A Guide to Mechatronics – Part 2: Composition of a Mechatronic Subsystem
July 3, 2024
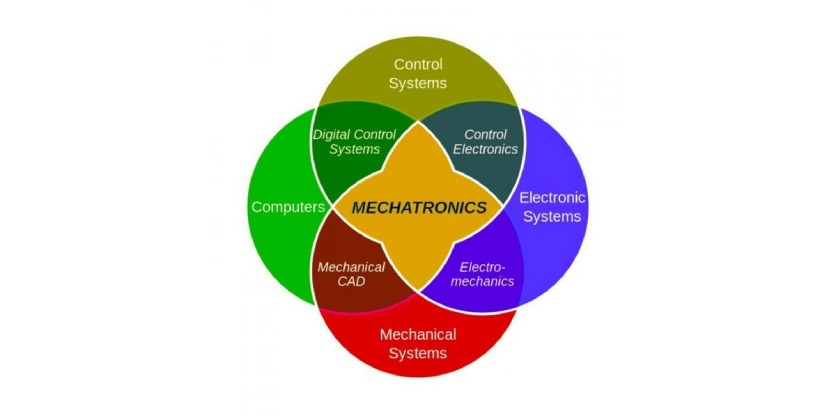
Sensors and Actuators
Sensors: Sensors are the eyes and ears of mechatronic systems, providing vital data about the environment and the system’s internal state. They come in various types, each suited for specific applications:
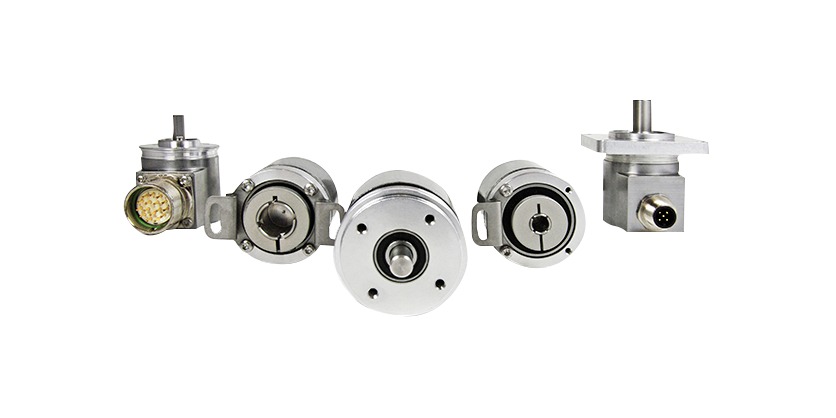
- Position Sensors: These include potentiometers, linear variable differential transformers (LVDTs), resolvers, and encoders, which are used for precise position measurement in robotic arms and CNC machines.
- Temperature Sensors: Thermocouples and thermistors are commonly used in systems requiring temperature control, like HVAC systems and automotive engines.
- Pressure Sensors: Employed in fluid systems and touch-sensitive technologies, they use piezoelectric materials or strain gauges for measurement.
- Proximity Sensors: These sensors, including ultrasonic, capacitive, and inductive types, are essential in automation for object detection and distance measurement.
Actuators: Actuators are the muscles of mechatronic systems responsible for motion and actuation based on signals from the control system. Like sensors, they vary widely:
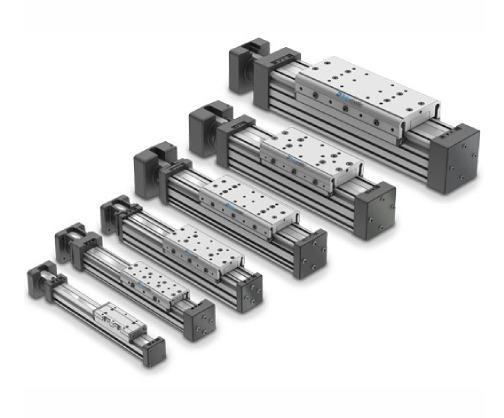
- Electric Motors: Used in many applications, from industrial machinery to consumer electronics, for precise and controlled motion.
- Hydraulic and Pneumatic Actuators: Common in heavy machinery, they use fluid dynamics to provide powerful and smooth motion.
- Piezoelectric Actuators: Known for their precision, they are used in applications requiring fine control, such as medical devices or micro-positioning systems.
Technical Aspects: The choice of sensors and actuators in a mechatronic system depends on several factors:
- Accuracy and Precision: Determining the level of detail and exactness required by the application.
- Environment and Durability: Considering factors like temperature range, humidity, and exposure to elements that might affect the sensor/actuator performance.
- Integration and Compatibility: Ensuring that the chosen components are compatible with the rest of the system regarding signal type, power requirements, and physical interfacing.
- Cost and Availability: Balancing the cost against the performance benefits and considering the availability of components for maintenance and repair.
In mechatronic design, the integration of sensors and actuators is crucial. It involves selecting the right type and configuring them to work in harmony with the control systems and mechanical components. This ensures that the system operates efficiently, responds accurately to inputs, and performs its intended function reliably.
