, you can smoothly transition to automation, ensuring your business remains competitive in the dynamic landscape of modern manufacturing. Experience the future of industrial automation with Universal Robots.
More Information
Related Story
Electromate Announces Pre-Order Availability of Universal Robots’ New UR30 Cobot
Electromate Inc., a leading Distributor of Precision Robotic & Mechatronic Solutions, is excited to announce the pre-order availability of Universal Robots’ latest innovation – the UR30 collaborative robot (cobot). The UR30, boasting a 30 kg payload capacity, is the newest addition to Universal Robots’ cutting-edge cobot lineup.