ABB Robots Boost Productivity at Nestlé’s Brazilian Plants by Over 50 Percent
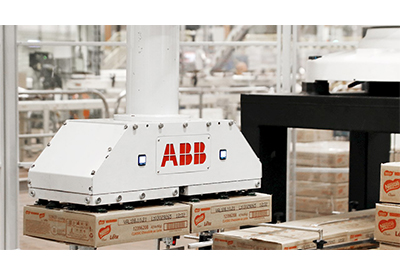
March 25, 2021
ABB robots are supporting Nestlé to improve the productivity of pallet loading in its chocolate manufacturing facilities in Brazil by 53 percent, using a new ABB palletizing robot solution.
While the company currently uses ABB Robotics palletizing solutions, the latest requirement was for a more compact cell that could fit into a smaller area and easily be replicated at other sites. An important requirement was for the robot to safely interact with employees, who occasionally need to enter the palletizing area to speed up pallet changes. ABB’s new, compact robotic palletizing cell, co-developed by ABB and Nestlé’s engineering team, features an ABB IRB 660 robot with a suction gripper head to move boxes from the end of the production line to the pallet, stacking them accurately to ensure a balanced load, while SafeMove technology enables safe intermittent collaboration between the robot and production line workers.
“Food and beverage manufacturers like Nestlé increasingly need more flexibility on their production lines to enable them to adapt to changing consumer tastes and demands, allowing their employees to collaborate intermittently with robots in their production centers. At the same time, they require higher levels of productivity and efficiency while maintaining the highest levels of product quality,” said Sami Atiya, President of ABB Robotics & Discrete Automation. “Collaborative robot technologies like SafeMove help us deliver on all of these requirements, and by removing the need for extensive fencing, enable us to bring automation to smaller spaces, anywhere on the production line.”
{videobox}DBHLQ95afJg{/videobox}
SafeMove, ABB’s robot monitoring software, detects movement and restricts a robot’s speed, motion and position when a person comes near. This allows large industrial robots to work safely and reliably alongside people, without the need for fences, safety switches, doors and locks.
At Nestlé’s Caçapava factory, the use of SafeMove instead of fences resulted in an approximately 30 to 40 percent smaller footprint compared to previous ABB cells at the Nestlé site.
The new installation has been so successful that it has now been installed in three other Nestlé factories in Brazil, with 13 palletizing cells already in operation and further installations and commissioning underway. Financial details of the contract were not disclosed.
Michey Piavantinha, Plant Director for Nestlé Caçapava, said: “Thanks to the partnership with ABB, it has been possible to develop solutions that make our manufacturing process more agile and efficient, ensuring that our products continue to have the same high level of quality and excellence that make the Nestlé brand successful.”
To demonstrate to the customer how the finished cell would work before installation, ABB used its RobotStudio® software to simulate the complete solution in a virtual environment, including showing the cycle time for the robot’s operations. This ensured a shorter implementation time and avoided any failures that might occur in the start-up process.
Nestlé in Brazil supplies a range of confectionery to South and Central America and Canada and the company’s Caçapava site is the largest Nestlé Kit Kat factory in the Americas.