Control Systems in Mechatronics
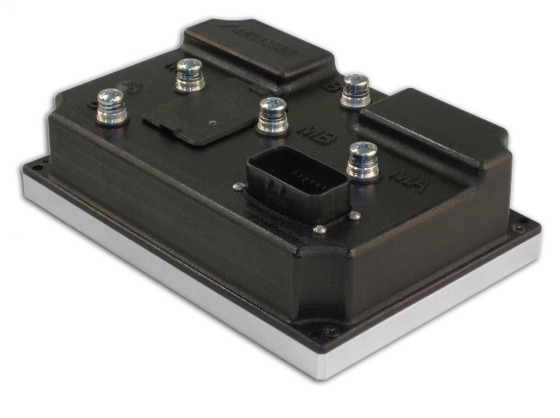
Basic Control Systems: At the heart of mechatronic systems lie control systems, which govern the operation of sensors and actuators based on the desired performance. Basic control systems include:
- On-Off Control: The simplest form of control, used in applications like thermostats, where the system switches on or off based on a set point.
- Linear Control Systems: These involve using linear feedback systems for applications where a proportional relationship between input and output is sufficient.
PID Controllers: Proportional-Integral-Derivative (PID) controllers are a cornerstone in control systems, offering a balance between complexity and capability. They are used extensively due to their effectiveness in a wide range of applications:
- Proportional (P) Control: Provides an output that is proportional to the current error (the difference between the desired and actual value).
- Integral (I) Control: Addresses the accumulated errors over time, helping to eliminate steady-state error.
- Derivative (D) Control: Predicts future errors based on the rate of change, improving the system’s responsiveness.
Advanced Control Systems: As the requirements of mechatronic systems grow more complex, advanced control methodologies are employed:
- Adaptive Control: Adapts to changing conditions and system dynamics. Useful in environments where parameters can shift over time, such as in aerospace applications.
- Intelligent Control Systems: Incorporate elements of artificial intelligence, such as neural networks and fuzzy logic, to handle non-linear, complex systems where traditional control methods fall short. These are used in advanced robotics and systems requiring sophisticated decision-making capabilities
Integration with Mechatronic Systems: In mechatronic design, integrating control systems effectivity is crucial. This involves:
- System Modeling and Simulation: Creating accurate models of the system to predict its behavior and fine-tune the control algorithms.
- Feedback and Feedforward Systems: Implementing feedback loops for self-correction and feedforward strategies for proactive adjustment.
- Interfacing with Sensors and Actuators: Ensuring seamless communication and response between the control system and the mechanical components.
Control systems in mechatronics are not standalone entities; they are deeply integrated with the system’s mechanical and electronic aspects. The choice between basic, PID, and advanced control systems depends on the application’s complexity, required precision, and the environmental conditions in which the system operates.
Data Acquisition in Mechatronics
This is the first step in the information chain of mechatronic systems. Data acquisition involves collecting raw data from sensors, ranging from simple temperature readings to complex images or sound waves. The key aspects include:
- Sampling and Quantization: Determining how often to sample the data and at what resolution directly impacts the system’s ability to capture and represent real-world phenomena accurately.
- Signal Conditioning: Filtering and amplifying signals to ensure they are suitable for processing. This may involve noise reduction, amplification, or conversion from analog to digital formats.
Signal Processing: Once data is acquired, the next step is to process these signals to extract meaningful information. Signal processing techniques vary based on the type of data and the desired outcome:
- Time-Domain Analysis: This is used for signals that vary over time, such as temperature or speed, and involves methods like filtering and time-series analysis.
- Frequency-domain analysis is useful for analyzing cyclic or periodic signals. It employs tools like Fourier transforms to understand the frequency content of signals.
- Feature Extraction and Data Fusion: Involves extracting key characteristics from complex data sets and combining data from multiple sensors to provide a more comprehensive understanding of the system’s state.
Data Analysis Techniques: Beyond processing, data analysis in mechatronics involves drawing conclusions and making decisions based on the processed data:
- Statistical Analysis: Employing statistical tools to interpret data, assess system performance, and make predictions.
- Machine Learning and AI: Advanced systems may use machine learning algorithms to identify patterns, make decisions, or predict future states, enhancing the system’s adaptability and intelligence.
Real-Time System Challenges: Many mechatronic systems require real-time data processing, which presents unique challenges:
- Latency and Throughput: Ensuring data is processed and responses are generated quickly enough to be relevant in real-time applications.
- Resource Constraints: Balancing the processing power and memory requirements with the system’s limitations, especially in embedded or portable applications.
- Reliability and Fault Tolerance: Developing systems that can handle errors or disruptions in data flow without significant performance degradation.
Data acquisition and processing are fundamental to the functionality of mechatronic systems, enabling them to respond intelligently and adaptively to their environment. The effectiveness of these processes directly influences the system’s efficiency, accuracy, and overall performance.
This article is original content created and posted by Electromate. Please do not re-post this content without prior approval from Electromate.
Related Story
A Guide to Mechatronics – Part 1: Introduction & Fundamentals
Mechatronics is a pivotal field that integrates mechanics, electronics, and computing, creating intelligent, adaptable, and versatile systems. It combines mechanical engineering precision, electronic control, and computer decision-making to innovate products and solutions. This interdisciplinary approach represents a shift from traditional engineering to a holistic method, leveraging each field’s strengths for efficient and sophisticated systems.
Mechatronics is crucial in modern engineering, evident in robotic arms, medical devices, autonomous vehicles, drones, and advanced electronics. The rise of IoT highlights its relevance, as it merges sensors, actuators, and communication technology. Mechatronics addresses pressing challenges like sustainable energy, advanced healthcare, and intelligent automation, optimizing systems for performance and efficiency.
This guide simplifies mechatronic subsystems for a broad audience, from students to professionals. It covers foundational aspects, demystifies sensors, actuators, and control systems, and emphasizes software’s role.