How Industrial Ethernet Shapes the Industrial Transformation – A Review
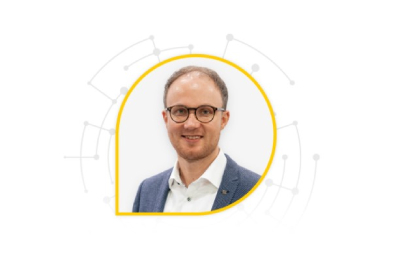
February 17, 2022
February 17
By Krystie Johnston
The vision of seamless communication between the cloud right down to every sensor is manifesting – and IIoT is becoming more and more of a reality. Joachim Finke, Head of PM Network Interface Connectors at HARTING explains how Ethernet empowers the IIoT. Mr. Finke explains how industrial Ethernet shapes the industrial transformation by exploring the success of industrial Ethernet over the last few years and discusses the needs of the digital transformation. He also questions whether existing technologies are enough to cope with those requirements. Finally, he discusses new technologies that are certain to shape the future of the industrial transformation. His presentation, At a Glance – How Industrial Ethernet Shapes the Industrial Transformation, was presented at HARTING Industrial Week, 2022.
The Ethernet – not the industrial Ethernet – just the Ethernet, originated in Hawaii in 1970. Dr. Abramson wanted to create a cost-efficient way to communicate between the University of Honolulu and the islands surrounding it, so he found a way to transmit data packages using two frequency bands and a random mode for collision avoidance. Essentially, he created the first wireless data network, or the start of the Ethernet. In 1983, the Institute of Electrical and Electronics Engineers, or IEEE, took it further than imagined. An explosive performance growth occurred when the 10 Megabit standard was made.
In 1995, the 100 Megabit was introduced. And this was important because for the first time, switching technologies, duplex data, communication modes, and the prioritization of packages was possible. Furthermore, avoidance of data collision was guaranteed. This was groundbreaking and allowed for the realization of the industrial Ethernet over the next few years. It was not long before 1 Gigabit was possible (1999), then 10 Gigabit (2006), then 25/40 Gigabit (2010), then 200/400 Gigabit (2017), and so on, driven by data needs from individuals, the private sector, and data centre needs all over the world. This growth was accelerated by changing from copper cabling to fiber optics. Companies began to use the IEEE Ethernet for industrial networks to connect sensors and drives and other components to build networks. They used it to make use of the high data rates and bandwidths, and the seamlessly unlimited number of network participants inside the machine.
“They used it to have an overall transmission control protocol, or TCP-based communication from the enterprise level of the automation pyramid down to the control level and the field level. This was revolutionary because switching technology, full duplex data transmission, and the messaging privatization is critical for use in the industry. The same progression happened for FIELDBUS systems – in reality, there is not one single industrial Ethernet across the whole world, there are ethernet-based protocols like PROFINET, or EtherCAT, or CC Link, and all the different protocols we know very well. Now, roughly 20 to 25 years later, Ethernet has truly penetrated the industrial market. For example, the machinery and automation market have different applications. IP20 inside the cabinet has switches, and converters, all typically based on the Ethernet. Outside the cabinet, there are HMIs, sensors, actuators, I/O, and more. We know that a lot of these devices are based on Industrial Ethernet communications – regardless of which protocol it is.”
The robotic market is the same as well. Although the market looks a little different, the applications within are typically the same. There are sensors and tools at the robot flange, there are components that go from the flange to the foot of the robot where the Ethernet cabling is contained. There are servo drives inside, and there is a control unit – all of which are typically based on industrial ethernet. The transportation market it is the same as well. There are wireless access points and IP cameras, even the safety-relevant communication tools are starting to, or already have, switched to Ethernet communication.
This means Ethernet has really become very big in many industrial applications. In fact, in the last 20 to 25 years, a fast development has taken place: 65% of factory automation is based on industrial Ethernet, 28% is still based on traditional FIELDBUS systems, and a small, 7% is based on wireless communication technologies. Looking at the applications themselves inside of the factory, the standard Ethernet is dominating. In the production world, the different Industrial Ethernet-based FIELDBUS protocols are dominating, and the last third of traditional FIELDBUS systems are at the sensor and actuator level. This makes the communication very complex, because all these different protocols and technologies must be connected by gateways. Specific people are required to change a sensor or add functions, and that can be a difficult thing to do.
“If we look at the performance of a company and their usage of digital technologies, one thing is clear: companies would like to use the new digital tools to become more productive, to create new offerings, and to create new business models. This is interesting to see, because, on the one hand, digitalization offers a very big chance, on the other hand, it also offers a very big risk, because, if you take it right, you can develop, if you miss a trend, there is a risk that you lose.
This is a unique challenge with the digitalization of the industry, beside everything, one thing is clear, and this I always heard from whatever machine builder I have visited during the last couple of years, ‘The access to the field data is the most important thing – it is key for the digital transformation in the company.’” Finke says.
The balance depends on many different factors, like the products a company offers and the size of the company itself. Some products are more suitable for digital services. Some companies are not large enough to adopt digitalization. To make adoption of digitalization more feasible, several factors need to be considered. Take a complete production hall, for example, with many different machines making big parts on a global scale. The automation structure has many different machines, all of which work and communicate within themselves, and at times, with each other. If they all speak different languages, there needs to be a translator, or gateway, so that everyone is speaking the same language. Another factor to consider is their speed and performance within the network, since some devices are using industrial Ethernet, others are using FIELDBUS or other protocols.
If autonomous operation is the goal, there will need to be something done to address these factors. Finke believes semantics are important and says that vendor-independent communication between machines is needed. He refers to this as horizontal communication. Vertical communication refers to the data that is gathered from the devices, such as sensors and actuators. This information would benefit from semantics as well, so it can provide standardized meaning about the data it has collected. Again, this could be solved with vendor-independent communication. This semantic today is not existing at all between the different protocols.
Finke points out, “We need to change some things in a way that companies today are working together. Let’s call it co-opetition. Competitors who work together, to, at the end of the day, reach something that is great for the overall industry. Everybody knows about OPC UA; it is the communication technology, not just about the protocol. It is the communication technology that can realize the vendor-independent communication between the horizontal (I.e., between the machines). This is not new: over 85% of today’s existing industrial automation companies produce and develop products according to OPC UA.
What is new is the data of the field level has very significant importance for the digital applications, and the OPC UA field level communications initiative worked on an OPC UA standard for the vertical communication (I.e., down to the machine). This is called OPCUA FX, or field exchange. Together, with standard OPC UA, in a few years, we can reach a vendor-independent communication between all different levels – between the horizontal and the vertical. It is not just a protocol like PROFINET or EtherCAT, it is much more. OPCUA and OPCUA FX really describe the meaning of the information all the different sensors are collecting. It is semantic.”
To summarize, seamless communication is transforming industries, but it will not happen overnight. Vendor-independent communication and semantics down to the machine and between machines will assist with the goal autonomous operation to be realized. HARTING presents the big picture of new technologies that will really shape the next couple of years.
For more insights, watch the entire presentation on YouTube by clicking here