Building a Smart Factory Requires a Smart Approach
The Truly Connected Factory
August 21, 2023
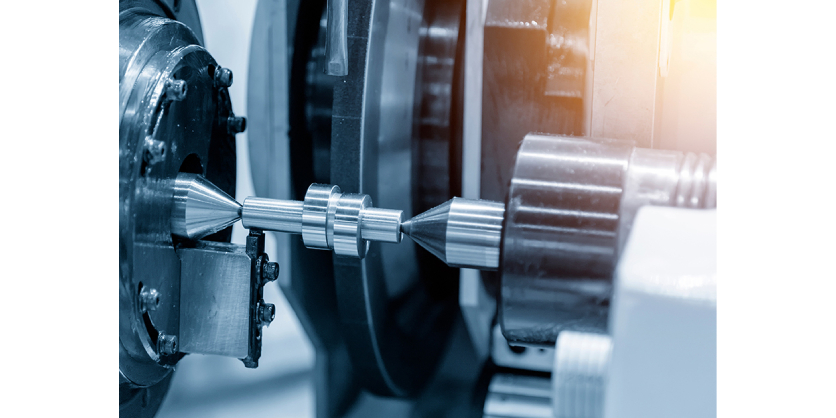
By Lucas Hale – Global Marketing Manager
The truly connected smart factory. Over the past decade, new technologies have increasingly permeated the factory floor. Automation, always a part of manufacturing, has quickly escalated thanks to ever increasing computer processing power and data storage. At the same time, technologies such as artificial intelligence, the Internet of Things connectivity, cloud computing, big data analytics, 3D printing, and many others that were previously complex to install and configure have become affordable and scalable. They too have found their way into industrial applications.
This rapid acceleration of digital transformation has been termed Industry 4.0—the Fourth Industrial Revolution. A major outcome of this period has been that the truly connected factory, or smart factory, is a reality. As more machines begin to communicate with each other, productivity increases. Gains in efficiency, using analytical tools that can predict maintenance needs, improve it even more. But the real benefits of a smart factory are far beyond mere productivity. It provides the ability to predict and adjust to changes, both internal and external, to offer unprecedented agility and flexibility, and create real competitive advantages for a business.
It’s about seeing as much as doing
While it’s easy to see how automation increases productivity by speeding up processes, streamlining product movement between machines, and reducing errors, the real benefits of a smart factory come from a far broader concept.
Smart factories offer complete transparency by integrating machines, processes, and people into a single, digitally connected system. Sensors feed data from every element of the manufacturing process all the time, so the information reflects current conditions. It’s then integrated with data from suppliers and customers to create a holistic view of upstream and downstream supply chain processes.
This means any change from the expected can be instantly recognized and acted upon. Whether it’s a difference in the availability of raw materials, a bottleneck in production, a shift in market demand, or an infinite number of other variables. And, of course, any necessary changes can be actioned either by human intervention or by autonomous decision-making.
The power of prediction
The ability of the smart factory to predict future outcomes based on historical and real-time data offers benefits in all sorts of ways. From anticipating issues with inventory, to predicting quality problems, to monitoring areas of safety concern.
One significant opportunity offered by smart factories is predictive maintenance. Until now, organizations had to choose between maximizing the life of a part at the risk of it failing and causing machine downtime or incurring the cost of replacing parts early, perhaps unnecessarily.
Predictive maintenance means, data gathered from connected, smart machines enables accurate prediction of when and where failures could occur, maximizing the life of parts and minimizing unnecessary downtime.
The silver lining of the cloud
The pandemic has only accelerated the use of cloud applications around the world. The ability to access information from anywhere to make informed decisions is a substantial component of the smart factory.
With data gathering at the very heart of smart factory procedures, utilizing the cloud is fundamental to its operation. Using a cloud service provider (CSP) removes the need to invest in on-site server infrastructure, maintenance, and IT staff.
The benefits include unlimited scalability, making it easy to grow without the need for additional infrastructure. Cost is usually tied to consumption, so you’re only paying for what you use. And the CSP is responsible for updating and maintaining the operating systems.
While some people are concerned about security, the fact is that a reputable CSP is going to have much greater resources to put into cybersecurity to protect your data in its cloud than you could ever hope to have in an on-site system.
The benefits of being smart
A smart factory can optimize the use of every asset. It should result in lower downtimes, greater capacity, reduced changeover time, and more.
Detecting quality defects faster and identifying the cause, results in lower scrap rates and lead times, as well as better quality products.
Just about every benefit of running a smart factory is likely to lower costs, increase efficiency, expand optimization, establish more predictable inventories, improve predictive maintenance, and so on.
There will also be benefits for both the environment and staff. Operational efficiencies may result in a smaller environmental footprint, while a reduction in the potential for human error should reduce the likelihood of industrial accidents.
It’s also worth acknowledging that likely changes in labor markets means moving towards a smart factory operation can insulate you from a potential skills shortage in the future.
Step by step
While the technology for building a true smart factory certainly exists today, it’s unnecessary to change everything at once. In fact, an important attribute of the connected factory is that it’ll continue to evolve as technology and requirements change. Build it incrementally, adding elements as you can. And ensure that you adapt the system to suit your business, not the other way around.
The ANCA Integrated Manufacturing System (AIMS) is a modular manufacturing system that lets you add automation to one specific process or build an entirely connected production line. Custom built to your needs, it connects machines and processes to maximize productivity, improve quality, and free operators from doing simple tasks so they can be redeployed to more valuable projects.
Everything is controlled by an AIMS server, which manages data flows and machine programs, displays real-time machine activity and continuously gathers production data.
Smart move
Investing in smart factory capability, at whatever speed, makes sense for your business, it really is inarguable. The benefits of agility, connectedness, and transparency are essential to enable you to function more effectively and efficiently in an ever-increasingly complex and rapidly shifting market.
Related Story
ANCA to Exhibit at EMO 2023
CNC grinding technology pioneer ANCA will showcase their latest products and industry-specific grinding and automation solutions at EMO at Booth F52, Hall 6 in Hanover, Germany in September. The eagerly awaited winner of the renowned Tool of the Year competition will be announced live Wednesday, September 20th at 4.30pm (GMT) – and all are welcome to join the celebrations and witness for themselves the ultimate range of cutting tools.